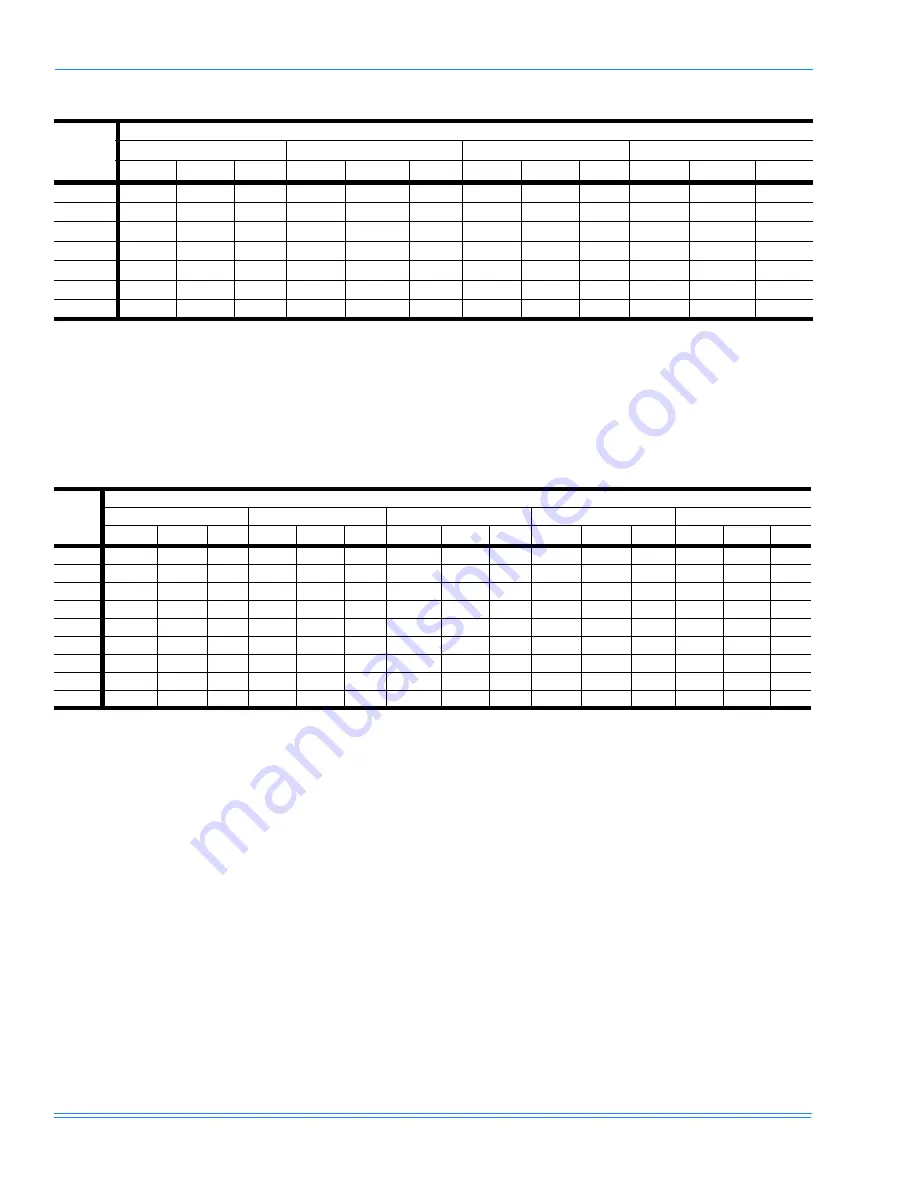
035-16626-000-E-0103
14
Unitary Products Group
POWER AND CONTROL WIRING
Install electrical wiring in accordance with the latest
National Electrical Code (NFPA standard No. 70) and/
or local regulations. The unit should be grounded in
accordance with these codes.
Route the power wires into the unit through the 1-3/8”
knockout in the rear panel, and connect them to the ter-
minals on blower motor contactor 10M. Route the con-
trol wires into the unit through the 7/8” hole in the rear
panel, and connect them to the terminals on block 4TB.
Refer to the unit drawing in Figures 17 and 18 for the
location of these knockouts.
If the unit includes and electric heat accessory, route
the power wires into heater control box in lieu of the
unit. Refer to the electric heat instruction PN 035-
16602-001 for additional installation information.
Refer to Tables 9 and 10 to size the disconnect switch,
the power wiring, the fuses and the control wiring.
Refer to Figure 11 for field wiring diagrams.
NOTE: Motors are wired for a 460V power supply.
Refer to the wiring diagram inside the motor
terminal box when reconnecting motor leads
for a 208 or 230 volt power supply.
TABLE 7: SUPPLY AIR PREFORMANCE FEH180
1
RPM
CFM
4800
5400
6000
6600
ESP
2
BHP
3
kW
4
ESP
2
BHP
3
kW
4
ESP
2
BHP
3
kW
4
ESP
2
BHP
3
kW
4
600
0.38
1.49
1.42
0.23
1.74
1.66
0.02
1.99
1.89
---
---
---
650
0.58
1.73
1.65
0.43
1.99
1.89
0.24
2.29
2.18
---
---
---
700
0.79
1.97
1.87
0.65
2.28
2.17
0.47
2.59
2.46
0.24
2.92
2.78
750
1.00
2.25
2.14
0.88
2.58
2.46
0.70
2.91
2.77
0.48
3.30
3.14
800
1.22
2.54
2.42
1.11
2.89
2.75
0.95
3.28
3.12
---
---
---
850
1.45
2.85
2.71
1.35
3.24
3.08
---
---
---
---
---
---
900
1.69
3.19
3.04
---
---
---
---
---
---
---
---
---
1.
Unit resistance based on a wet evaporator coil, clean filters, and unit tested in horizontal configuration.
2.
Available static pressure in IWG to overcome the resistance of the duct system and any accessories added to the unit. Refer to
the respective tables for the resistance of these accessories and for additional motor and drive data.
3.
Motors can be selected to operate into their service factor because they are located in the moving airstream, upstream of any
heating device.
4.
kW is based on 6% drive losses and a motor efficiency of 83.1%. Calculate kW by using the following formula: kW = (746 X BHP
X DRIVE LOSSES) / (1000 X MOTOR EFFICIENCY)
TABLE 8: SUPPLY AIR PERFORMANCE FEH240
1
RPM
CFM
6400
7200
8000
8800
9600
ESP
2
BHP
3
kW
4
ESP
2
BHP
3
kW
4
ESP
2
BHP
3
kW
4
ESP
2
BHP
3
kW
4
ESP
2
BHP
3
kW
4
600
0.15
1.49
1.42
-
-
-
-
-
-
-
-
-
-
-
-
650
0.31
1.71
1.63
0.14
2.00
1.90
-
-
-
-
-
-
-
-
-
700
0.49
1.95
1.86
0.32
2.27
2.16
0.12
2.63
2.50
-
-
-
-
-
-
750
0.67
2.21
2.10
0.51
2.56
2.44
0.32
2.92
2.78
0.10
3.35
3.19
-
-
-
800
0.85
2.50
2.38
0.70
2.85
2.71
0.52
3.25
3.09
0.31
3.70
3.52
0.07
4.20
4.00
850
1.05
2.80
2.66
0.91
3.19
3.04
0.74
3.61
3.44
0.53
4.07
3.87
0.29
4.62
4.40
900
1.25
3.11
2.96
1.12
3.55
3.38
0.96
3.99
3.80
0.76
4.51
4.29
0.53
5.07
4.82
950
1.46
3.46
3.29
1.34
3.92
3.73
1.18
4.43
4.22
1.00
4.97
4.73
0.78
5.53
5.26
1000
1.67
3.82
3.64
1.56
4.33
4.12
1.42
4.88
4.64
1.24
5.44
5.18
-
-
-
1.
Unit resistance is based on a wet evaporator coil, clean filters, and unit tested in horizontal configuration.
2.
Available static pressure in IWG to overcome the resistance of the duct system and any accessories added to the unit. Refer to
the respective tables for the resistance of theses accessories and for additional motor and drive data.
3.
Motors can be selected to operate into their service factor because they are located in the moving air stream, upstream of any
heating device.
4.
kW is based on 6% drive losses and a motor efficiency of 83.1%. Calculate kW by using the following formula:
kW = (746 X BHP X DRIVE LOSSES) / (1000 X MOTOR EFFICIENCY)