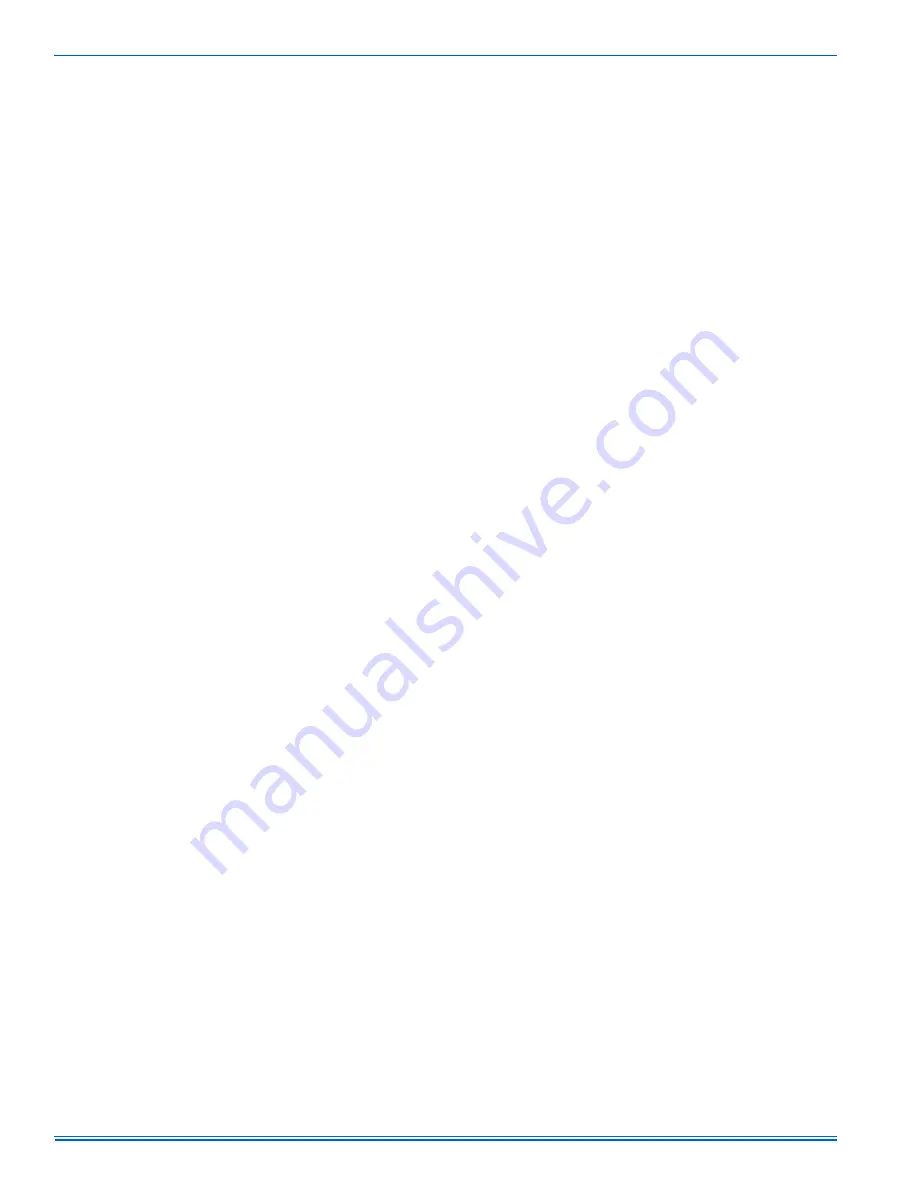
271043-UIM-B-0707
24
Unitary Products Group
Heating and Cooling Airflow
The heating and the cooling airflows are preset at the factory. The heat-
ing airflow is set to the maximum CFM. The cooling airflow is set to pro-
vide 90 percent of the maximum CFM. The heating and cooling airflows
must be field adjusted to match the HVAC system at installation. See
Table 17 for the HEAT, COOL and ADJ jumper settings to use for spe-
cific airflows.
CFM Board - Delay Taps Selection
The set of jumper pins on the control board labeled "DELAY" are used
to set the delay profiles for the furnace. These can be chosen so as to
maximize the comfort and sound levels for various regions of the coun-
try.
Tap A
is the default profile. It provides a 30-second ramp-up from zero
airflow to full capacity and a 30-second ramp-down from full capacity
back to zero airflow. Whenever there is a change in airflow mode, such
as from low heat to high heat, the motor will take 30 seconds to ramp
from one speed to the other.
Tap B
is the humid profile. This profile is best-suited for installations
where the humidity is frequently very high during cooling season, such
as in the southern part of the country. On a call for cooling, the blower
will ramp up to 50% of full capacity and will stay there for two minutes,
then will ramp up to 82% of full capacity and will stay there for five min-
utes, and then will ramp up to full capacity, where it will stay until the
wall thermostat is satisfied. In every case, it will take the motor 30 sec-
onds to ramp from one speed to another.
Tap C
is the dry profile. This profile is best suited to parts of the country
where excessive humidity is not generally a problem, where the sum-
mer months are usually dry. On a call for cooling the motor will ramp up
to full capacity and will stay there until the thermostat is satisfied. At the
end of the cooling cycle, the blower will ramp down to 50% of full capac-
ity where it will stay for 60 seconds. Then it will ramp down to zero. In
every case, it will take the motor 30 seconds to ramp from one speed to
another.
Tap D
is the normal profile, best suited for most of the country, where
neither excessive humidity nor extremely dry conditions are the norm.
On a call for cooling, the motor will ramp up to 63% of full capacity and
will stay there for 90 seconds, then will ramp up to full capacity. At the
end of the cooling cycle, the motor will ramp down to 63% of full capac-
ity and will stay there for 30 seconds, then will ramp down to zero. In
every case, it will take the motor 30 seconds to ramp from one speed to
another.
Continuous Blower Operation
The blower will run continuously whenever the wall thermostat fan
switch is in the "ON" position. The furnace blower will run at the speed
selected on the "FAN SPEED" jumpers on the main control board (HI
COOL, LO COOL, HI HEAT or LO HEAT). When the jumper is in the
"VS G" position, the blower will run at 50% of the high cool speed.
Intermittent Blower Cooling
On cooling/ heating thermostats with a fan switch, when the fan switch
is set in the auto position and the thermostat calls for cooling, a circuit is
completed between the R, Y and G terminals. The motor is energized
through the Y1 cool terminal and runs on the speed selected on the
COOL tap of the control board. The fan off setting is fixed at 60 seconds
for SEER enhancement. The control board can accommodate two-
stage cooling. When a two-stage cool thermostat is connected to the Y1
and Y2 terminals on the board, the blower will operate on LOW COOL
speed when Y1 is energized and on HI COOL speed when Y1 and Y2
are energized.
Intermittent Blower Heating
On cooling/ heating thermostats with a fan switch, when the fan switch
is set in the auto position and the thermostat calls for heating, a circuit is
completed between the R and W terminals. The indoor fan motor is
energized through the W1 heat terminal and runs on the speed selected
on the HEAT tap of the control board.
Humidistat
When a humidistat is installed in the system, the “Humidistat Installed?”
jumper on the control board should be moved to the “YES” position. The
cooling CFM will then be reduced by 15% whenever the humidistat indi-
cates high humidity.
FURNACE CONTROL DIAGNOSTICS
The furnace has built-in, self-diagnostic capability. If a system problem
occurs, a blinking LED shows a fault code. The LED can flash red,
green or amber to indicate various conditions. It is located behind a
clear view port in the blower compartment door.
The control continuously monitors its own operation and the operation
of the system. If a failure occurs, the LED will indicate the failure code. If
the failure is internal to the control, the light will stay on continuously. In
this case, the entire control should be replaced, as the control is not
field repairable.
Flash sequence codes 1 through 10 are as follows: LED will turn “on”
for 1/4 second and “off” for 1/4 second. This pattern will be repeated the
number of times equal to the code. For example, six “on” flashes equals
a number 6 fault code. All flash code sequences are broken by a 2 sec-
ond “off” period.
SLOW GREEN FLASH:
Normal operation.
SLOW AMBER FLASH:
Normal operation with call for heat.
RAPID RED FLASH:
Twinning error, incorrect 24V phasing. Check
twinning wiring.
RAPID AMBER FLASH:
Flame sense current is below 1.5 microamps.
Check and clean flame sensor. Check for proper gas flow.
4
AMBER FLASHES:
The control board is recieving a “Y” signal from
the thermostat without a “G” signal, indicating improper thermostat wir-
ing.
1 RED FLASH:
This indicates that flame was sensed when there was
not a call for heat. With this fault code the control will turn on both the
inducer motor and supply air blower. A gas valve that leaks through or
is slow closing would typically cause this fault.
2 RED FLASHES:
This indicates that the normally open pressure
switch contacts are stuck in the closed position. The control confirms
these contacts are open at the beginning of each heat cycle. This would
indicate a faulty pressure switch or miswiring.
3 RED FLASHES:
This indicates the normally open pressure switch
contact did not close after the inducer was energized. This could be
caused by a number of problems: faulty inducer, blocked vent pipe, bro-
ken pressure switch hose or faulty pressure switch.
4 RED FLASHES:
This indicates that a primary or auxiliary limit switch
has opened its normally closed contacts. With this fault code the control
will operate the supply air blower and inducer. This condition may be
caused by: dirty filter, improperly sized duct system, incorrect blower
speed setting, incorrect firing rate or faulty blower motor.
5 RED FLASHES:
This fault is indicated if the normally closed contacts
in the rollout switch opens. The rollout control is manually reset. If it has
opened, check for proper combustion air, proper inducer operation, and
primary heat exchanger failure or burner problem. Be sure to reset the
switch after correcting the failure condition.
6 RED FLASHES:
This indicates that after the unit was operating, the
pressure switch opened 4 times during the call for heat. If the main
blower is in a “Delay on” mode it will complete it, and any subsequent
delay off period. The furnace will lock out for one hour and then restart.
7 RED FLASHES:
This fault code indicates that the flame could not be
established. This no-light condition occurred 3 times (2 retries) during
the call for heat before locking out. Low gas pressure, faulty gas valve,
faulty hot surface ignitor or burner problem may cause this. The furnace
will lock out for one hour and then restart.
8 RED FLASHES:
This fault is indicated if the flame is lost 5 times (4
recycles) during the heating cycle. This could be caused by low gas
pressure or faulty gas valve. The furnace will lock out for one hour and
then restart.