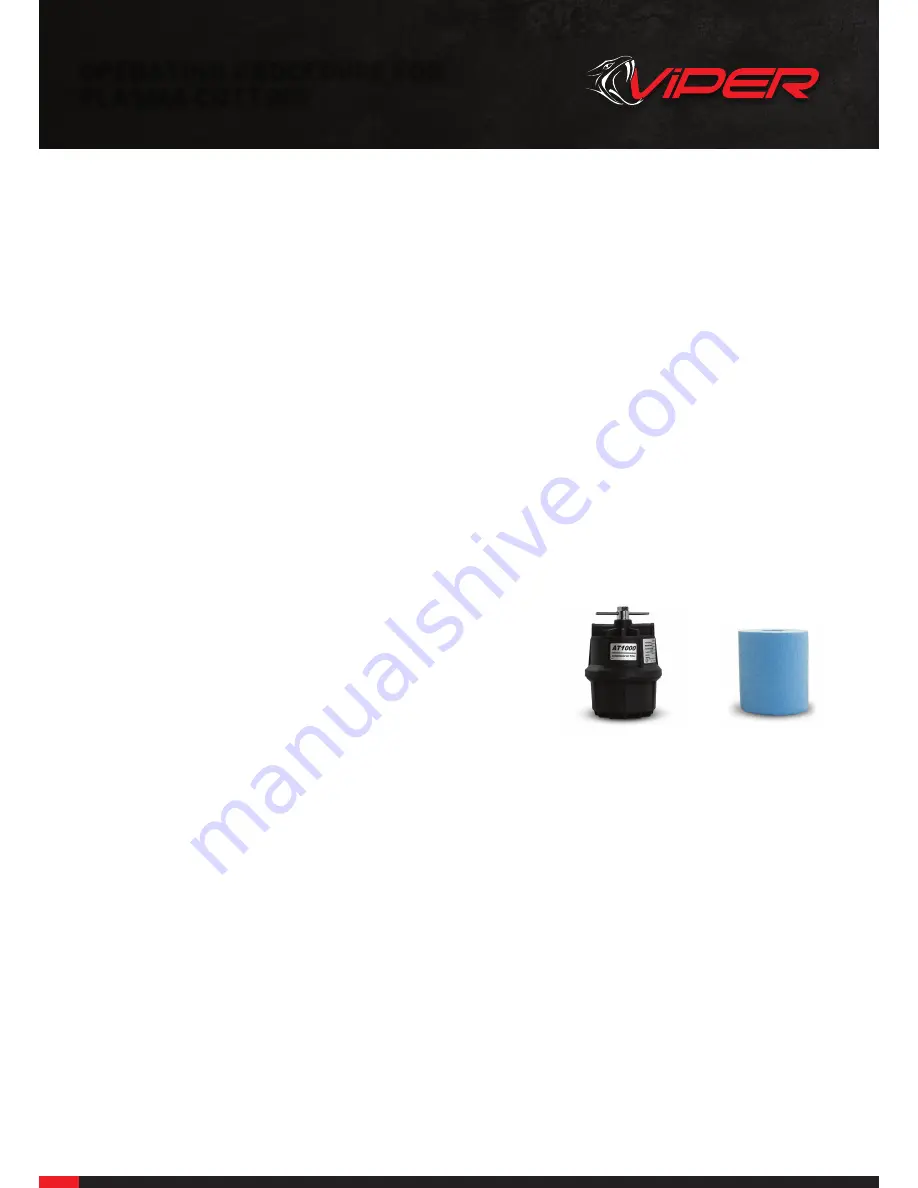
14
| Viper Cut 30 Manual
13
Operating Procedure & Techniques for PLASMA Cutting
●
Air pressure and volume
Air pressure,
ow rate and air quality are critical to quality plasma cutting and consumable life span.
The required air pressure and volume can vary from model to model and the manufacturer will provide the specs.
The volume capacity of your
compressor is important, if you have a small compressor with exactly the same l/min rating as the
plasma, then the compressor
will run continuously when you are plasma cutting, a compressor with a l/min rating slightly higher
than the plasma would be more
adequate. If you are doing a lot of cutting, cutting thick plate (same air consumption but slower
slower cut speeds = longer cut time) then
choose a compressor at 1.5 to 2 times the plasma system requirement.
●
Air quality
Good air quality is essential to quality plasma cutting and consumable life span.
Compressors take in air at atmospheric pressure and increase the pressure and store it in a tank. Humidity in the air is condensed
in the tank and in the airlines producing water, more so in humid environments. Moisture that forms in air lines has a tendency
to condense into larger drops when the air pressure decreases as it is entering the plasma torch. When these droplets enter into
the high temperatures (as much as 11,000
°
C) in the plenum of the torch, they immediately break down into oxygen and hydrogen,
which alters the normal chemical content of air in the torch. These elements will then dramatically change the plasma arc which
causes the torch consumable parts to wear very quickly, alters the shape of the nozzle ori
ce, dramatically affecting cut quality in
terms of edge squareness, dross formation, and edge smoothness. Minimising the moisture in the air supply is absolutely critical to
quality plasma cuts and longevity of consumable parts. As a minimum be sure to drain the receiver (tank) on the air compressor at
least daily.
Most air plasma systems from reputable manufacturers have an on board particulate
lter and or a coalescing
lter with an auto
drain that will remove some moisture from the air supply. For home workshop and light industrial users the on board air
lter is
adequate. Most situations however will require additional
ltration to prevent moisture from affecting the quality of the plasma cutter
and in most cases it is recommended to install a sub micronic particulate
lter that is designed to trap water through absorption.
This style of
lter has a replaceable
lter cartridge that absorbs water and must be changed after it is near saturation, it should be
installed close as possible to the air intake of the plasma cutter.
●
Technique Tips
•
It is easier to pull the torch through the cut than to push it.
•
To cut thin material reduce the amperage until you get the best quality cut.
•
Use the correct size tip ori
ce for the amperage being used.
•
For Straight cuts use a straight edge or cutting buggy as a guide. For circles, use a template or circle cutting attachment.
•
Check that the front end consumable parts of the plasma cutting torch are in good condition.
Sub Micronic Filter
Filter Element
●
Starting a cut
Hold the torch vertical at the edge of the
work piece
Pull the trigger to start the pilot arc.
The cutting arc will initiate when the torch
tip is close enough to the work piece. Start
cutting on the edge until the arc has cut
completely through.
Then, proceed with the cut.
●
Hand torch cutting technique
When cutting make sure that sparks are
exiting from the bottom of the work piece.
If sparks are spraying up from the work
piece, you are moving the torch too fast, or
you don't have enough amps set.
Hold the torch vertical and watch the arc as
it cuts along the line.
AIR PRESSURE AND VOLUME
Air pressure, flow rate and air quality are critical to quality plasma cutting and consumable life span. The required air pressure and volume can vary from
model to model and the manufacturer will provide the specs. The Viper Cut 30 air pressure must be adjusted and set to 0.5MPA (75psi) and requires a
flow rate of 190 l/min. The volume capacity of your compressor is important, if you have a small compressor with exactly the same l/min rating as the
plasma, then the compressor will run continuously when you are plasma cutting, a compressor with a l/min rating slightly higher than the plasma would
be more adequate. If you are doing a lot of cutting, cutting thick plate (same air consumption but slower cut speeds = longer cut time) then choose a
compressor at 1.5 to 2 times the plasma system requirement.
AIR QUALITY
Good air quality is essential to quality plasma cutting and consumable life span.
Compressors take in air at atmospheric pressure and increase the pressure and store it in a tank. Humidity in the air is condensed in the tank and in
the airlines producing water, more so in humid environments. Moisture that forms in air lines has a tendency to condense into larger drops when the air
pressure decreases as it is entering the plasma torch. When these droplets enter into the high temperatures (as much as 11,000°C) in the plenum of the
torch, they immediately break down into oxygen and hydrogen, which alters the normal chemical content of air in the torch. These elements will then
dramatically change the plasma arc which causes the torch consumable parts to wear very quickly, alters the shape of the nozzle orifice, dramatically
affecting cut quality in terms of edge squareness, dross formation, and edge smoothness. Minimising the moisture in the air supply is absolutely critical
to quality plasma cuts and longevity of consumable parts. As a minimum be sure to drain the receiver (tank) on the air compressor at least daily.
Most air plasma systems from reputable manufacturers have an on board particulate filter and or a coalescing filter with an auto drain that will remove
some moisture from the air supply. For home workshop and light industrial users the on board air filter is adequate. Most situations however will require
additional filtration to prevent moisture from affecting the quality of the plasma cutter and in most cases it is recommended to install a sub micronic
particulate filter that is designed to trap water through absorption. This style of filter has a replaceable filter cartridge that absorbs water and must be
changed after it is near saturation, it should be installed close as possible to the air intake of the plasma cutter.
TECHNIQUE TIPS
• It is easier to pull the torch through the cut than to push it.
• To cut thin material reduce the amperage until you get the best quality cut.
• Use the correct size tip orifice for the amperage being used.
• For Straight cuts use a straight edge or cutting buggy as a guide. For circles, use a template
or circle cutting attachment.
• Check that the front end consumable parts of the plasma cutting torch are in good condition.
OPERATING PROCEDURE FOR
PLASMA CUTTING
Содержание Viper Cut 30
Страница 21: ...Viper Cut 30 Manual 21 NOTES...
Страница 22: ...22 Viper Cut 30 Manual NOTES...
Страница 23: ...Viper Cut 30 Manual 23 NOTES...