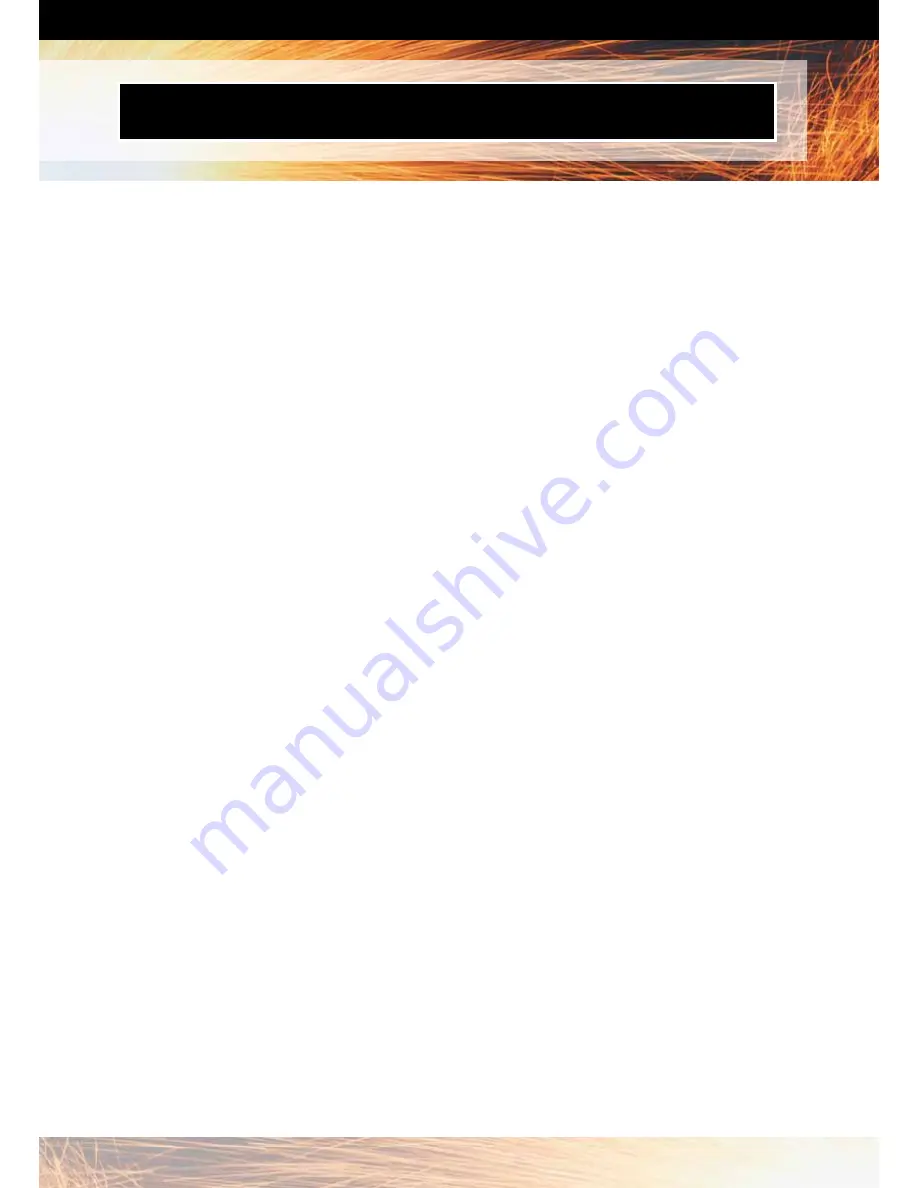
1
INSTRUCTION MANUAL FOR UNI-FLAME
GAS WELDING, FLAME CUTTING AND GOUGING KIT
UNI-FLAME GAS WELDING EQUIPMENT
Dear customer,
Congratulations on your excellent choice of oxy/acetylene welding and cutting equipment.
The
UNI-FLAME
range of gas welding and cutting equipment has been rigorously tested by independent laboratories and con-
form to the following
AUSTRALIAN STANDARDS
for gas welding and cutting processes:
Regulators
AS4267 including the
PROMOTED IGNITION TEST
Gas hose
AS1335
Flash arrestors
AS4603
This manual refers to safety measures that must be adhered to for safe operation of your Uni-Flame gas cutting and welding
equipment. Please read and understand these warnings and instructions before use. Failure to do so could result in serious
injury or death. Uni-Flame gas cutting and welding equipment should only be used by operators who are properly trained and
qualified in the safe use of this type of equipment.
Technical information in this Instruction Manual is based upon information available in two Expert Technology Tools published
by the Welding Technology Institute of Australia (WTIA):
WTIA Technical Note 5 Flame cutting of steels (1996)
WTIA Technical Note 7 Health and safety in welding (2004)
Further information and copies of these publications, and technical support in welding and related activities, are available from
WTIA Tel: +61 (0)2 9748 4443 Fax; +61 (0)2 9748 2858 or email [email protected]. For information about other publications
and the activities of the WTIA and WGA visit www.wtia.com.au. or www.unimig.com.au
General Safety Information
Safety consideration for both the operator and his surroundings must be given to the heat source produced by mixing
compressed oxygen with a fuel gas and igniting the resulting mixture.
When using any of these processes, particular safety considerations apply in respect of:
a)
Burns from flames, hot objects, malfunctioning hand-held equipment, molten particles etc.
b)
Explosion from mixed gas concentrations created by fuel gas leakage from cylinders, bulk supplies, hoses, welding
equipment breakable connections, etc.
c)
Fire caused by ignition of flammable materials, leakage of fuel gases, contact with hot slag, welding equipment in
poor condition etc. Plant, buildings, ship and bush fires have occurred.
d)
Ignition of materials not normally considered flammable due to oxygen enrichment
e)
Violent rupture or explosion of components due to being pressurised beyond their design pressures.
f)
Asphyxiation due to displacement of atmospheric, breathable air by inert or toxic gases, e.g. leakages in confined
spaces or lack of oxygen resulting from excessive rusting in confined spaces
g)
Radiation damage (to eyes principally and other exposed surfaces).
h)
Fumes originating from the particular materials being welded, heated or cut.
i)
Electric shock which could result when gas welding or cutting on cables or other conductors at high voltage.
j)
Influence on the workplace from the above hazards (containers, vessels, heights, etc).
Gas Properties and Particular Hazards
Gases Used
The flames used in gas welding, cutting and allied processes are obtained by the ignition of mixtures of oxygen and
appropriate fuel gases, the most common being acetylene and LPG.
All of these fuel gases, especially when mixed with compressed oxygen, are capable of releasing very large amounts of energy
in the form of heat or explosion, requiring minimum energy to start the reaction.
Consequently, they should be treated with great care and in accordance with well defined safety procedures.
Some industrial gases may be flammable, oxidising, toxic or corrosive, and users need to take special precautions in handling
them. Users should always have on hand Material Safety Data Sheets, normally available from Gas Suppliers, for each of the
gases stored and used at any location.