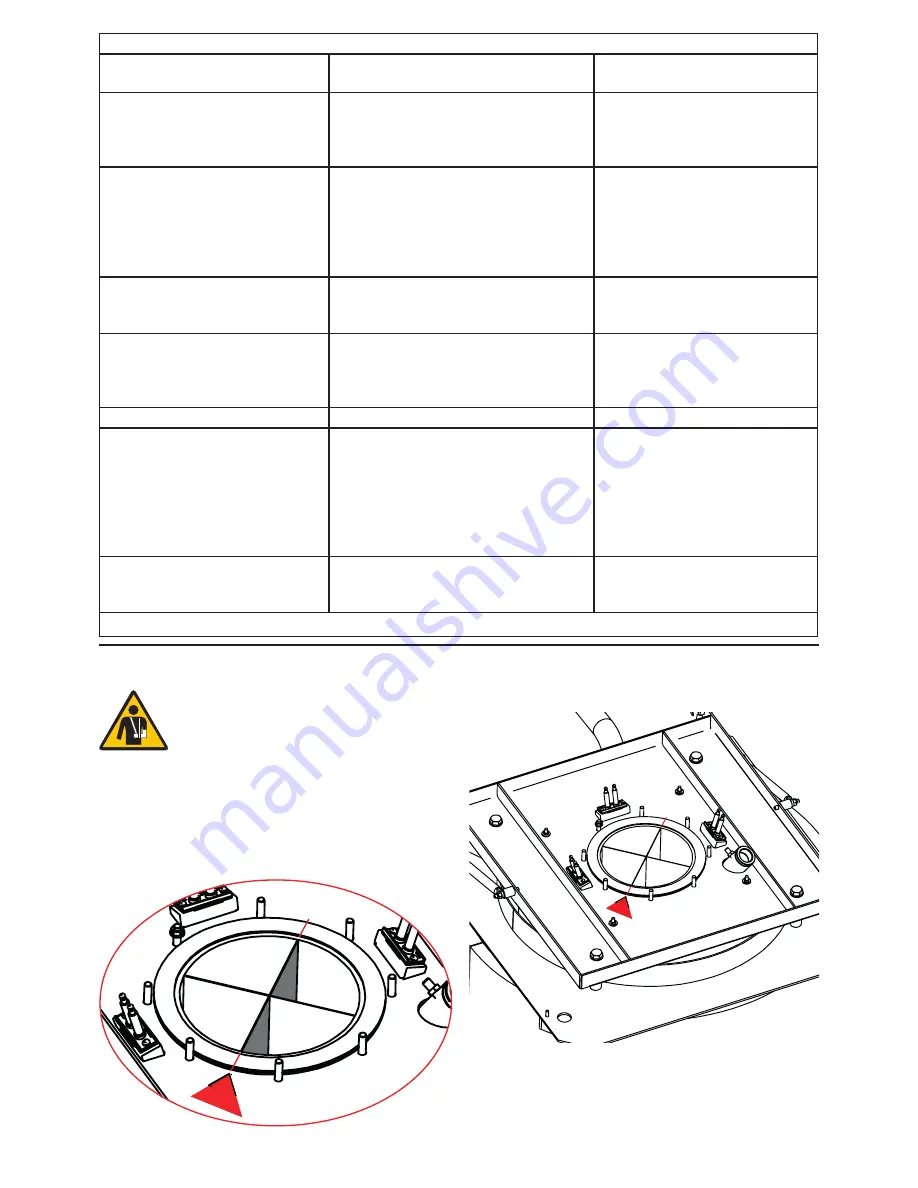
34
ROUTINE YEARLY VERIFICATION OPERATIONS
COMPONENT:
VERIFY:
CONTROL/INTERVENTION METH-
OD:
VG
(Gas valve)
( 3 )
does the valve modulate properly?
the check is carried out in “calibration”
mode, requesting 100% , 50%, and
minimum modulation percentage.
Check the modules flame.
SM (flow sensor)
( 11 )
do the sensors maintain the
original characteristics?
12571 ohm at 20° c / 1762 ohm at
70° c.
measurement to be taken with the
wires disconnected (see table Res/
temp)
.
E Acc (ignition electrode
( 28 )
does the discharge of sparks before
putting the boiler in safe conditions last less
than 3 sec.?
detach the electrode ionisation wire
and check the securing time.
tL (anti-overheating
limit thermostat)
( 10 )
(51) (Chap.3.9)
does the tL put the boiler in safety conditions
when overheating?
Heat the tL until it intervenes at 102°c
and check that it intervenes at 102°.
condensation drain trap
(27)
Has the trap got deposits on the bottom?
clean the trap with water.
Heat exchanger body
If SL places the boiler in safety mode in the
event of condensate level increases
If PF places the boiler in safety mode in the
event of flue gas exhaust clogging
check/Remove any deposits in the
combustion chamber using a vacuum
cleaner, then wash the heat exchang-
er body with water and check proper
draining of the smoke chamber and
siphon / remove any obstructions from
the flue gas side.
Burner
( 5 )
check the state of cleanliness of the burner
mesh
Remove any deposits using com-
pressed air, blowing from the mesh
side.
( Num ) =
see key Par. 2.2
ATTENTION:
After executing maintenance operations
, it is
essential to assemble
the burner correctly.
A
- Insert gasket
1
B
- direct the burner
2
as indicated in the drawing
(incision in the shape of an arrow on the door
must correspond to the burner's fins)
C
- Insert the gasket
3
POSITIONING AND REASSEMBLING THE BURNER