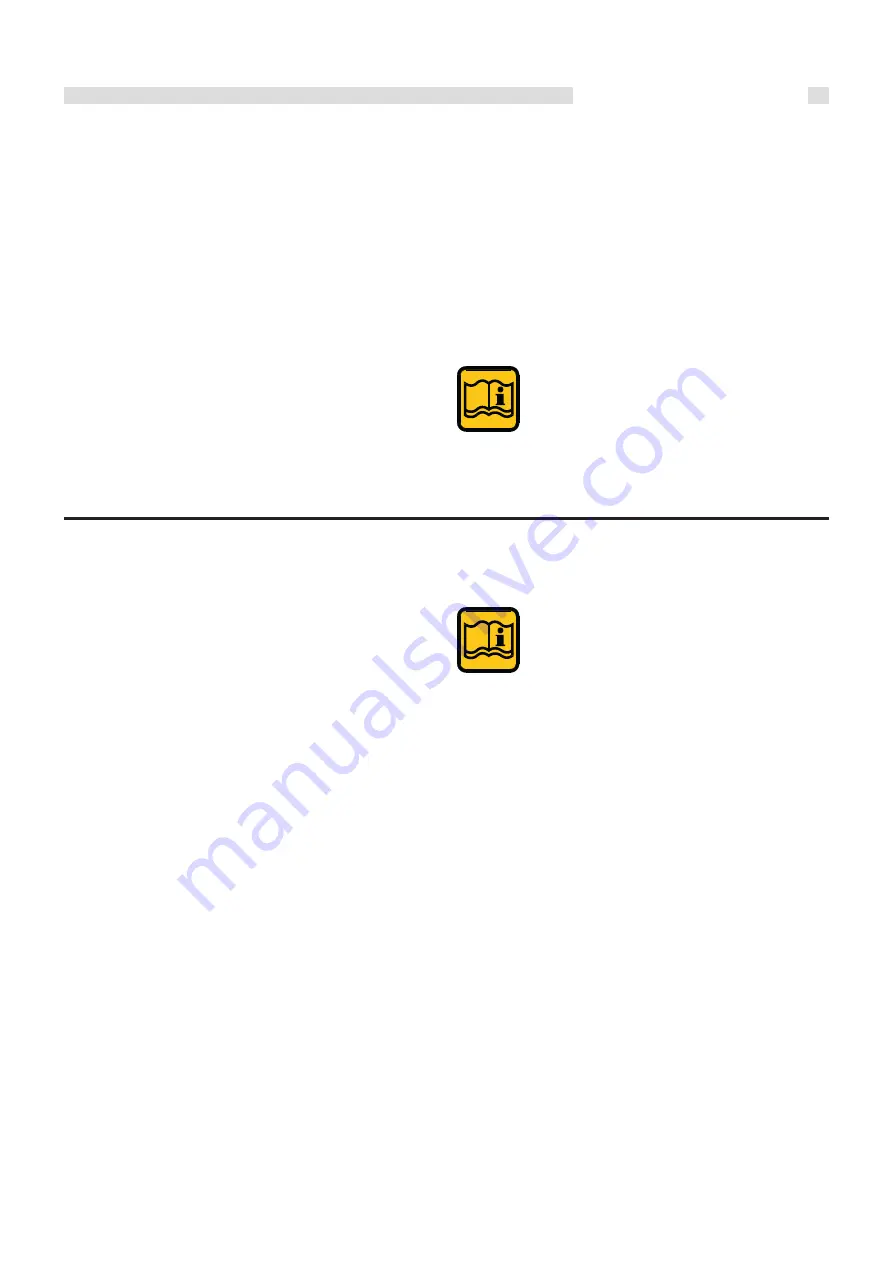
5
General Information
When the appliance is installed on existing systems, ensure
yourself that:
-
The flue outlet pipe is suitable for condensing boilers, for
the temperature of the products of combustion, calculated
and manufactured according to the regulations in force. It
must be installed as much as possible in a straight line,
tested for soundness, insulated and must not have any
occlusions or restrictions.
-
The flue outlet pipe has a connection for the discharge of
condensate.
- The boiler room has a suitable outlet for the discharge of
condensate produce by the boiler.
-
The electrical system has been fitted in compliance to the
specific norms and the work has been carried out by a
competent person.
-
The circulation pump’s output, the head and flow direction
are suitable.
- The gas feeding supply pipe and the eventual tank are
constructed according to the regulations in force.
- The expansion vessels assure the total absorption of the
dilatation of the fluid contained in the system.
- The system has been cleaned of impurities and lime scale.
When a Modulex boiler is installed onto an existing
heating system:
In case the replacement of an existing boiler in an old system can
be programmed, it
is necessary to thoroughly
clean out the system with a basic solution.
The system must be cleaned 4 weeks before
the substitution, with the system firing at a
temperature of 35°C to 40°C.
WARNING!
If it is noticed that a new Modulex has replaced,
in an old system the existing boiler without having first perfor-
med what said in the previous paragraph, Do not wash now
the system, as residual products, present in the circuit, could
lead to system gathering in the boiler body, causing damage.
UNICAL recommends contacting a specialised company for
water treatment.
Instead, if installing a Modulex boiler in a new system, it is
still recommended to thoroughly clean out the system with an
adequate product and fit a Y filter with two isolating valves onthe
boiler’s return pipe, so that, when necessary, it can be cleaned.
This filter will protect the boiler from the dirt coming from the
heating system.
When sizing pumps, it is necessary to take into consideration
the pressure losses which occurin the primary circuit.
1.6 - INSTALLATION ON EXISTING HEATING SYSTEMS
1.5 - STANDARD CODES FOR
INSTALLATION
The appliance must be installed in compliance to the instructions
contained in this manual.
The installation must be carried out by a competent qualified
engineer, whom will assume the responsibility of complying to
all the local and/or national regulations published in the official
publications, as well as all the applicable codes of practice.
Before installing the appliance please contact the gas supply
company.
The installation must be carried in accordance to the codes of
practice, the regulations and the requirements hereby indicated
which constitute an indicative list, but not a complete one, as
these continue to undergo evolve devolpments.
Moreover, the boiler must be installed in accordance to all the
regulations regarding the boiler room, the building regulations
and the prescriptions regarding central heating plants in force
in the country where the boiler is installed.
The appliance must be installed, commissioned and serviced
according to the regulations in force. This is also valid for the
hydraulic system, the flue outlet system and the boiler location
room.
Failure to comply with these rules will
nullify the warranty
Содержание MODULEX EXT 100
Страница 1: ...E N G L I S H 100 150 200 250 300 350 INSTALLATION AND SERVICING INSTRUCTIONS MODULEX EXT ...
Страница 32: ...32 Instructions for the installer THERMOSTAT FBR 2 CONNECTION room sensor ...
Страница 33: ...33 Instructions for the installer MODULATING THERMOSTAT CONNECTIONS ...
Страница 35: ...35 Instructions for the installer ...
Страница 37: ...37 Instructions for the installer Sensor terminal assignments Terminal assignments BCM ...