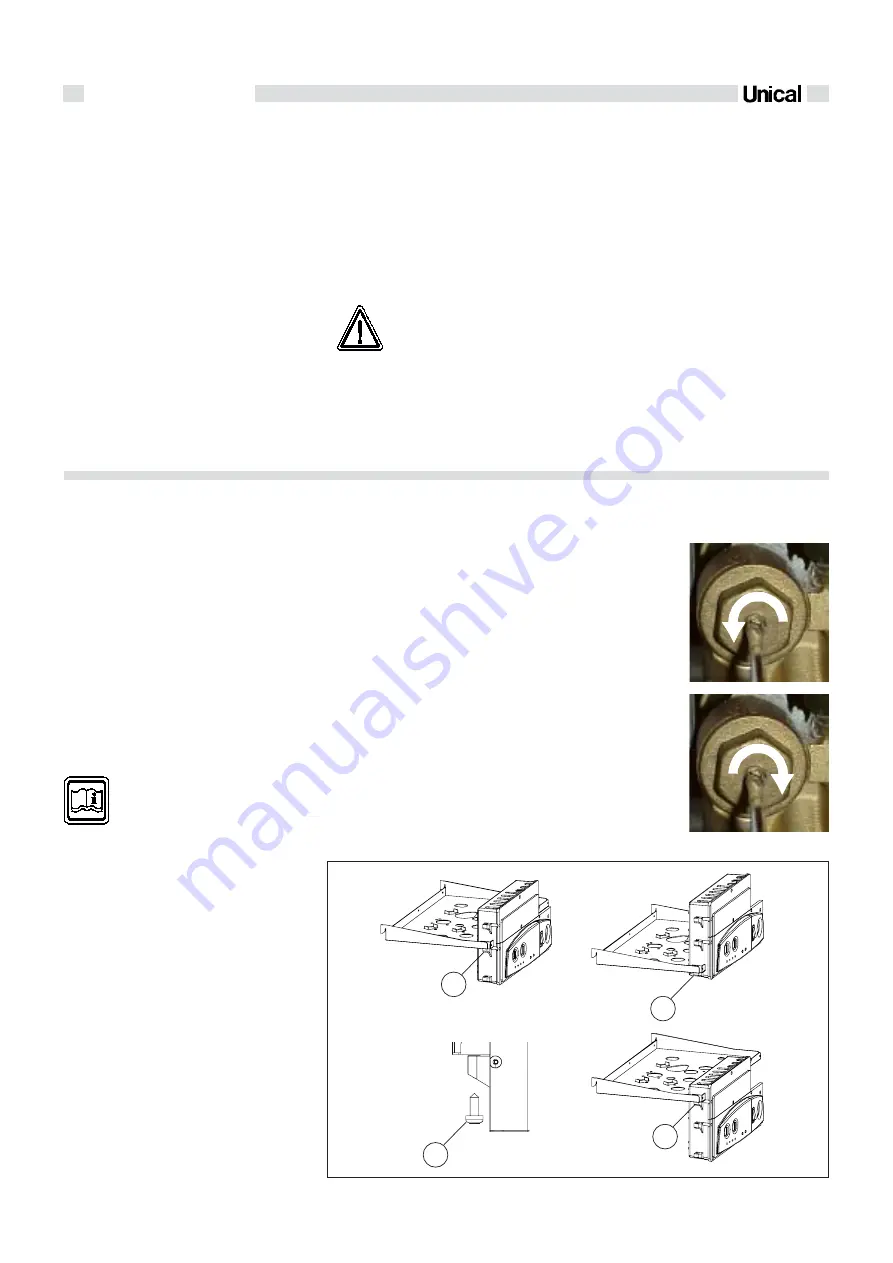
20
Installation info
2.2.12 -
CONNECTION TO THE GAS
MAINS
The supply pipe must have a section which is
the same as or greater than the one used in
the boiler.
Comply with the applicable local installation
requirements which shall be considered as
having been incorporated in full in this ma-
nual.
Before opening the internal gas supply system;
i.e. before connecting the gas meter, all seals
must be checked.
If any part of the system is concealed the seals
must be checked before the pipes are cove-
red.
The seal test must be conducted using air or
nitrogen at a pressure of at least 100 mbar.
The commissioning of the boiler also inclu-
des the following operations and checks:
-
Opening of the gas gate valve and venting
2.2.13 - HYDRAULIC CONNECTION
Before installing the boiler we recommend that
the system be cleaned to remove any impuri-
ties which could originate from components
and which could risk damaging the circulating
pump and heat exchanger.
Note: The use of solvents could damage
the components of the heating cir-
cuit.
PRELIMINARY OPERATIONS:
Act on the coupled spring (located in the lower
part) and remove the two screws (located in
the upper part) in order to remove the casing.
fig. 21
of the air contained in the piping and ap-
pliances, proceding appliance by applian-
ce
-
Check, with the gate valve of all the ap-
pliance Off, that there are no gas leaks.
During the 2
nd
quarter of a hour from the
beginning of the test no pressure reduc-
tion is to be detected on the gas pressure
Move the control panel in the high position for
the hydraulic connection. Remove the three
screws
"A"
fixing the panel and then place
the panel in correspondence to the low holes
"B"
and fix the panel.
After having carried out the connections, re-
store the panel's normal position.
HEATING
The heating flow and return must be connected
to the relevant ¾” connections of the boiler
M
and
R
(see fig. 7).
When determining the size of the heating cir-
cuit pipes it is essential to bear in mind the
pressure losses induced by radiators, any ther-
mostatic valves, radiator cut-off valves and
the configuration of the system.
In the boiler, onto a bass group positioned,
between the flow and return an automatic by-
pass device is fitted (about a differential val-
ve with a flow rate of about 150 l/h) which gua-
fig. 22
A
B
C
D
To OPEN the
By-pass
rotate the screw
anti-clockwise
To CLOSE the
By-pass
rotate the
screw
clockwise
Note:The control panel can be mo-
ved in two positions beyond the nor-
mal position
‘’D’’
, that is to say high
and low position, in order to make
the maintenance operations easy.
rantees always minimum flow rate throught
the heat exchanger, also in the case, for in-
stance, that all the thermostatic valves fitted
on the radiators, are closed. It is possible to
adjust the by-pass by acting onto the adju-
sting screw (see fig. 21)
We recommend that the discharge of the sa-
fety valve mounted in the boiler be conveyed
into the sewer.
If this precaution is not taken, activation of
the safety valve may result in flooding of the
room where the boiler is installed.
UNICAL shall not be held responsible for da-
mage caused by non-observance of this tech-
nical precaution.
D.H.W.
Outlet and inlet of D.H.W. must be connected
to the relevant ½” connections of the boiler
C
and
F
(see fig. 7).
The hardness of the supply water affects the
frequency of the cleaning of the heat exchan-
ger.
gauge. If gas leaks have to be found, use
only water soap solution or any other spe-
cific gas leak detector which can be avai-
lable on the market. Never look for gas le-
aks using a nacked flame.
While connecting gas inlet pipe of the boiler to the pipe coming from
gas network, it is MANDATORY to insert a TIGHT GASKET, whose
dimensions and material must be adequate. Connection is NOT sui-
table for hemp, teflon strip or similar materials
AVVERTENZA!
Содержание EVE 05 CTFS 24 F
Страница 35: ...35 ...