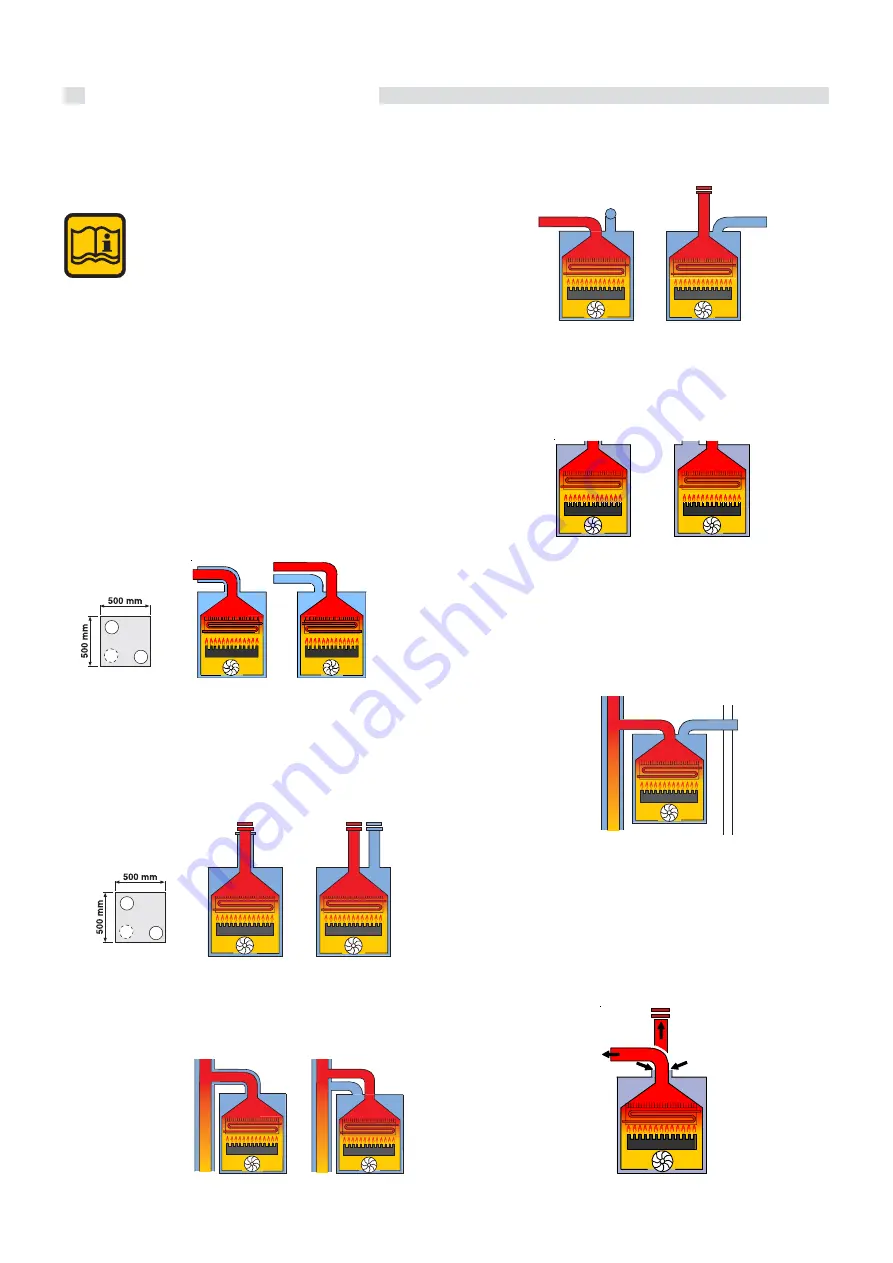
20
Instruction for the installer
3.12 - FLUE OUTLET INSTALLATION
The flue system must be installed in accordance with the
local and national Standards (refer to Standard UNI-CIG
7129, point 4 and UNI-CIG point 5)
.
We recommend using only original UNICAL flue
outlet systems.
Damages caused by installation errors and for
non-observance of the instructions given by
the same manufacturer will invalidate all the
supplier’s contractual or extra contractual
responsibilities.
If the boiler has to be replaced ALWAYS replace the flue
outlet system.
The boiler has been approved for the following flue
configurations:
C13
oiler designed for connection to horizontal inlet and ou-
tlet terminals, which admit fresh air to the burner and
discharge the products of combustion to the outside
through concentric or twin ducts.
The minimum distance between the inlet air duct and
the flue outlet duct must be of 250 mm and both terminals
must be positioned within a 500 mm square section.
C33
Boiler designed for connection to vertical inlet and out-
let terminals, which admit fresh air to the burner and
discharge the products of combustion to the outside
through concentric or twin ducts.
The minimum distance between the air inlet duct and
the flue gas outlet duct must be of 250 mm and moreover
both terminals must be positioned within a 500 mm
square area.
C43
Boiler designed for connection to collective flue systems
including two ducts, one for the air inlet and the other for
the discharge of products of combustion through con-
centric or twin ducts.
C53
Boiler with separate air inlet and products outlet. These
ducts can discharge into areas with different pressure.
The two terminals must not be fitted on to two opposite
walls.
C83
Boiler designed for connection to a terminal for the in-
take of combustion air and to an individual or collective
chimney for the discharge of the products of combu-
stion.
The chimney must comply to the current regulations.
B23
Boiler designed to be connected to an open flue which
will terminate vertically through the roof. The combustion
air is withdrawn directly from the room where the boiler
is installed.
WARNING: for this type of connection the room must
comply with the same installation regulations valid
for open chimney boilers.
The chimney must comply to the current regulations.
aa
aa
aa
aa
aa
aa
aa
aa
aa
aa
aa
aa
aa
aa
aa
aa
aa
aa
aa
aa
Type C63
Boiler designed for connection to a combustion air inlet and
flue products discharge system approved and sold separa-
tely.
Содержание ALKON C 18
Страница 1: ...ALKON 09 R 18 C 18 R 24 C 24 00333176 2nd edition 10 2011 INSTALLATION AND SERVICING MANUAL ...
Страница 46: ......
Страница 47: ......