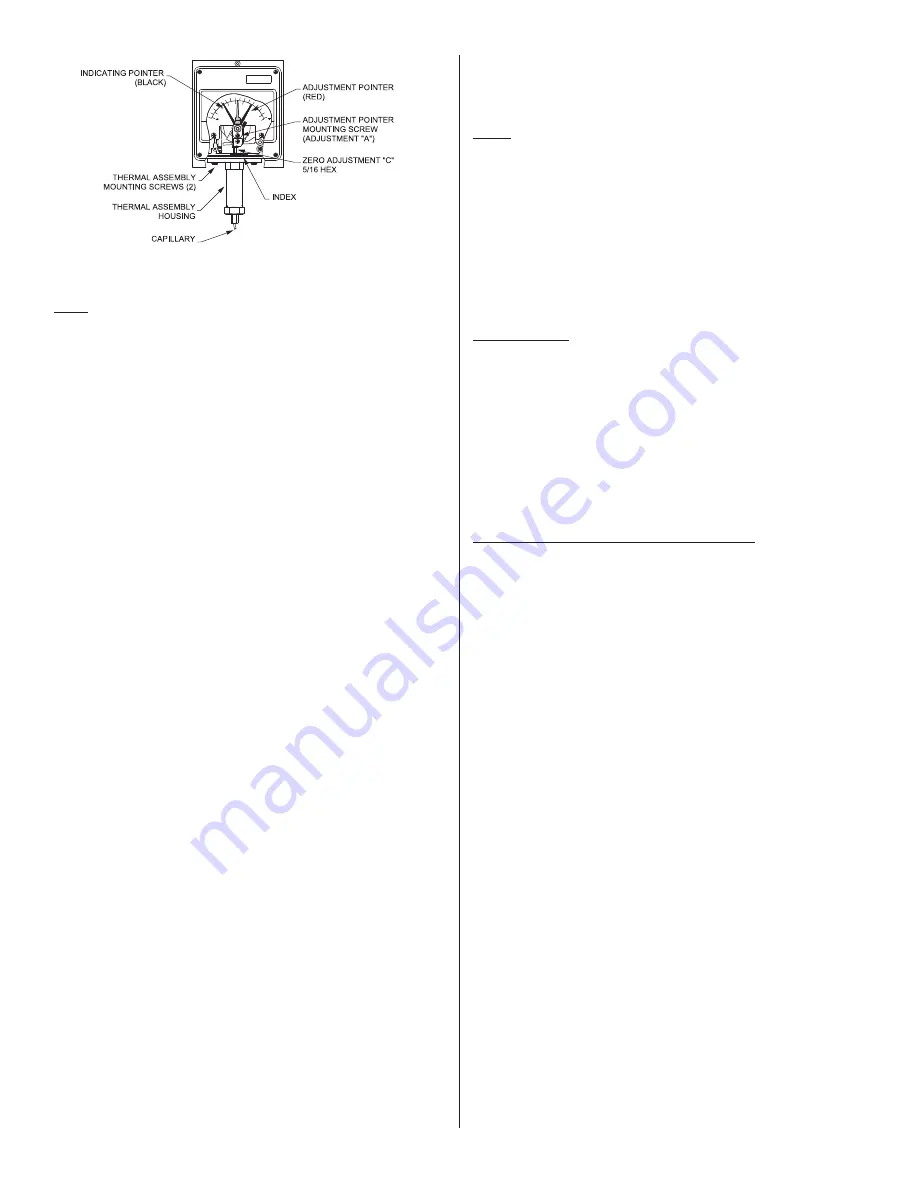
IMT120-12
www.ueonline.com
NOTE:
indicating pointer adjustment (820e, 822e): use an accurate test
thermometer such as a thermocouple with its probe mounted directly to the
center of the sensing bulb. before making any adjustments, allow process
temperature to stabilize; i.e., successive on-off cycles repeated.
correct any difference between the indicating pointer and the test
thermometer by holding the compensator with a 5/16” wrench while turning
the zero adjustment “c” on the thermal assembly with a second 5/16”
wrench (see figure 5) until the brown indicating pointer reads the same as
the test thermometer. turning clockwise lowers indicated reading. compare
the process temperature with the set point adjustment pointer. loosen
adjustment screw “a” to align set point adjustment pointer with the indicating
pointer. re-tighten screw “a”.
Correction of Capillary (820E, 822E)
if the length of capillary immersed in the process differs from the amount
immersed (6”, see Mounting bulb & capillary in part i - installation) at the
factory calibration bath, a calibration shift will occur. the error may be cor-
rected as follows:
Move set pointer to the highest temperature setting. note indicating scale
reading with the head and sensor at room temperature. loosen the two
thermal assembly mounting screws. re-position the housing index against the
calibration on the instrument case (or skeleton casting) at a rate of 1 divi-
sion line per capillary length listed in figure 6. Move to the left if capillary is
to be added to the process, or to the right if capillary is to be removed from
process.
*added to or taken away from the process
Model
number
range
cap length/
division*
1
-180 to 120
°
f
2 ft
2
-125 to 350
°
f
1 1 /2 ft
3
-125 to 500
°
f
1 ft
4
-40 to 120
°
f
4 ft
5
-40 to 180
°
f
3 ft
6
0 to 250
°
f
2 1/2 ft
7
0 to 400
°
f
2 ft
8
50 to 650
°
f
2 ft
Figure 6
zONE hAzARDOUS LOCATIONS FLAMEPROOF GAP AND jOINT
DETAILS
120’S
activation plunger to adjustment screw hole gap joints: 1.140in/28.96mm
min length by 0.0039in/0.099mm max annular gap
plunger guide to enclosure through threaded joints: minimum 8 ½ fully
engaged threads
cover to enclosure through threaded joints: minimum 7 ½ fully engaged
threads
121’S & 122’S
activation plunger to enclosure through hole gap joints: 1.000in/25.40mm
min length by 0.0030in/0.076mm max annular gap
adjustment shaft to shaft through hole gap joints: 1.050in/26.67mm min.
length by 0.0035in/0.089mm max. annular gap
cover to enclosure through threaded joints: minimum 7 ½ fully engaged
threads
MANUAL RESET OPTION 1530 (120’S,121’S)
reset pivot to pivot guide through hole gap joints: 1.118in/28.40mm min.
length by 0.0036in/0.091mm max annular gap
reset guide to enclosure through threaded joints: 8 fully engaged threads
Figure 5: Indicating Enclosure Internals