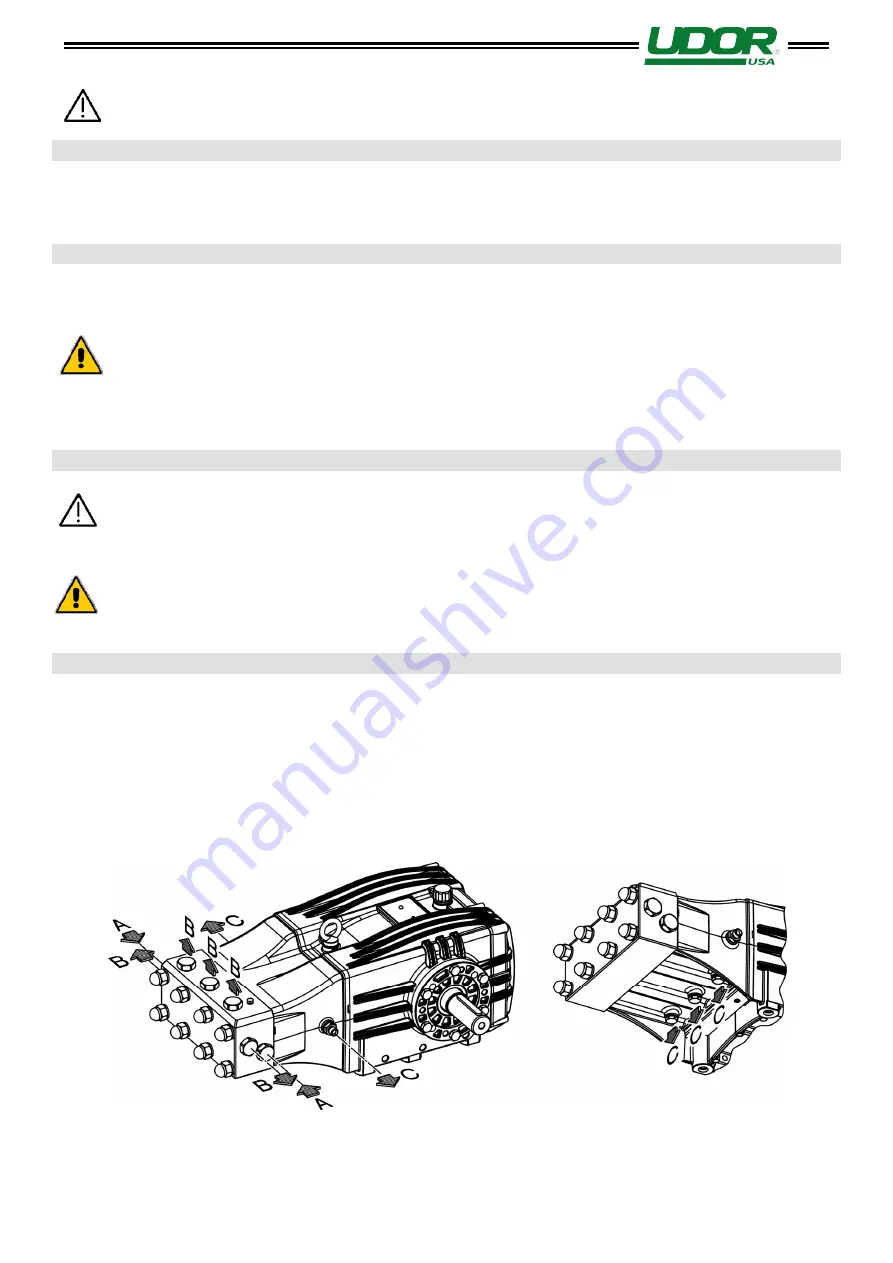
5
The Pump is supplied to be installed on a more complex machine or plant; the manufacturer of such
machine or plant shall add all the information related to safety of the assembled machine/plant
fulfilled.
3. INTENDED USE
UDOR Plunger Pumps are designed to be used in machines or systems for transferring pressuri
z
ed water, such as the
following for example: High Pressure Cleaning, High Pressure Descaling, Chemical Process.
The temperature of the workplace shall be between: Min. 0°C (32°F) - Max.40°C (104°F)
The Pump cannot be used submerged under any type of liquid.
4. OPERATIONAL RESTRICTION
The specifications of the liquid to be used are described in detail herewith: do not use for different liquids; in
particular, it is NOT possible to use UDOR Pumps in the following conditions:
- In the presence of water with high salt content, such as seawater for example; for this type of use, you are
recommended to use UDOR Pump stainless steel series.
- In workplaces where there is a corrosive or explosive atmosphere.
- In the presence of any liquid that is not compatible with the constructional material of the Pump.
- To pump paint, solvents, fuel and any flammable liquid (not suitable for ATEX workplaces).
- To foodstuffs.
- To wash people, animals, live electrical or electronic equipment.
- To wash the Pump itself.
5. GENERAL WARNINGS
- Never start the Pump under pressure.
- Constantly check the state of wear of the pipes and relevant fittings, especially those under pressure. Pipes
with signs of abrasion or that do not guarantee a perfect seal shall be replaced.
- The Pump must never run dry/without any liquid while in use.
- Protect rotating parts with a cover to prevent contact.
- The Pump is designed to be integrated in a machine or system, with various supply systems, which may
make the noise level vary, even quite substantially. The manufacturer of such machine or system shall assess
the level of noise emitted by the assembled machine or system and inform the user appropriately, also in
relation to the use of suitable personal protection equipment.
6. BEFORE START UP
6.1 LIQUIDS TO BE PUMPED
The Pump is designed and manufactured to transfer clean liquid or non-aggressive watery solutions.
The liquid intaken must be free from sand or other solid particles in suspension.
The liquid intaken shall have viscosity and density similar to water.
The maximum temperature of the liquid to be pumped: 35°C (95°F).
Any other use is not admitted unless
authorized
in writing by the Engineering Department of UDOR.
6.2 INLET, OUTLET AND PORTS OF THE PUMP
The UDOR pumps of the VY series (see fig. 2) are equipped with the following fittings:
Fig.
2
A.
No. 2 G 1/2" Inlets (also called In-take or Supply fittings); by removing or inverting the sealing caps, they can
be used indifferently on the right or left part of the head of the Pump or they can both be used.
Содержание VY Series
Страница 1: ...Pompa a Tre Pistoni Triplex Plunger Pump VYseries Assembly Instructions USE AND MAINTENANCE MANUAL ...
Страница 2: ......
Страница 12: ...12 14 PERFORMANCE CURVES ...
Страница 13: ...13 ...
Страница 14: ...14 ...
Страница 15: ...15 ...
Страница 16: ...16 ...
Страница 17: ...17 15 MAINTENANCE GUIDE A CHECK OR REPLACEMENT OF VALVES ...
Страница 18: ...18 B CHECK OR REPLACEMENT OF WATER PACKING SEALS 1 See Chapter A Images 1 to 6 ...
Страница 19: ...19 ...
Страница 20: ...20 ...
Страница 23: ......