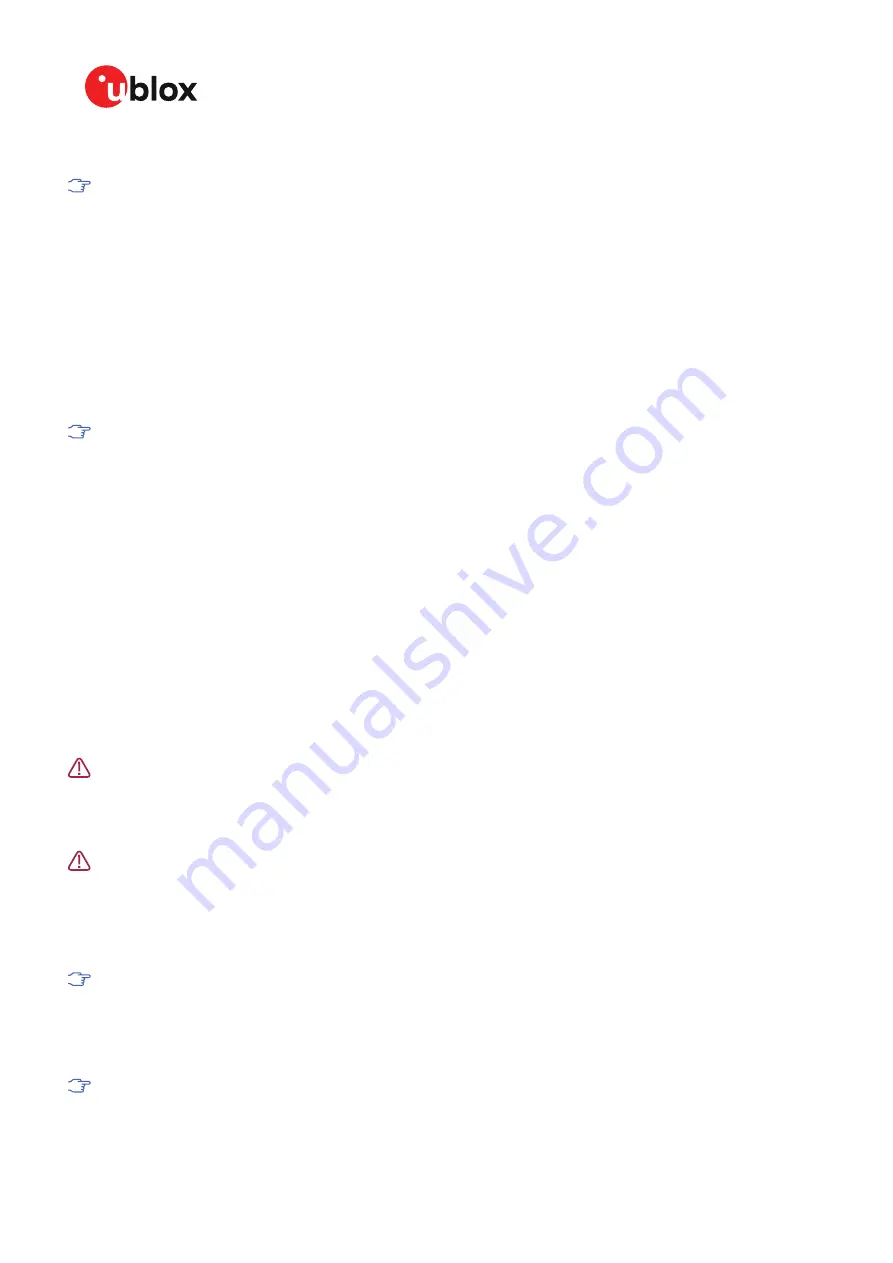
NEO-F10N - Integration manual
Cleaning
Do not clean with water, solvent, or ultrasonic cleaner:
• Cleaning with water will lead to capillary effects where water is absorbed into the gap between
the baseboard and the module. The combination of residues of soldering flux and encapsulated
water leads to short circuits or resistor-like interconnections between neighboring pads.
• Cleaning with alcohol or other organic solvents can result in soldering flux residues flowing
underneath the module, into areas that are not accessible for post-cleaning inspections. The
solvent will also damage the sticker and the printed text.
• Ultrasonic cleaning will permanently damage the module, in particular the quartz oscillators.
The best approach is to use a “no clean” soldering paste to eliminate the cleaning step after the
soldering.
Repeated reflow soldering
Repeated reflow soldering processes or soldering the module upside down are not
recommended.
A board that is populated with components on both sides may require more than one reflow
soldering cycle. In such a case, the process should ensure the module is only placed on the board
submitted for a single final upright reflow cycle. A module placed on the underside of the board may
detach during a reflow soldering cycle due to lack of adhesion.
The module can also tolerate an additional reflow cycle for rework purposes.
Wave soldering
Base boards with combined through-hole technology (THT) components and surface-mount
technology (SMT) devices require wave soldering to solder the THT components. Only a single wave
soldering process is encouraged for boards populated with modules.
Rework
We do not recommend using a hot air gun because it is an uncontrolled process and can damage
the module.
Use of a hot air gun can lead to overheating and severely damage the module. Always avoid
overheating the module.
After the module is removed, clean the pads before reapplying solder paste, placing and reflow
soldering a new module.
Never attempt a rework on the module itself, e.g. by replacing individual components. Such
actions will immediately void the warranty.
Conformal coating
Certain applications employ a conformal coating of the PCB using HumiSeal® or other related
coating products. These materials affect the RF properties of the GNSS module
Conformal coating of the module will void the warranty.
Casting
If casting is required, use viscose or another type of silicon pottant. The OEM is strongly advised to
qualify such processes in combination with the module before implementing this in the production.
Casting will void the warranty.
Grounding metal covers
UBXDOC-963802114-12193 - R02
5 Product handling
Page 32 of 42
C1-Public