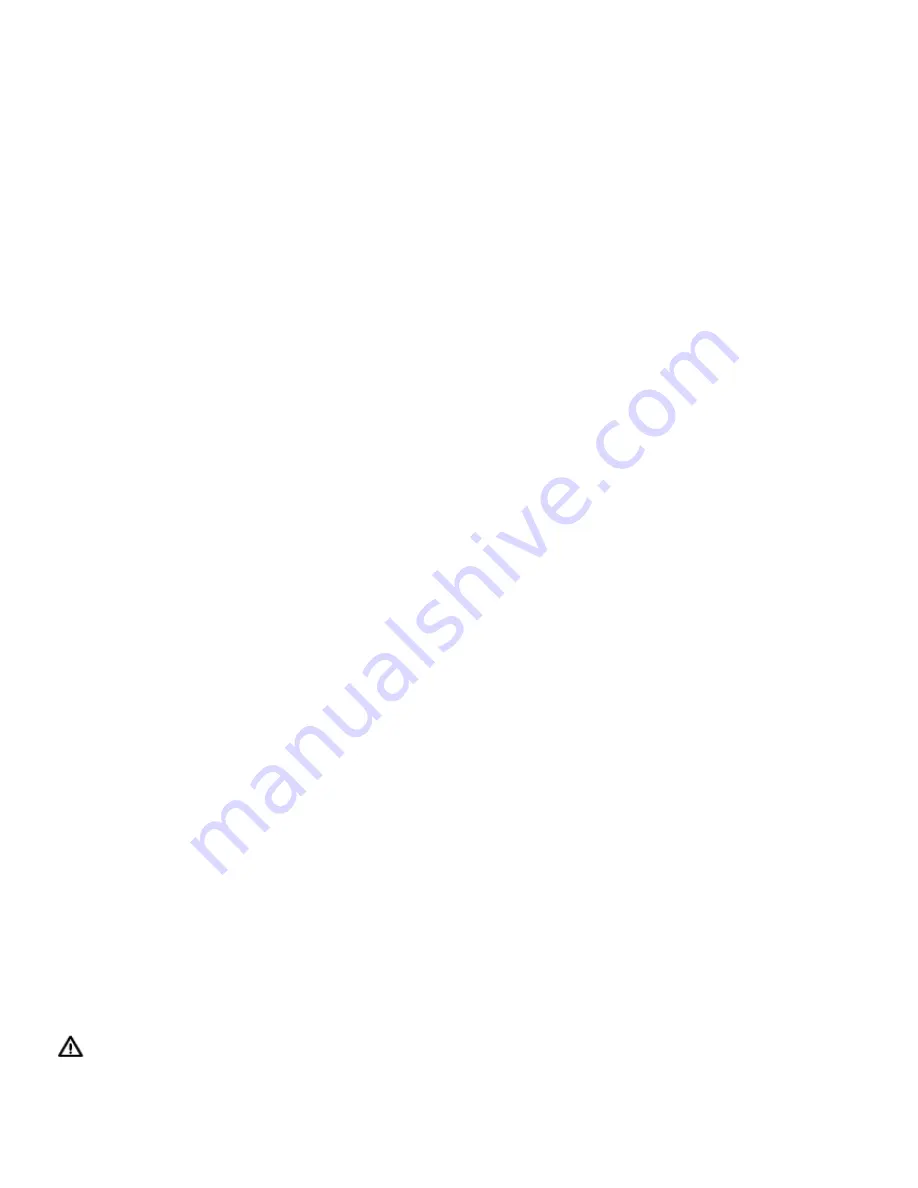
4
Connect the priming hose to the machine, turn the pump ON (2) and prime the air out of the pump.
When the water is clear (no air in it) turn the pump off and remove the priming hose. NOTE: if priming
is difficult, place the open end of the priming hose into the vacuum inlet hose barb, and turn the vacuum
on (6). Use you hand to block the open area in the hose barb. This will allow the pump and the
vacuum to work together to get the water moving. Priming may take 20-60 seconds, and the solution
tank should be full. Once the pump is primed, turn the pump and the vacuum off. Remove the
priming hose.
5
Add liquid cleaning chemical, with a pH between 6 and 9, to the solution tank.
6
Attach the spray hose to the solution quick disconnect and the vacuum hose to the hose barb on
the recovery tank. Pull the hoses out of the reel. Attach the other ends of the hoses to the
cleaning tool.
6
Allow the heat exchanger two minutes to reach operating temperature. The red light (5) will go out
when the heater has reached operating temperature. NOTE: the red light will be on nearly all the
time as you clean.
7
Turn the pump on and set the pressure selection switch (3) to the desired spraying pressure 300 or
50 PSI). Turn the vacuum on (6).
8
Begin cleaning using the correct hoses and tool.
9
Use defoamer in the recovery tank any time foaming occurs.
10 Monitor the water level in the solution tank. Do not let the pump run dry.
11 When the solution tank gets low, turn the pump and the vacuum off, fill the solution tank, empty
and clean the recovery tank.
12 When finished with the job, remove any unused solution from the solution tank, and run a few
gallons of clean water through the system. Drain the recovery tank by placing the dump hose over
a drain, or into a bucket, and remove the hose cap. Disconnect the hoses from the cleaning tool,
and reel the hoses up onto the hose spool.
NOTE: to remove the reel, with the hoses, from the machine, pull the vacuum hose loose from the hose
barb on the front of the tank. Disconnect the solution hose quick coupling. Push the vacuum hose into the
center of the spool. Grasp the spool on both sides, and lift it off the machine. NOTE: before servicing any
component in the base cabinet, the hoses and spool must be removed from the machine before the tanks
can be lifted open.
This unique, patented system is operated by a solid state circuit. It will inform the operator when the two
cords are plugged into separate circuits by turning on the circuit locator light. This helps to prevent tripping
circuit breakers. NOTE: if the green, circuit locator light does not illuminate when the cords are plugged in,
then both cords are on the same circuit. Try other outlets with one of the cords until you get the locator
light to come on. NOTE: if the bypass switch is turned on when both cords are on the same circuit, the
breaker in the wall may trip.
REFER TO THE DIAGRAMS ON THE PREVIOUS PAGE
BALL FLOAT SHUT-OFF
When the recovery tank is full, the ball float will disable the vacuum suction. This will prevent water from
entering the vacuum motor. The float may not work properly if the vacuum inlet float filter is dirty or if
there is heavy foam in the tank
.
CAUTION: to avoid vacuum motor damage, always make sure the float filter is clean and that the
ball can travel freely before you operate the machine. Always use a defoamer any time foam is
present.
ELECTRIC CIRCUIT LOCATOR