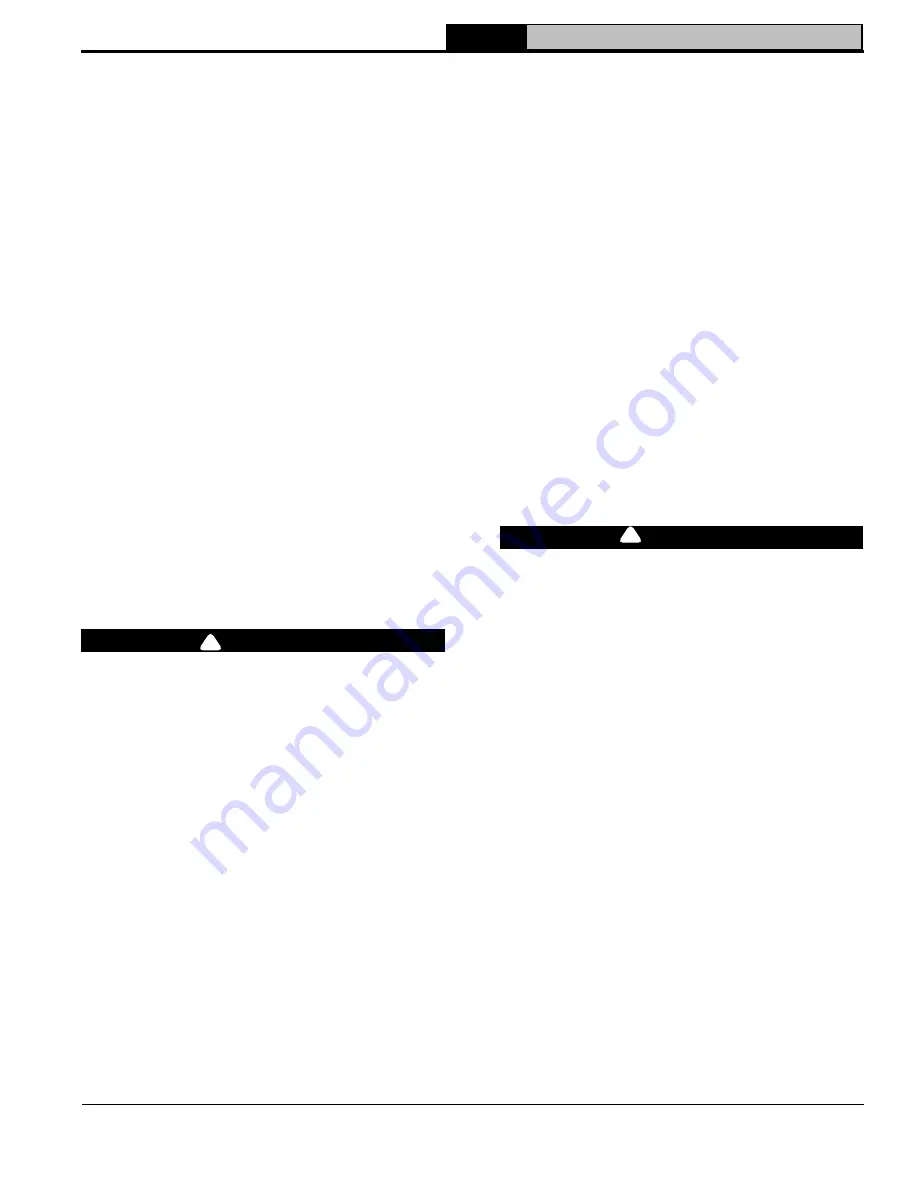
106636-04 - 8/22
33
X-2
Installation, Operating & Service Manual
13
Service and Maintenance
(continued)
4. Clean Main Burners and Combustion Chamber.
A. To remove burners for cleaning, changing
orifices, or repairs:
i. Remove Jacket Front Panel.
ii. Disconnect pilot tubing at gas valve.
iii. Disconnect 3-wire plug at the gas valve.
iv. Remove wires to flame roll-out switch.
v. Disconnect ignitor sensor cable at boiler
control.
vi. Remove burner access panel.
vii. Mark location of pilot main burner on the
manifold if marking on manifold is missing.
viii.Hold burner at throat. Lift front of burner
to clear orifice. Pilot burner can only be
removed by lifting the burner adjacent to its
right first.
B. Brush top of burners with a soft bristle brush.
Vacuum burners.
C. Check orifices. Drilled passageways must be
free of lint or dirt.
D. Vacuum tip of Pilot Burner.
E. Clean combustion chamber by vacuuming.
Exercise care not to damage base insulation.
F. Install burners by reversing procedure used
to remove burners. Make sure burner with
pilot assembly is in same location as original
installation.
WARNING
Be careful handling pilot tubing. Do not crimp
or crack pilot tube. Leaking pilot tubing could
result in serious injury, or substantial property
damage.
Check burners to see that they are located
properly in slot at rear of burner tray. Reinstall
burner access panel. Reconnect flame roll-out
switch wires, pilot gas supply, and pilot lead.
G. Connect pilot gas supply, igniter/sensor wire,
and ground wire at Boiler Control.
F. Install Burner Access Panel. Connect Flame
Rollout Switch wires.
5. Inspect Water Piping.
A. Check all system piping for leaks.
B. Repair any leaks before placing back into
service.
6. Inspect Temperature/Pressure Gauge.
A. Water temperature needle should move with
variation in water temperature.
B. Pressure needle should move with variation in
pressure.
C. Replace gauge if needed.
7. Operate Safety Relief Valve.
A. When manually operating relief valve,
water will discharge. Take precautions to
avoid contact with hot water and avoid water
damage. Inspect relief valve and lift lever to
verify flow.
B. If relief valve leaks or will not seat properly,
replace relief valve.
8. Inspect Gas Piping.
A. Sniff around boiler area for indication of gas
leak.
B. Locate leaks using approved gas detector,
a non corrosive leak detector fluid or other
approved leak detection methods.
C. Repair any leaks before placing back into
service and retest.
DANGER
Explosion Hazard.
Do not use matches, candles, open flames, or
other ignition sources to check for leaks. Failure
to comply could result in severe personal injury,
death, or substantial property damage.
9. Inspect Air Openings.
A. Keep boiler area clear of combustible
materials.
B. Remove any obstructions in boiler room
that will hinder flow of combustion and
ventilation air and dilution air.
10. Follow Section 10 instructions to put boiler back
into operation.
11. Check CO detector operation (if available).
12. Lubrication. There are no parts requiring
lubrication by service technician or owner.
Circulator bearings are water lubricated.
13. If remodeling has occurred, verify combustion air
supply is adequate.
!
!