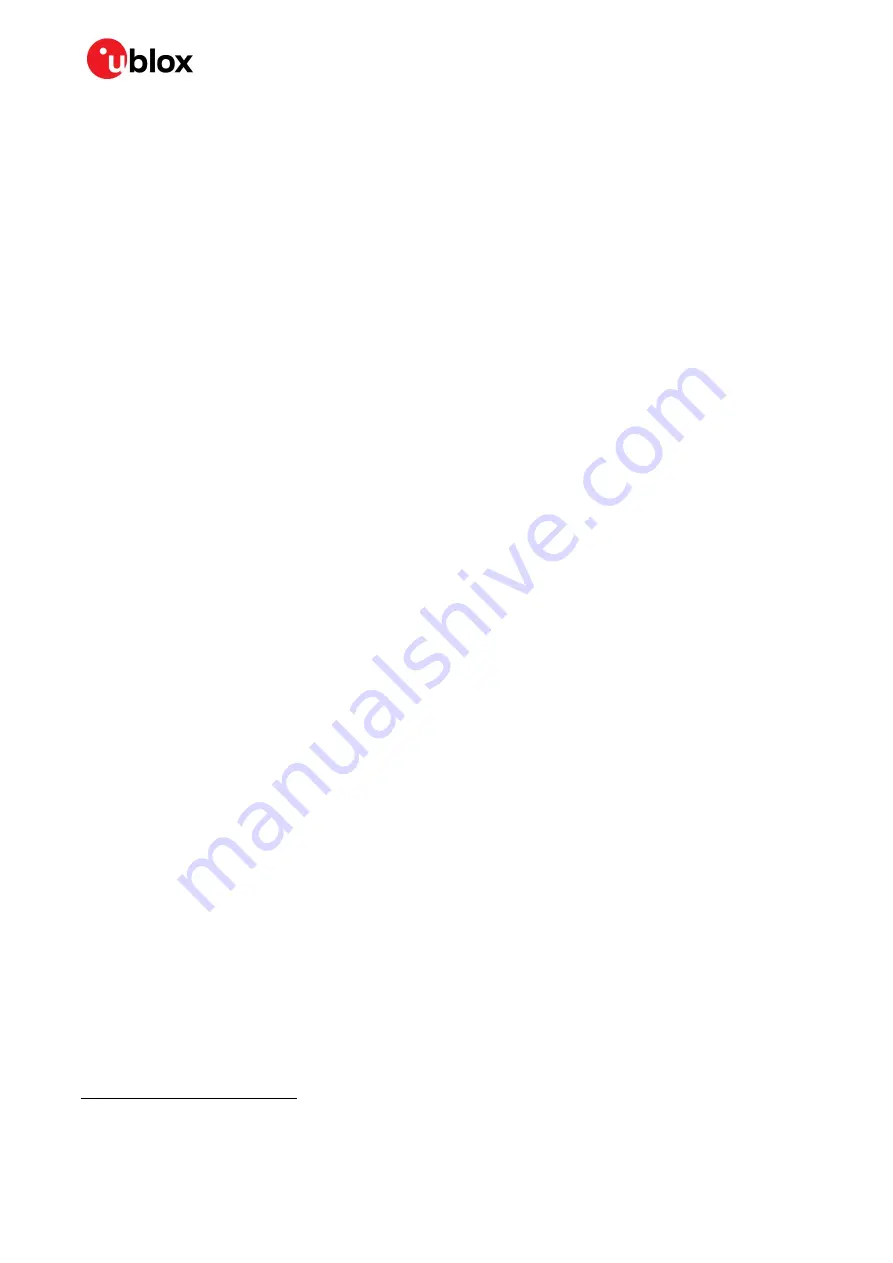
LILY-W1 series - System integration manual
UBX-15027600 - R09
Design-in
Page 23 of 64
C1 - Public
•
Additional bypass capacitors in the range of 100 nF to 1
µ
F on all supply pins are required for high
frequency filtering. The preferred choice is a ceramic capacitor with X7R or X5R dielectric due to
low ESR/ESL. Smaller size bypass capacitors should be chosen for the manufacturing process to
minimize ESL.
2.3.1.1
Guidelines for VCC supply circuit design using a switching regulator
It is recommended to use a Switching Mode Power Supply (SMPS) when the difference from the
available supply rail to the
VCC
rail allows significant power savings. For example, conversion of a 12
V or greater voltage supply to the nominal 3.3 V value for the
VCC
supply.
The characteristics of the SMPS connected to the
VCC
pin should meet the following prerequisites to
comply with the module requirements summarized in Table 4.
•
Power capability:
The switching regulator together with any additional filter in front of the module
must be capable of providing a voltage value within the specified operating range, and must be
capable of delivering the specified peak current.
•
Low output ripple
: The switching regulator must be capable of providing a peak-to-peak Voltage
ripple within the specified limits. This requirement applies both to voltage ripple generated by
SMPS operating frequency and to high frequency noise generated by power switching.
•
PWM/PFM mode operation
: It is preferable to select regulators with fixed Pulse Width Modulation
(PWM) mode. Pulse Frequency Modulation (PFM) mode typically exhibits higher ripple and may
affect RF performance. If power consumption is not a concern, PFM/PWM mode transitions
should be avoided in favor of fixed PWM operation to reduce the peak-to-peak noise on voltage
rails. Switching regulators with mixed PWM/PFM mode can be used provided that the PFM/PWM
modes and transition between modes complies with the requirements.
2.3.1.2
Guidelines for supply circuit design using a Low Drop-Out (LDO) linear
regulator
The use of a linear regulator is suggested when the difference from the available supply rail and the
VCC
or
VCC_IO
value is relatively low. The linear regulators provide acceptable efficiency when
transforming a supply of less than 5 V to a voltage value within the normal operating range of the
module. A linear regulator can be also considered to power the
VCC_IO
section due to the low current
requirements, especially if cascaded from a SMPS-generated low voltage rail.
The characteristics of the Low Drop-Out (LDO) linear regulator used to power the voltage rails must
meet the following prerequisites to comply with the requirements summarized in Table 4.
•
Power capabilities
: The LDO linear regulator with its output circuit must be capable of providing a
voltage value to the
VCC
or
VCC_IO
pins within the specified operating range and must be capable
of withstanding and delivering the maximum specified peak current while in connected-mode.
•
Power dissipation
: The power handling capability of the LDO linear regulator must be checked to
limit its junction temperature to the rated operating range. The worst-case junction temperature
can be estimated as shown below:
𝑇𝑇
𝑗𝑗
,
𝑒𝑒𝑒𝑒𝑒𝑒
= (
𝑚𝑚
𝑖𝑖𝑖𝑖
− 𝑚𝑚
𝑜𝑜𝑜𝑜𝑒𝑒
)
∗ 𝐼𝐼
𝑎𝑎𝑎𝑎𝑎𝑎
∗ 𝜃𝜃
𝑗𝑗𝑎𝑎
+
𝑇𝑇
𝑎𝑎
Where:
𝜃𝜃
𝑗𝑗𝑎𝑎
is the junction-to-ambient thermal resistance of the LDO’s package
𝐼𝐼
𝑎𝑎𝑎𝑎𝑎𝑎
is the current
consumption of the given voltage rail in continuous TX/RX mode and
𝑇𝑇
𝑎𝑎
is the maximum operating
temperature of the end product inside the housing.
5
Thermal dissipation capability reported on datasheets is usually tested on a reference board with adequate copper area (ref.
to JESD51 [13]). Junction temperature on a typical PCB may be higher than the estimated value due to the limited space to
dissipate the heat. Thermal reliefs on pads also affect the capability of a device to dissipate the heat.