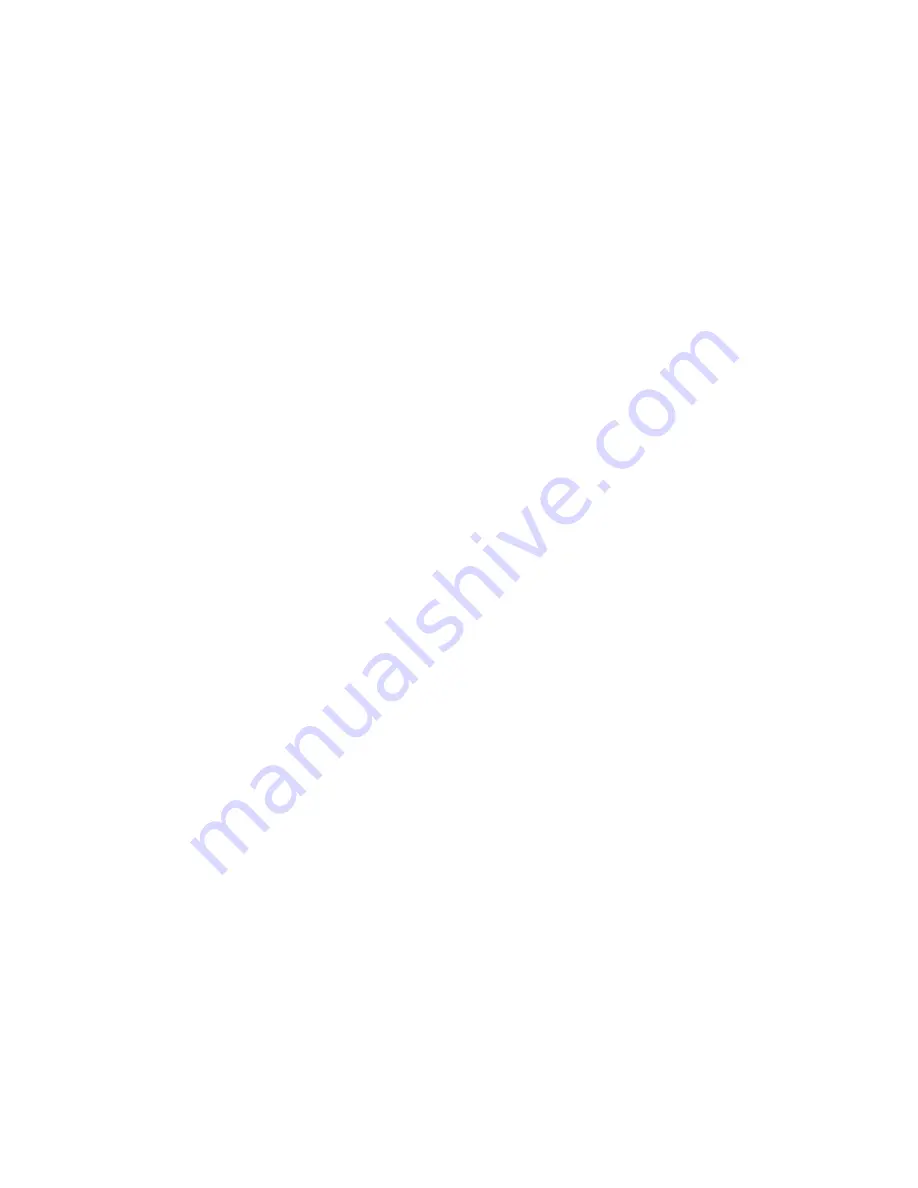
TFP1020
Page 17 of 20
The absence of air discharging from
the Automatic Drain Valve is an indica-
tion of a properly set air seat within the
DPV-1 Valve. If air is discharging, refer
to the Care and Maintenance section
under Automatic Drain Valve Inspection
to determine/correct the cause of the
leakage problem.
Step 10.
Partially open the Main
Control Valve. Slowly close the Main
Drain Valve as soon as water dis-
charges from the drain connection.
Depress the plunger on the Automatic
Drain Valve to make sure that it is open
and that there is no water discharging.
The absence of water discharging from
the Automatic Drain Valve is an indica-
tion of a properly set water seat within
the DPV-1 Valve. If water is discharg-
ing, refer to the Care and Maintenance
section under the Automatic Drain
Valve Inspection to determine/correct
the cause of the leakage problem.
If there are no leaks, the DPV-1 Valve is
ready to be placed in service and the
Main Control Valve must then be fully
opened.
Note:
After setting a fire protection
system, notify the proper authorities
and advise those responsible for moni-
toring proprietary and/or central station
alarms.
Step 11.
Once a week after a valve is
reset following an operational test or
system operation, the Low Body Drain
Valve (and any low point drain valves)
should be partially opened (and then
subsequently closed) to relieve drain-
back water. Continue this procedure
until drain-back water is no longer
present.
Care and
Maintenance
The following procedures and inspec-
tions should be performed as indicated,
in addition to any specific requirements
of the NFPA, and any impairment must
be immediately corrected.
Before closing a fire protection system
main control valve for maintenance
work on the fire protection system that
it controls, permission to shut down the
affected fire protection system must be
obtained from the proper authorities
and notify all personnel who may be
affected by action.
The owner is responsible for the
inspection, testing, and maintenance of
their fire protection system and devices
in compliance with this document, as
well as with the applicable standards
of the National Fire Protection Associa-
tion (e.g., NFPA 25), in addition to the
standards of any authority having juris-
diction. Contact the installing contrac-
tor or sprinkler manufacturer regarding
any questions.
Automatic sprinkler systems are rec-
ommended to be inspected, tested,
and maintained by a qualified Inspec-
tion Service in accordance with local
requirements and/or national codes.
The operational test procedure and
waterflow pressure alarm test pro-
cedure will result in operation of the
associated alarms. Consequently,
notification must first be given to the
owner and the fire department, central
station, or other signal station to which
the alarms are connected.
Annual Operation Test Procedure
Note:
Unless otherwise noted, refer to
Figure 4, 5, or 6 to identify functional
trim components.
Proper operation of the DPV-1 Valve
(i.e., opening of the DPV-1 Valve during
a fire condition) should be verified at
least once a year as follows:
Step 1.
If water must be prevented
from flowing beyond the riser, perform
the following steps.
• Close the Main Control Valve.
• Open the Main Drain Valve.
• Open the Main Control Valve one
turn beyond the position at which
water just begins to flow from the
Main Drain Valve.
• Close the Main Drain Valve.
Step 2.
Open the system’s Inspector’s
Test Connection.
Step 3.
Verify that the DPV-1 Valve
has operated, as indicated by the flow
of water into the system and that all
waterflow alarms operate properly.
Step 4.
Close the system’s Main
Control Valve.
Step 5.
Reset the DPV-1 Valve in
accordance with the Valve Setting
Procedure.
Note:
It is recommended that the
requirement of NFPA 25 to annually
inspect the inside of the valve be per-
formed at this time and prior to reset-
ting the DPV-1 Valve. Refer to the
Automatic Drain Valve Inspection sub-
section Steps 2 through 5 for instruc-
tions with regard to the inspection of
the Clapper Facing.
Quarterly Waterflow
Alarm Test Procedure
Testing of the system waterflow alarms
should be performed quarterly. To test
the waterflow alarm, open the Alarm
Test Valve, which will allow a flow of
water to the Waterflow Pressure Alarm
Switch and/or Water Motor Alarm.
Upon satisfactory completion of the
test, close the Alarm Test Valve.
Water Pressure Inspection
The Water Pressure Gauge is to be
inspected monthly (per NFPA 25) to
ensure that normal system water pres-
sure is being maintained.
Air Pressure Inspection
The Air Pressure Gauge is to be
inspected monthly (per NFPA 25) to
ensure that normal system air pressure
is being maintained.
Automatic Drain Valve Inspection
The Automatic Drain Valve should be
inspected monthly (per NFPA 25) by
depressing the plunger and check-
ing to ensure that the Automatic Drain
Valve is not discharging water and/or
air. A discharge of water and/or air is
an indication that the air and/or water
seats are leaking, which could subse-
quently cause a false operation should
the intermediate chamber become
inadvertently pressurized.
If leakage is present, take the DPV-1
Valve out of service (i.e., close the
main control valve, open the main drain
valve, close the air supply control valve,
remove the Dry Pipe Valve Accelerator
from service, as applicable, in accor-
dance with its Technical Data Sheet
(Refer to TFP1105 for the VIZOR or
TFP1112 for the ACC-1), and open the
Inspector’s Test Connection to relieve
the system air pressure to 0 psig as
indicated on the System Air Pressure
Gauge), and then after removing the
Handhole Cover, perform the follow-
ing steps:
Step 1.
Make sure that the Seat Ring
is clean and free of any nicks or signifi-
cant scratches.
Step 2.
Remove the Clapper Assem-
bly from the valve by first pulling out
the Hinge Pin.
Step 3.
Disassemble the Clapper
Facing Retainer from the Clapper
so that the Clapper Facing can be
removed and inspected. Make sure
that the Clapper Facing does not show
signs of compression set, damage, etc.
Replace the Clapper Facing if there is
any signs of wear.
Step 4.
Clean the Clapper Facing,
Clapper, and Clapper Facing Retainer,
and then reassemble the Clapper
Assembly.
Step 5.
Reinstall the Clapper Assembly
with its Hinge Pin and then reinstall the
Handhole Cover.