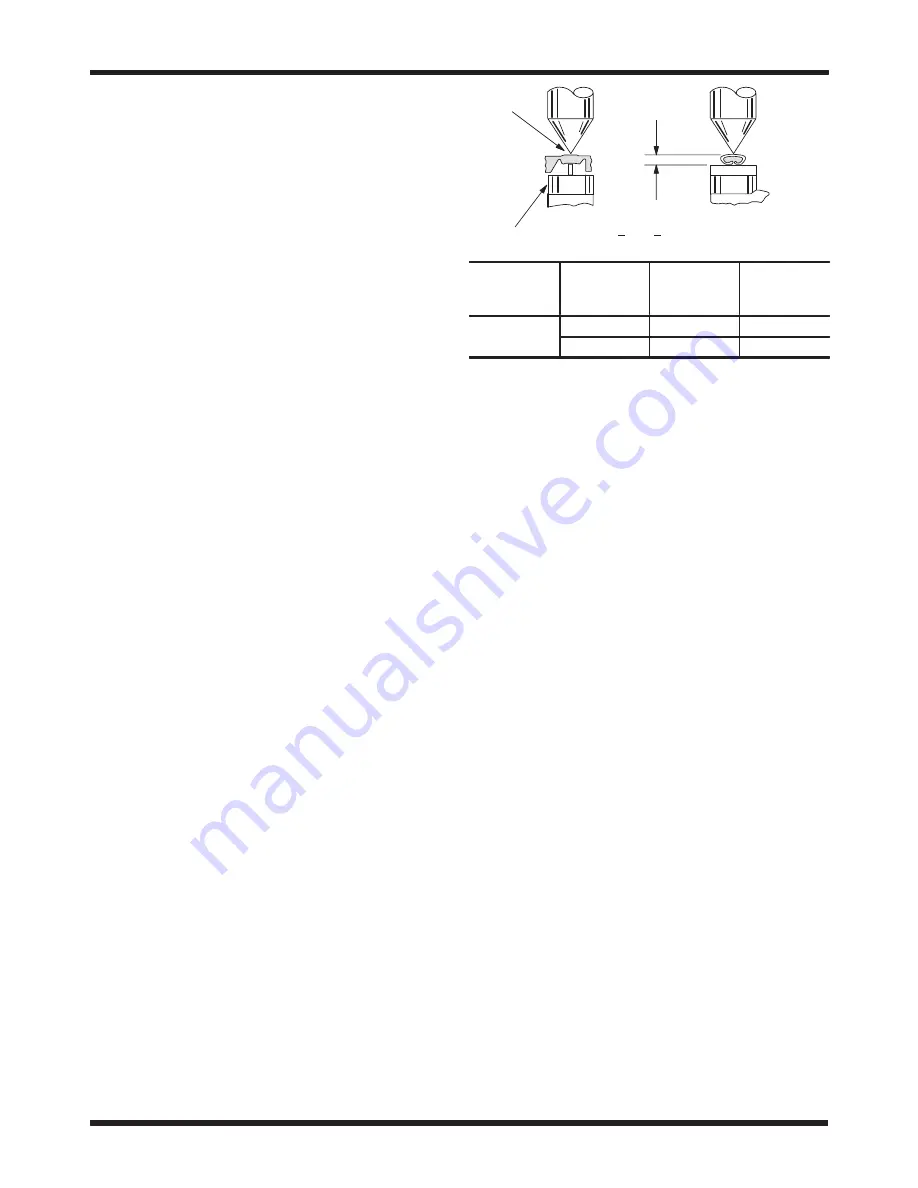
408-9375
Hand Crimping Tool 90430-1
3 of 4
Rev D
Tyco Electronics Corporation
4. When the tool is not in use, keep handles closed
to prevent objects from becoming lodged in the
crimping dies. Store the tool in a clean, dry area.
4.2. Lubrication
Lubricate all pins, pivot points, and bearing surfaces
with SAE No. 20 motor oil as follows:
Tools used in daily production – lubricate daily
Tools used daily (occasional) – lubricate weekly
Tools used weekly – lubricate monthly
Wipe excess oil from tool, particularly from crimping
area. Oil transferred from the crimping area onto
certain terminations may affect the electrical
characteristics of an application.
4.3. Periodic Inspection
1. Hand tool should be immersed (handles partially
closed) in a reliable commercial degreasing
compound to remove accumulated dirt, grease,
and foreign matter.
2. Close tool handles until ratchet releases and
then allow them to open freely. If they do not open
quickly and fully, the spring is defective and must
be replaced. See Section 5, REPLACEMENT AND
REPAIR.
3. Inspect head assembly for worn, cracked, or
broken dies. If damage is evident, return the tool
for evaluation and repair. See Section 5,
REPLACEMENT AND REPAIR.
4.4. Crimp Height Inspection
This inspection requires the use of micrometer with a
modified anvil as shown in Figure 5. Tyco Electronics
recommends use of the modified micrometer (Crimp
Height Comparator RS–1019–5LP) which can be
purchased from:
Shearer Industrial Supply Co.
717–767–7575
or
VALCO
610–691–3205
Proceed as follows:
1. Refer to the chart in Figure 5 and select a
contact and a wire (maximum size) for each crimp
section listed in the chart.
2. Refer to Section 3, CRIMPING PROCEDURE,
and crimp the contact(s) accordingly.
3. Using a crimp height comparator, measure wire
barrel crimp height as shown in Figure 5. If the
crimp height conforms to that shown in the chart,
the tool is considered dimensionally correct. If not,
return the tool for evaluation and repair (refer to
Section 5, REPLACEMENT AND REPAIR).
A"
+0.05 [+.002]
CONTACT
WIRE SIZE
AWG (MAX)
CRIMP SECT
WIRE SIZE
MARKING
DIM. A"
High Density
26
26-28
0.69 [.027]
g
y
22 DF
22
22-24
0.79 [.031]
Figure 5
For additional information concerning the use of the
crimp height comparator, refer to Instruction Sheet
408–7424.
4.5. CERTI-CRIMP Ratchet Inspection
The CERTI–CRIMP ratchet feature on hand tools
should be checked to ensure that the ratchet does not
release prematurely, allowing the crimping dies to
open before they have fully bottomed. Obtain a
0.025–mm [.001–in.] shim that is suitable for checking
the clearance between the bottoming surfaces of the
crimping dies. Proceed as follows:
1. Select the maximum size wire and strip it
according to dimensions listed in Figure 2.
2. Select contact and crimp section corresponding
to the selected wire size (refer to Figure 2).
3. Position the contact and wire between the
crimping dies, as described in Section 3,
CRIMPING PROCEDURE.
4. Hold the wire in place and squeeze the handles
until the CERTI–CRIMP ratchet releases. Hold the
handles in this position, maintaining just enough
tension to keep the dies closed.
5. Check the clearance between the bottoming
surfaces of the crimping dies. If the clearance is
0.025 mm [.001 in.] or less, the ratchet is
satisfactory. If clearance exceeds 0.025 mm
[.001 in.], the ratchet is out of adjustment and must
be repaired. See Section 5, REPLACEMENT AND
REPAIR.
4.6. Insulation Crimp Adjustment
The insulation barrel crimp height is controlled by the
insulation adjustment lever. To determine the proper
setting, test crimp a contact using the setting which
approximates the insulation size (1–small, 2–medium,
3–large). If the crimped insulation barrel is too tight or
too loose, change the setting accordingly. The crimp
should hold the insulation firmly without cutting into it.