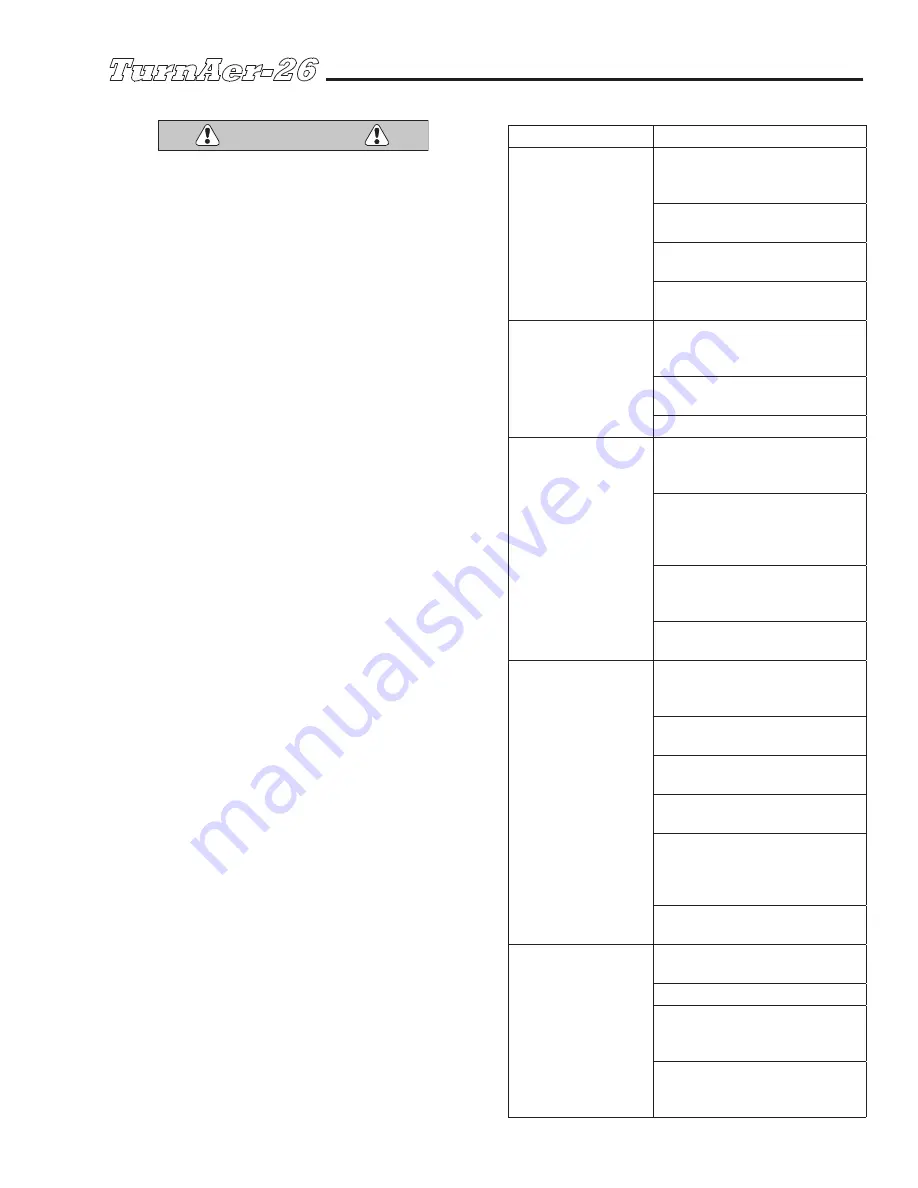
™
13
Operator Daily Inspection
WARNING
TO AVOID SERIOUS INJURY,
Never Perform Any Inspection With the TurnAer-26
Engine Running.
Wear the appropriate safety gear when Inspecting
the TurnAer-26.
Before each use, check the following items. Refer any
repairs to service personnel.
● Inspect fuel levels. Do not fill fuel tank over 3/4 full.
● Check for proper lubrication of the entire machine.
● Check for proper oil levels in the engine.
● Check condition and sharpness of the tines. Check
for plugged or blocked tines.
● Inspect all controls for proper operation
● Inspect the entire machine for loose fasteners.
Tighten if necessary.
● Inspect for damaged, inoperable, or missing guards
and components. Do not operate any machine
with missing, inoperable, or damaged guards and
components.
● Check for a buildup of dirt, grass, cores or debris
on the machine. Check under the top guard. Clean
machine before use. Do not high pressure wash.
Storage
TO STORE
the TurnAer-26 over a extended period,
clean all surfaces and remove any remaining aeration
cores from the machine. Use only
Low Pressure Wash
on the machine. High pressure washing can wash away
the grease from the bearings.
Remove fuel from gas tank and run engine until
carburetor is empty. Prepare engine in accordance with
engine manufacturer’s directions.
To avoid getting a flat spot on the front drums, store with
the front elevated.
Check the tines and remove any cores, stones, or
debris. Apply a light film of light machine oil to the tines
to control rust. See the lubrication directions and follow
the procedures.
If needed, fold the handlebar into the storage position.
Loosen the handlebar locking nuts and rotate the
handlebar forward until locks into a forward position. The
handlebar should not rest on the front bumper. Retighten
locking nuts. Take care not to trap or stress any control
cables.
TO RETURN TO SERVICE AFTER EXTENDED
STORAGE
, inspect the entire machine for any damage
that may have occurred during storage. Look for loose
or missing parts. Refer any needed correction to the
proper service level maintenance personnel. Check all
lubrication levels.
Troubleshooting Table
OPERATION
PROBLEM
POSSIBLE CAUSE
Excessive Vibration
or Noise
Worn Drive Train or Clutch
Idler Bearings. Worn Or
Misadjusted Drive Chains.
Loose Components. Tighten
All Fasteners
Dull, Bent, Broken, Plugged or
Loose Tines.
Engine Speed Wrong For Soil
Conditions.
Poor Tine
Penetration
Blocked Tine Openings.
Buildup of Dirt, Rocks or
Debris In Tines.
Ground Too Hard. Water Turf
To Soften Ground.
Worn, Dull or Damaged Tines.
Transport Wheels
Dragging Or
Catching On Turf
Misadjusted, Disconnected,
Worn or Damaged Wheel Lift
Tension Springs.
Wheel Lift Linkage Not
Latching In Raised Position.
Debris Caught in Mechanism
or Mechanism Damaged.
Transport Wheel Handle
Staying Raised (Actuated).
Wheel Lift Cables Caught.
Operating On Too Steep Of A
Slope.
Clutch Control
Inoperative
Slipping V–Belt At Clutch.
Mis–adjusted Clutch Control
Cable.
Broken or Worn V–Belt. V-Belt
Surface Contaminated.
Disconnected Clutch Control
Cable.
Clutch Control Cable Caught
On Handlebar Components.
Spring On Clutch Control
Cable Damaged, Stretched,
Or Caught On Components
Under or Near Top Guard.
Worn or Damaged Clutch Idler
Pulley.
Steering Brakes
Inoperative
Worn or Misadjusted Brake
Pads. Brake Housings Loose
Misadjusted Brake Cables
Debris Caught In Brake
Housing or debris Coating
Brake Rotors
Worn Bearings on Drive
Shaft Causing Rotors to Be
Misaligned