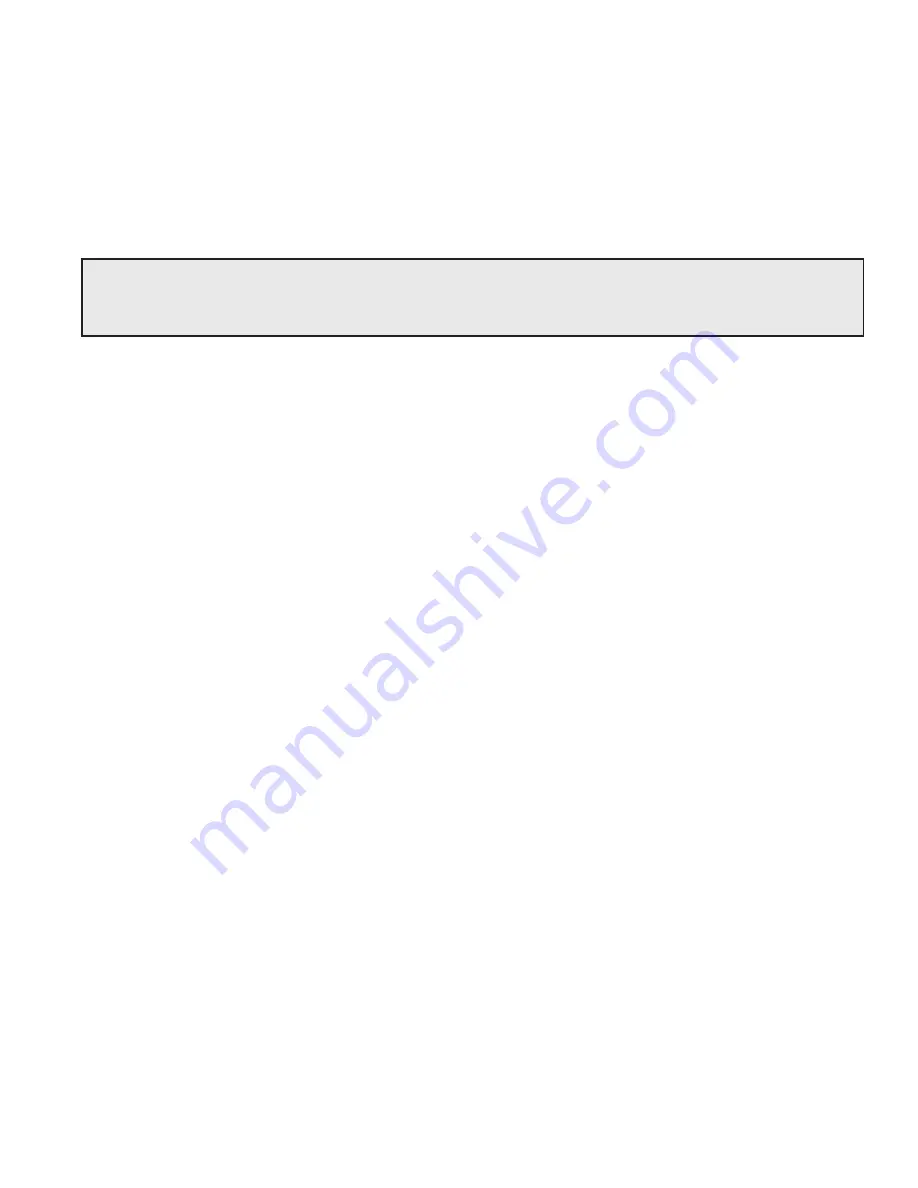
B1403 13
www.turck.com • Phone: 763-553-7300 • Application Support: 1-800-544-7769 • Fax: 763-553-0708 • Turck Minneapolis, MN 55441
www.turck.com • Phone: 763-553-7300 • Application Support: 1-800-544-7769 • Fax: 763-553-0708 • Turck Minneapolis, MN 55441
3 .7 Troubleshooting for Q21-DQ
Troubleshooting describes common problems that may occur when installing the LDT and offers possible solutions to these
problems . If, after reading this appendix, you are unable to resolve a problem, contact our technical support department at
1-800-544-7769 .
General Checks
Make sure that the magnet is located within the LDT’s active stroke area . Captive magnet assemblies should be positioned so
that they can move freely over the entire area of the active stroke without binding or pushing on the extrusion . Non-captive
magnet assemblies should be situated so that the magnet is no further than 3/8” from the sensing surface at any point in the
floating magnet assembly’s movement .
NOTE:
Ferromagnetic material (material readily magnetized) should be located no closer than 0 .25” from the sensing surface of the
LDT . This includes mounting brackets, magnet spacers, magnet brackets, and mounting screws . Ferromagnetic material can
distort the magnetic field, causing adverse operation or failure of the LDT .
Check all LDT wires for continuity and/or shorts . It is preferable that the cable between the LDT and the interface device be
one continuous run . If you are using a junction box, it is highly recommended that the splice junction box be free of AC and/
or DC transient-producing lines . The shield should be carried through the splice and terminated at the interface device end .
Power Supply Check
This section will help you to determine if your power supply is adequate for the LDT to operate properly, or if the LDT’s cable
has a short or open . In order for the Q21-DQ LDT to operate properly, the external power supply must provide a level between
13 .5 to 30 VDC . A power supply providing voltage above this specified range may damage the LDT . A power supply providing
power below this specified range will not be sufficient to power the LDT . When powering more than one LDT on a single
power supply, remember that each LDT requires three (2 .5) watts of power maximum (2 watts typical) . The amount of current
draw will vary based on the input voltage used . To calculate the current draw for a particular LDT, divide the LDT wattage by
the input voltage . For example, 2 watts divided by 24 VDC equals 104 mA .
If your LDT is not operating properly, the LDT’s cable may have an open or short, or the power supply is not supplying
sufficient power . To verify this, perform the following steps:
1 . Turn the power supply off .
2 . Remove the mating connector from the LDT .
3 . Turn the power supply on .
4 . Using a digital voltmeter, check from power supply common (GND) and Power (Vsource) from the mating end of
the cable for a level b13 .5 and +30 VDC .
If reading is between 13 .5 and 30 VDC, turn power supply off and go to step 7 . If reading is below 13 .5 VDC, either your
power supply is not providing enough power or the LDT’s cable possibly has a short/open . Readings of no voltage or minimal
voltage (less than 5 volts) may be due to short/open in the cable . If reading is not between 13 .5 and 30 VDC, go to step 5 . If
reading is above 30 VDC, adjust power supply or replace .
5 . Turn the power supply off .
6 . Check the continuity of the individual wires of the cable between the power supply and the LDT . Check for continuity from
one end of the cable to the other . Also verify that no shorts exist between pins .
7 . Reconnect the mating connector to the LDT .
8 . Turn power supply on .
9 . Using a digital voltmeter, check the power supply’s “+” and “-” terminals for a voltage between 13 .5 and 30 VDC .
Low voltage readings may indicate a power supply with a wattage (current) rating that is too low . (Each LDT requires 2 .5
watts) . If the cabling checks out in step 6 and your voltage is below 13 .5 VDC, check your power supply current rating . If
voltage is between 13 .5 to 30 VDC and the LDT is still inoperative, contact factory .
Содержание EZ-track
Страница 1: ...EZ track Q21 Series Quadrature Output Manual Your Global Automation Partner...
Страница 17: ...Notes...
Страница 18: ...Notes...
Страница 19: ...Notes...