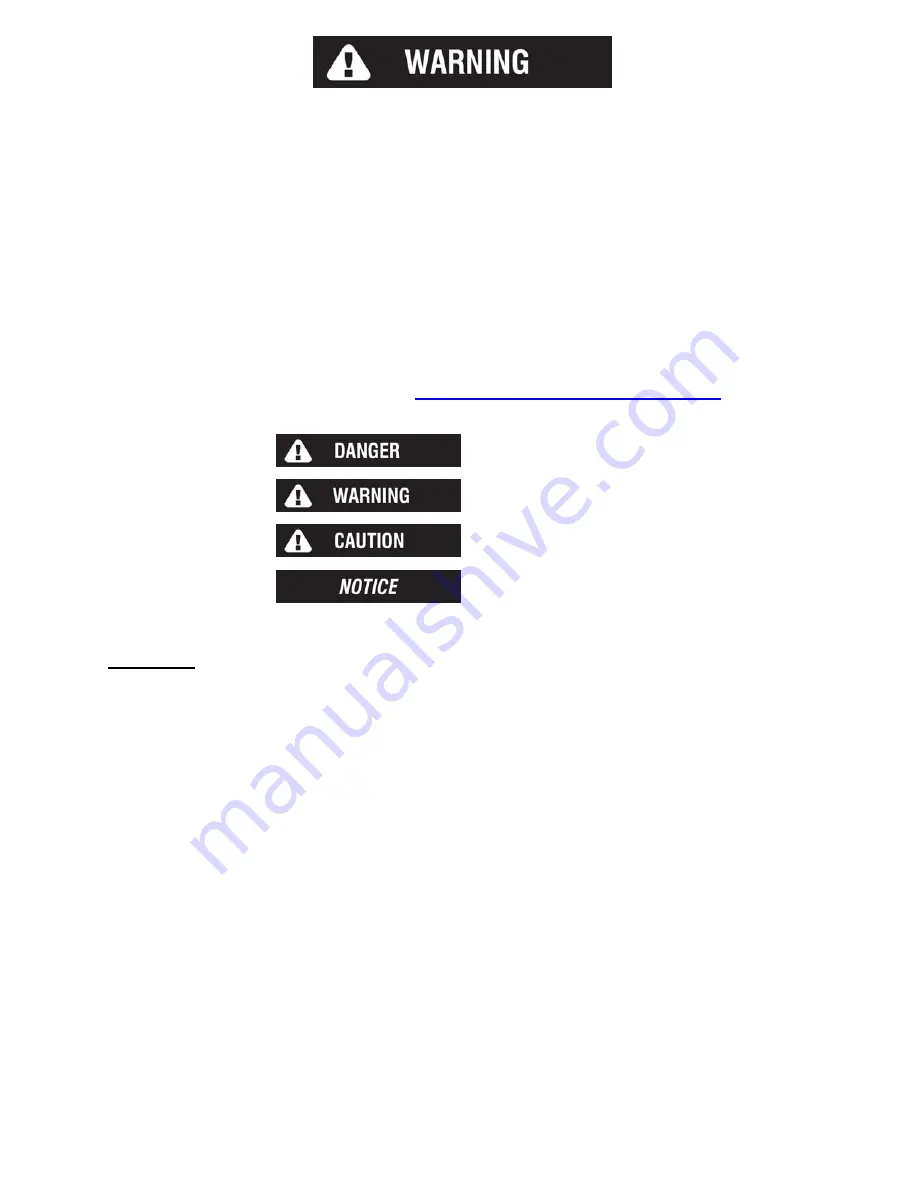
2
FAILURE TO HEED THE FOLLOWING WARNINGS
MAY RESULT IN SERIOUS INJURY OR DEATH.
The safety of the winch operator and ground personnel should always be of great
concern, and all necessary precautions to insure their safety must be taken. The
primary mover and the winch must be operated with care and concern for the
equipment and the environment and with a thorough knowledge of the equipment and
its performance capabilities must be understood. These general safety guidelines are
offered, however local rules and regulations or national standards may also apply.
Recommended references are, but not limited to, ANSI B30, OSHA 1910, AWS D 14.3,
and SAE J706.
Additional information can be found at
http://www.team-twg.com/TulsaWinch/
Mounting:
Winch mounting must be secure and able to withstand the applied loads.
•
The stability of the mounting system must be approved by a qualified person.
•
All welding should also be done by a qualified person.
•
Winch mount must be flat so as not to induce binding.
•
The flatness must not exceed 1/16 inch across the mounting surface of the winch
itself.
Guards must be placed on all open drives in the case of mechanical winches.
Insure that all hydraulic hoses, valves and fittings are rated to winch manufacturer’s
operating pressures.
Relief valves should be set to winch manufacturer’s specifications.
Insure that all PTO’s and drivelines are sized appropriately for the winch manufactures
speed and torque specifications.
Indicates an imminently hazardous situation
which, if not avoided, will result in death or serious
injury.
Indicates a potentially hazardous situation which,
if not avoided, could result in death or serious
injury.
Indicates a potentially hazardous situation which,
if not avoided, may result in minor or moderate
injury or property damage.
Indicates information or a company policy that
relates directly or indirectly to the safety of
personnel or protection of property.
Содержание RUFNEK 45
Страница 25: ...25 CLUTCH INSPECTION...
Страница 31: ...31 ISOMETRIC VIEW FOR ADJUSTABLE OIL BRAKE AND HYDRAULIC MOTOR SEE PAGE 32...