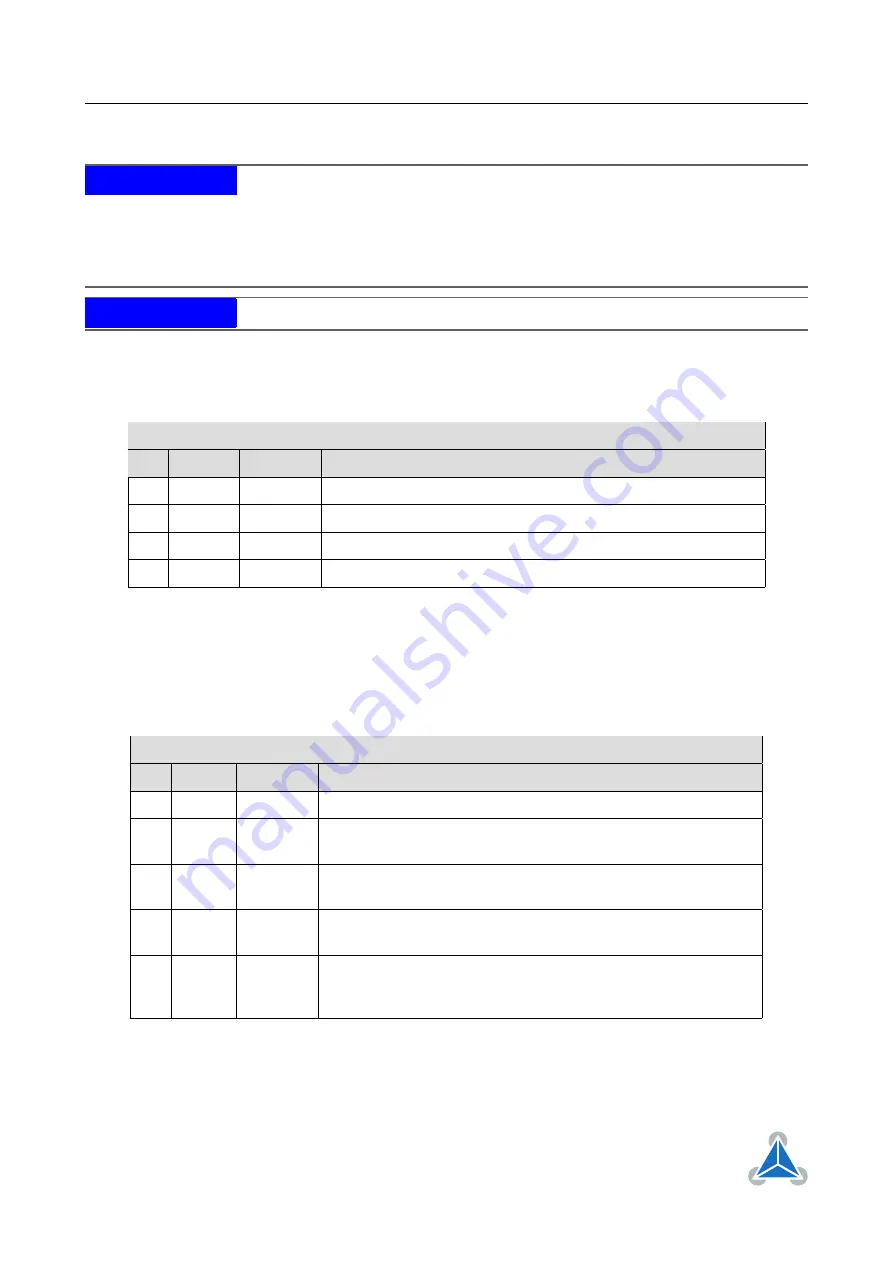
TMCM-6214 Hardware Manual • Hardware Version V1.30 | Document Revision V1.10 • 2019-MAR-25
11 / 27
NOTICE
Do not connect or disconnect motor during operation!
Motor cable and mo-
tor inductivity might lead to voltage spikes when the motor is (dis)connected
while energized. These voltage spikes might exceed voltage limits of the driver
MOSFETs and might permanently damage them. Therefore, always switch off
/ disconnect power supply or at least disable driver stage before connecting /
disconnecting motor.
NOTICE
Do not mix-up stop switch and motor connectors!
4.7 Stop switch connector
The TMCM-6214 offers 6 stop switch connectors (4pin JST PH series) - one for each motor axis.
Motor connector pin assignment
Pin
Label
Direction Description
1
GND
Signal and supply GND
2
+24V
out
connected to +24V supply input for supply of end switches etc.
3
STOP_L
in
Stop left switch input. Interal pull-up to +5V
4
STOP_R
in
Stop right switch input. Internal pull-up to +5V
Table 10: Stop switch connector pin assignment
4.8 Encoder connector
The TMCM-6214 offers 3 encoder connectors (5pin JST PH series) for motor axis 3 to 5 (with axis numbering
0 to 5).
Motor connector pin assignment
Pin
Label
Direction Description
1
GND
Signal and supply GND
2
+5V
out
for encoder supply. Max. 100mA per encoder / 300mA for all
three encoders together.
3
ENC_A
in
Encoder A channel input. +5V TTL signals and open-drain
signals (internal 4k7 pull-up to +5V) are accepted.
4
ENC_B
in
Encoder B channel input. +5V TTL signals and open-drain
signals (internal 4k7 pull-up to +5V) are accepted.
5
ENC_N
in
Encoder N channel input (Null / Zero channel). +5V TTL sig-
nals and open-drain signals (internal 4k7 pull-up to +5V) are
accepted.
Table 11: Encoder connector pin assignment
©2019 TRINAMIC Motion Control GmbH & Co. KG, Hamburg, Germany
Terms of delivery and rights to technical change reserved.
Download newest version at