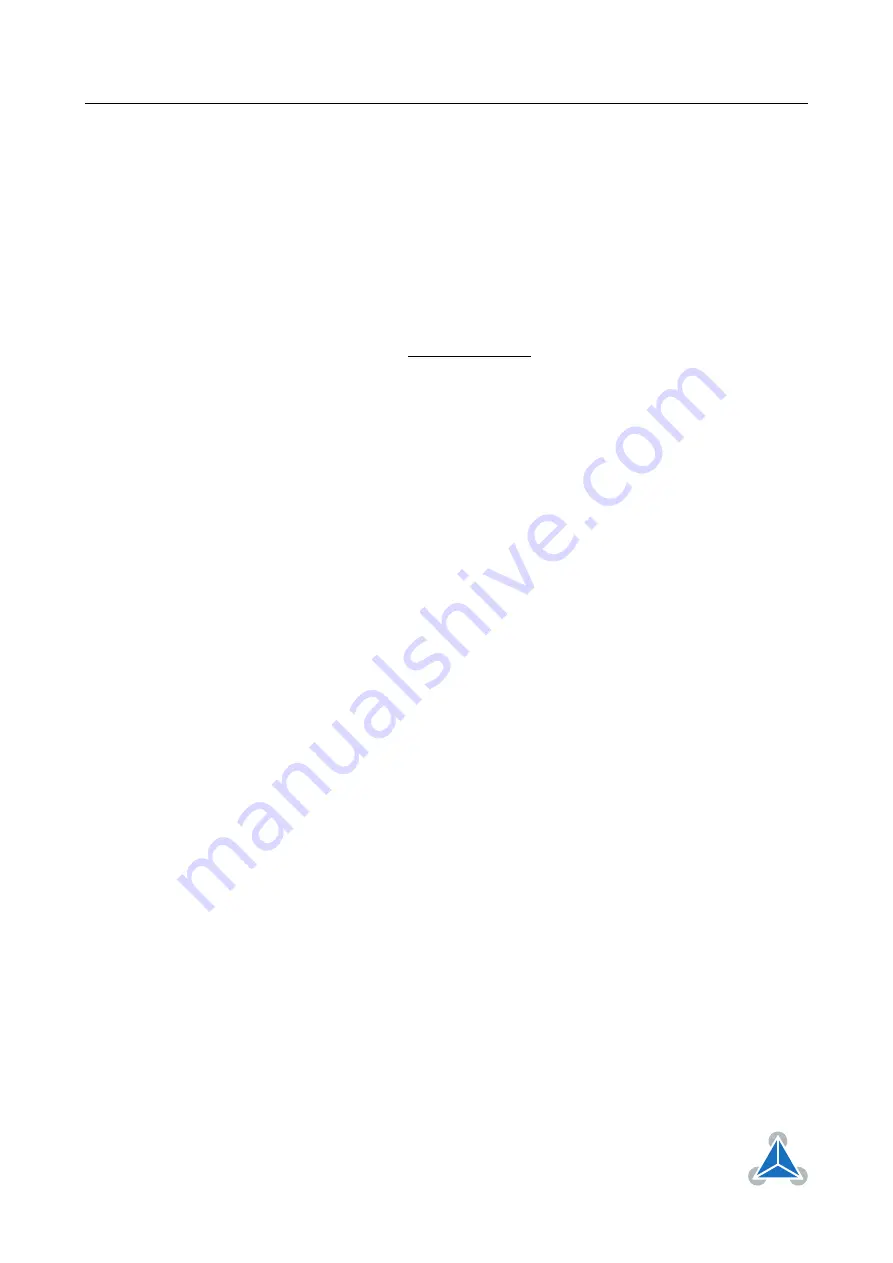
TMCM-1021 TMCL
™
Firmware Manual • Firmware Version V1.42 | Document Revision V1.10 • 2018-JAN-09
90 / 109
6
Module Specific Hints
This section contains some hints that are specific to the TMCM-1021 module.
6.1
Conversion between PPS, RPM and RPS
In order to convert between pps units and units like rounds per second (rps) or rounds per minute (rpm),
one has to know the fullstep resolution of the motor (full steps per round) and the microstep resolution
setting of the module (axis parameter #140, default setting is 256 microsteps per full step).
So to convert from pps to rps, use the following formula:
v
rps
=
v
pps
r
f ullstep
·
r
microstep
To convert from rps to rpm, use:
v
rpm
=
v
rps
·
60
With the following symbols:
•
v
rps
: velocity in rounds per second
•
v
rpm
: velocity in rounds per minute
•
v
pps
: velocity in pulses (microsteps) per second
•
r
f ullstep
: fullstep resolution of the motor (with most motors 200 (1.8°))
•
r
microstep
: microstep setting of the module (default 256)
So, with a 200 fullsteps motor and a microstep setting of 256 (axis parameter #140 = 8), a velocity of
51200pps will result in 1rps (60rpm).
6.2
The sensOstep™ Encoder
The TMCM-1021 module offers an integrated sensOstep encoder. This built-in encoder has a resolution of
1024 steps per rotation. Please consider the following hints when using the built-in encoder:
• The encoder counter can be read by software and can be used to monitor the current position of the
motor.
• To read out or to change the position value of the encoder use axis parameter #209. To read out the
position of the internal encoder use GAP 209, 0. The encoder position register can also be changed
using command SAP 209, 0, <n>, with n = -2147483648 . . . 2147483647.
• Axis parameter #210 is used to change the encoder settings. This also includes the prescaler of the
encoder. The prescaler is used to match motor resolution and encoder resolution.
• The motor can be stopped automatically if motor position and encoder position differ too much
(deviation error). This can be set using axis parameter #212 (maximum deviation). Setting this
parameter to 0 turns off this feature.
• As the built-in encoder is a magnetic encoder, the absolute position value can also be read. Use GAP
215, 0 to read the absolute (single-turn) position value. This always is a value between 0 and 1023
(independent of the prescaler setting).
©2018 TRINAMIC Motion Control GmbH & Co. KG, Hamburg, Germany
Terms of delivery and rights to technical change reserved.
Download newest version at