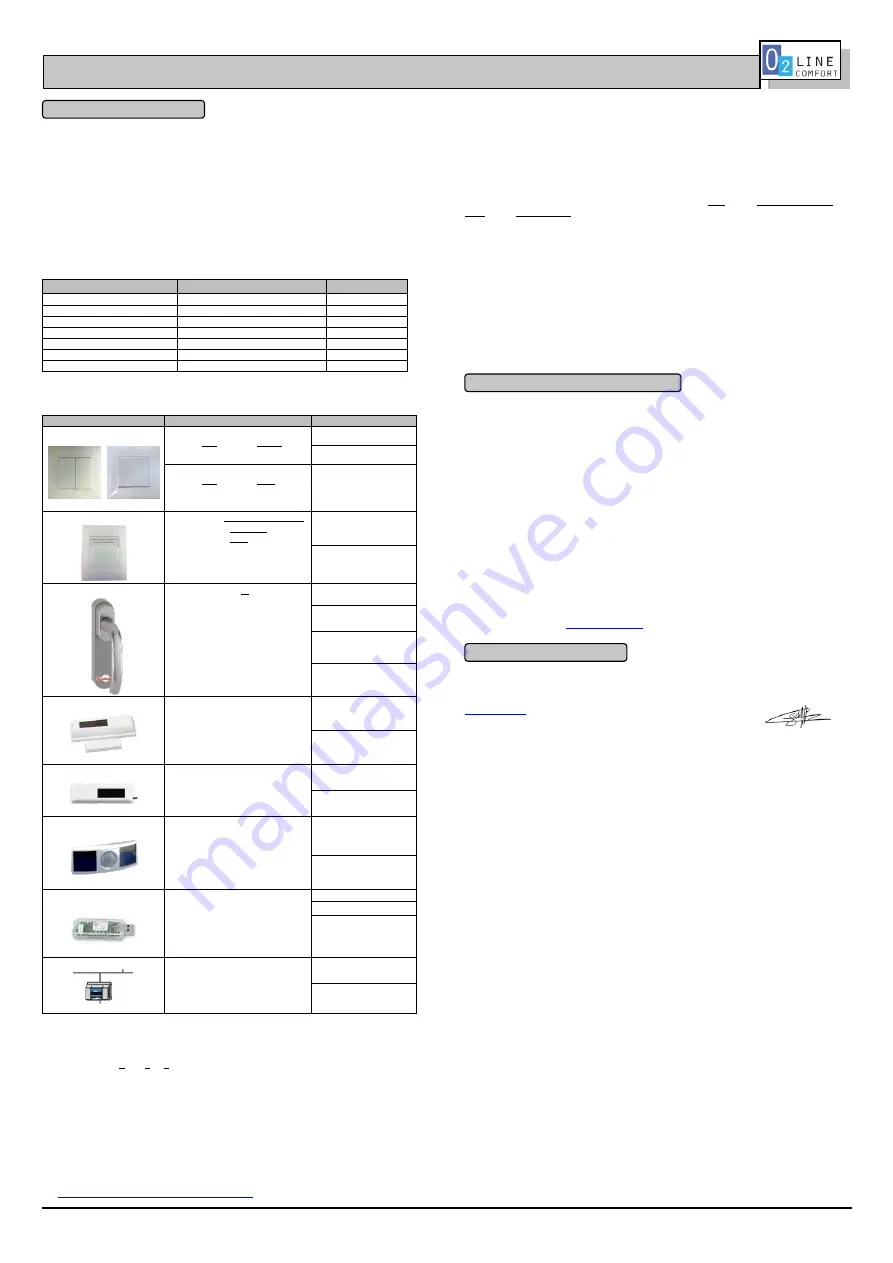
TOC1502NUbd_0418
4/4
TRI
0
2
SYS
sarl
–
8 grande rue le village, 21160 FLAVIGNEROT
Each receiver can receive up to a maximum of 32 transmitters, switches or sensors. Upon
allocating on the selected output the first transmitter or sensor, for the selected output, the
operating mode is defined. The operating mode cannot be changed until all the transmitters (the
two outputs) have been cleared using the
CLR
button.
Switch mode:
Each transmitter can be used to change the switching state, of the associated
output of the receiver. It is possible to switch
ON
(button
I
) with a switch and
OFF
(button
O
) with
another switch.
Window contact mode
(D5-00-01)
:
If at least one of the window contacts is open, this
activates
ON
the associated output of the receiver. If all possible window contacts are closed,
the associated output of the receiver is
OFF
. The window contacts transmit a signal
approximately every 15 minutes. 60 minutes after receipt of the last signal received, the receiver
considers this contact closed.
6.1 Compatible transmitters
The following transmitters can be associated with the receiver
10020086
:
Designation
0
2
LINE reference
EEP
1
Profil
Switch
10020001, 10020019, 10020022
F6-02-01
Key card
10020067
F6-04-01
Window Handle
10020011
F6-10-00
Window contact
10020032, 10020042
D5-00-01
Dry contact sensor
10020047, 10020057
D5-00-01
Occupancy sensor
10020051
A5-07-01
Gateway
10020040
A5-38-08
6.2 Transmitter associated functions
(switch mode)
The functions associated with different sensors are determined during learning. The learning
process (Cf § 5.1) is to do before activating the transmitter.
designation
Learning
Fonction obtained*
Switch
Button 1 (2, 3 or 4) :
pressed and released before
visual acknowledge
Button 1 (or 3) : ON
Button 2 (or 4) : OFF
Button 1 (2, 3 or 4) :
pressed and released after
visual acknowledge
EnOcean profil :
F6-02-30
(not in
EEP
1
)
Button 1 (2, 3 or 4) :
Transition from ON to
OFF and vice versa
(Switch mode only §6)
Key card
Card inserted before the entry into
learning mode, removed (in
learning mode) then
reinserted
Card inserted : ON
Card removed : OFF
Window handle
Closed to opened or opened to
closed
Tilt to opened : no
change
Opened to tilt : no
change
Closed to opened : OFF
Opened to closed : ON
Windows contact
Press the LEARN button
Magnet away : ON
Magnet near : OFF
Dry contact sensor
Press the LEARN button
Contact closed : OFF
Contact open : ON
Occupancy sensor
Press the LEARN button
Detection (PIR = On) :
ON
Detection (PIR = OFF) :
OFF
Gateway
Protocol UTE (see §5.1)
EEP A5-38-08
1
, command 01
control switch, only
SW=0 : OFF
SW=1 : ON
immediate or delayed
with or without (0s)
delay of 1 second at
1h45
BMS product
Protocol UTE (see §5.2)
EEP D2-01-11
1
, command 01
control switch and command 03
querying of status
(acknowledgment)
OV=0x00 : OFF
OV=0x64 : ON
Note: * The ON state corresponds to the lighting of the LED (on the front of the product) and
contact closure outputs NO.
6.3 Radio function test
(slave)
This RLT function (Radio Link Test, EEP §A5-3F-00
1
) master slave allows, through a diagnostic
product (master), to perform a radio test range (slave):
a) On the diagnostic product, activate the master RLT mode (refer to its manual instruction)
b) On this receiver, activate the slave RLT mode by a short press (approximately 0,5s) on
LRN
and
CLR
simultaneously. This mode is confirmed by the flashing (orange) regular of
LED
.
c) To exit this function, short press (approximately 0,5s) on the
LRN
button. The output is
confirmed by the stopping of regular flashing of
LED
. In the absence of test activity, this function
stops automatically after 30 seconds.
1
frame description is described in the
EnOcean Equipment Profiles EEP2.6
document available
on:
www.enocean-alliance.org/en/enocean_standard
6.4 Inversion of the output contact
This function allows the reversal of the operation of the output contact. In reverse mode, when
the
LED
(product front) is on, then the output contact is open (load off) and vice versa.
To enter the inversion mode:
a) Power down this receiver
b) Press the
CLR
button
c) Power up this receiver, while maintaining press the
CLR
button
d) As soon as the
LED 1
is on orange, release the
CLR
button immediately. The state of the
inversion of the output is shown by the flashing of the
LED,
long for the non-inverted mode and
short for the reverse mode:
a) To change the inversion mode of the output, short press (approximately 0.5s) the
LRN
button. This new mode is confirmed by the change of flashing of
DEL
.
b) To select channel 2, short press (approximately 0,5s) the
CLR
button. This change is
confirmed by the extinction of the
LED 1
and the flashing corresponding to the reverse mode of
output 2 on the
LED 2
.
c) To exit this mode, short press (approximately 0.5s) the
CLR
button. The output is
confirmed by the stopping of regular flashing of the
LED
.
This feature allows the reversal of the operation of the output contact. In reverse mode, when the
LED
(in product facade) will be lit, then the output will open its contact (off load) and vice versa.
Notes:
– The output 1 and 2 is not inverted (load off) as supplied state.
– The output contact is electrically open (load off), even if a reverse mode is programmed (load
on) at power down of the receiver the output contact is open: load off.
7.1 New or existing installation
• Check the circuit breaker, the electrical supply and the load connected to the receiver
associated with this sensor (qualified electricians).
• Check the connected load and the connecting cables (qualified electricians).
• If the receiver functions at a shorter distance relative to the sensor, it is subject to interference
or used outside the transmission range.
• Search the system environment for changes that could cause the interference (for example
movement of metallic cabinets, furniture or partitions).
• Use the sensor or receiver in a more suitable locations.
• Clear the receiver and perform a new learn process.
7.2 Automatic activation of the receiver
• The cause may be the activation of a sensor external to the system which has by chance been
programmed on the receiver.
• Clear the receiver and perform a new learn process.
7.3 Limitation of the range of the radio signals
• Transmitter/receiver used close to metallic objects or close to materials containing metallic
elements. Observe a distance of at least 10cm.
• Humidity in the materials.
• Device emitting high frequency signals such as: audio and video systems, computers,
electronic ballasts or fluorescent tubes. Observe a distance of at least 0,5m.
7.4 Contacts
E-mail:............................
This product can be marketed and distributed in the countries of the European Union. Hereby
declares that radio equipment
10020086
is in compliance with directive 2014/53/EU,
known as the RED Directive.
The full text of the EU declaration of conformity is available at the following internet address:
D.Girard
6. Commande et fonctions
7. Troubleshooting
8. Declaration of conformity
0
2
LINE
2
1
1
2
4
3
TRI
0
2
SYS