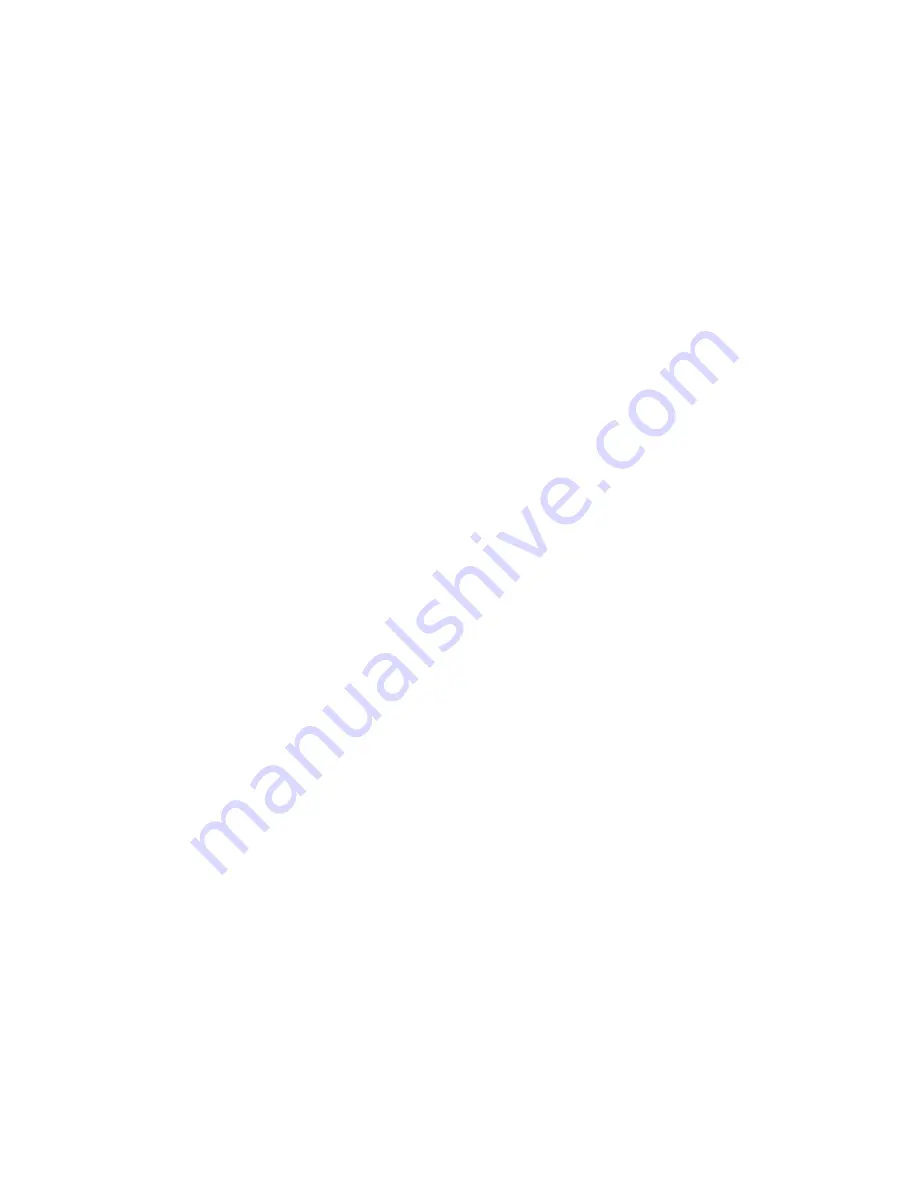
VI. COMPONENT FUNCTION
Compressor
Pumps refrigerant through refrigeration lines and components.
Condenser Fan
Draws air across condenser coil to aid in removing heat from the refrigerant and
moves air across compressor to aid in cooling the compressor.
Dual Pressure Control
Low side monitors suction pressure at compressor. Shuts compressor OFF when
(TBC1H & TBC2H only)
low pressure setting is reached (cut-out). Allows compressor to run when
pressure rises to cut-in setting.
High side monitors discharge pressure at compressor. Shuts compressor OFF
when high side pressure setting is reached (cut-out). Allows compressor to run
when pressure returns to cut-in setting.
The differential is the difference in pressure between open and closed states of the
pressure switch.
Start Capacitor
Wired in series with the start windings to help start compressor motor.
Run Capacitor
Continually in circuit to help compressor motor during operation.
Thermal Overload
Removes power from compressor if the internal temperature of the compressor
becomes too high (auto reset).
Start Relay
Senses current of run winding of compressor motor. Normally open contacts
close when run winding draws a high amperage at start and brings the start
capacitor and start windings into the circuit. As the motor reaches operating
speed (less amperage through run winding), the normally open contacts open and
removes the start capacitor and start windings from the circuit.
Evaporator Fan
Draws air from the cabinet and moves air through the evaporator coil.
Defrost Heater
Defrosts evaporator coils and prevents water droplets from evaporator coil from
freezing before they can drain to the condensate pan. Operates only during
defrost cycle.
Air Temperature Sensor
Monitors air temperature inside the cabinet.
Coil Temperature Sensor
Monitors the suction line temperature at evaporator during defrost cycle.
Food Temperature Probe
Monitors temperature of food product.
Solenoid Valve
Normally closed. When energized, allows refrigerant to flow from receiver to
evaporator coil.
Door Perimeter Heater
Prevents condensate on door frame.
Controller
Performs the following functions:
a) Displays all data for the current mode of operation.
b) Cycles refrigeration system to maintain cabinet temperature.
c) Monitors power failures.
Power Supply Boards
Provides DC voltage to control system.
Relay Board
Performs the following functions:
a) Cycles fans.
b) Controls outputs to heaters and compressor relays.
Thermal Fuse
TBC1H, TBC1HR, TBC2H and TBC2HR only. Monitors cabinet air temperature.
Opens circuit to defrost heater if cabinet temperature exceeds 230°F.
-7-
Содержание TBC13
Страница 17: ... 16 IX WIRING DIAGRAM MODEL TBC5 ...
Страница 18: ... 17 X WIRING DIAGRAM MODEL TBC13 ...
Страница 19: ... 18 XI WIRING DIAGRAM MODEL TBC1H TBC1HR ...
Страница 25: ... 24 ...