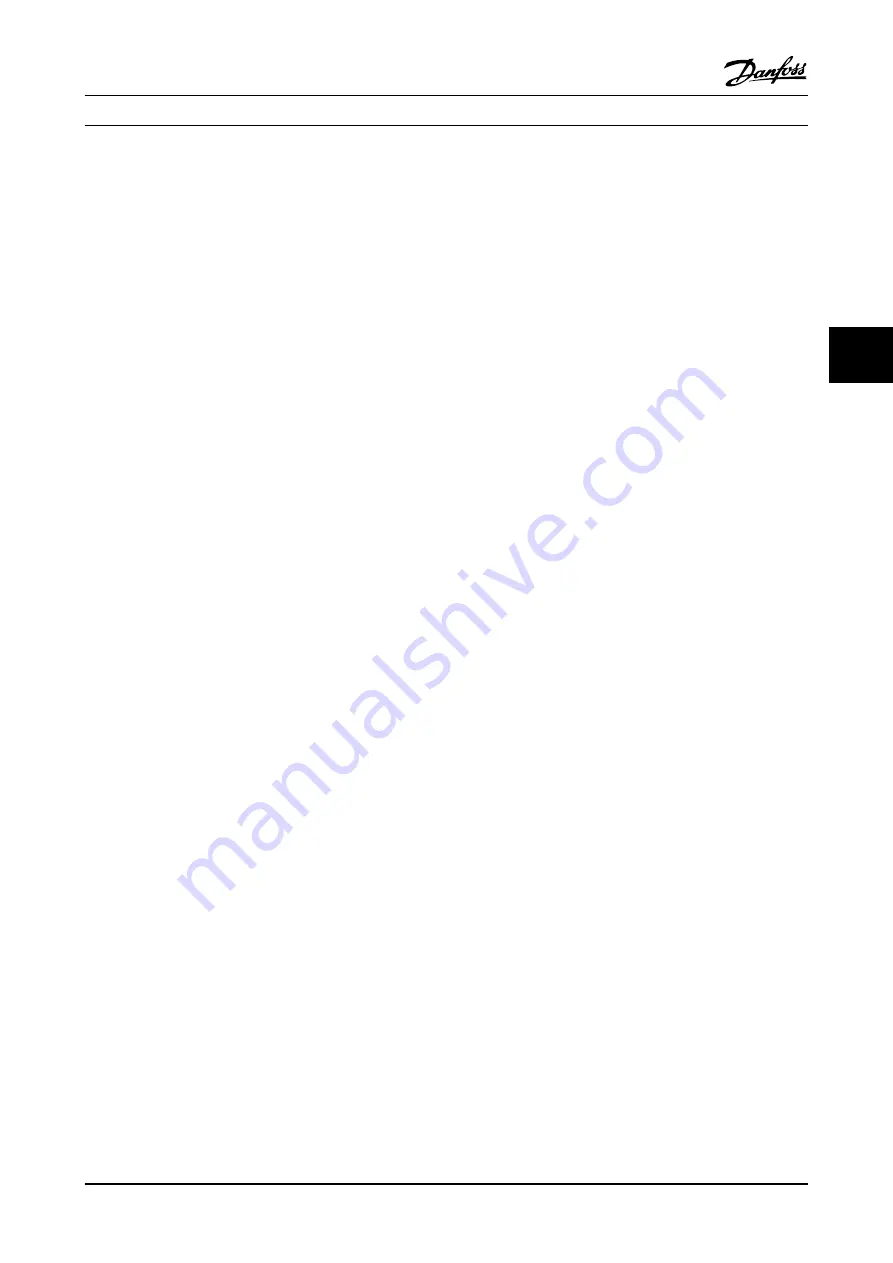
CAUTION
MOTOR START!
Ensure that motor, system, and any attached equipment is
ready for start. Failure to do so could result in personal
injury or equipment damage.
5.
If a bypass is connected, place the Mode Selector
Switch in drive mode. Apply power by turning
the main disconnect switch to the ON position.
6.
Enter drive programming data per the drive
instruction manual.
7.
Check motor rotation direction in drive control as
follows.
7a
Put panel in drive mode.
7b
Hand start drive at minimum speed (see
drive instruction manual for details).
7c
Confirm directional rotation.
7d
If incorrect, stop the drive, remove
power, and lock out.
7e
Reverse connection of T1 & T2 motor
leads. Do not change incoming power
leads.
7f
Remove lockout and apply power.
7g
Confirm directional rotation.
8.
Check motor rotation direction in bypass as
follows.
8a
Momentarily bump motor in bypass.
8b
Confirm directional rotation.
8c
If incorrect, stop drive, remove power,
and lock out.
8d
Reverse connection of L1 & L2 input
power leads to the main disconnect. Do
not change motor leads.
8e
Confirm directional rotation.
CAUTION
FULL SPEED OPERATION!
Ensure that the motor, system, and any attached
equipment is ready for full speed operation. The user
assumes all responsibility for assuring the system is able to
safely run at full speed. Failure to ensure that the motor,
system, and any attached equipment is ready for full speed
operation could result in equipment damage.
9.
Check motor current in drive mode on the motor
terminals.
9a
Put the unit in drive mode.
9b
Check motor current on motor terminals
T1, T2, and T3. Verify the motor amps
are within drive and motor rated current
and are balanced within 3%. If incorrect,
see
for
isolation procedures.
9c
Check input current on input terminals
L1, L2, and L3. Verify that current is
within FLA of drive and balanced within
3%. If incorrect, see
for isolation procedures.
10.
Check motor current in bypass mode on the
motor terminals.
10a
Put the unit in bypass mode.
10b
Check full load amps on terminals T1,
T2, and T3. Verify the motor amps are
within motor FLA rated current and
balanced within 3%. If incorrect, see
for isolation
procedures.
For steps 11-13, see
5 Electromechanical Bypass (EMB2)
and
6 Electronically Controlled Bypass (ECB)
for details.
11.
Check operation of any optional functions to
confirm that they work, as applicable. Options
may include run permissive, fire mode, common
start/stop, or others.
12.
Exercise the safety circuit and verify that the unit
stops running.
13.
Exercise the start/stop circuit and verify that the
unit starts and stops with the system in the Auto
mode of operation.
Start Up
Vertical Bypass/Non Bypass Panel
MG.13.A1.22 - VLT
®
is a registered Danfoss trademark
4-3
4
4
Содержание VLT AQUA Drive FC 202 VLT AutomationDrive FC 301
Страница 1: ...MAKING MODERN LIVING POSSIBLE Instruction Manual Vertical Bypass Non Bypass Panel...
Страница 3: ...Safety Vertical Bypass Non Bypass Panel MG 13 A1 22 VLT is a registered Danfoss trademark...
Страница 45: ...Installation Vertical Bypass Non Bypass Panel 3 28 MG 13 A1 22 VLT is a registered Danfoss trademark 3 3...
Страница 49: ...Start Up Vertical Bypass Non Bypass Panel 4 4 MG 13 A1 22 VLT is a registered Danfoss trademark 4 4...
Страница 88: ...www danfoss com drives MG13A122 130R0264 MG13A122 Rev 2011 08 10...
Страница 89: ......