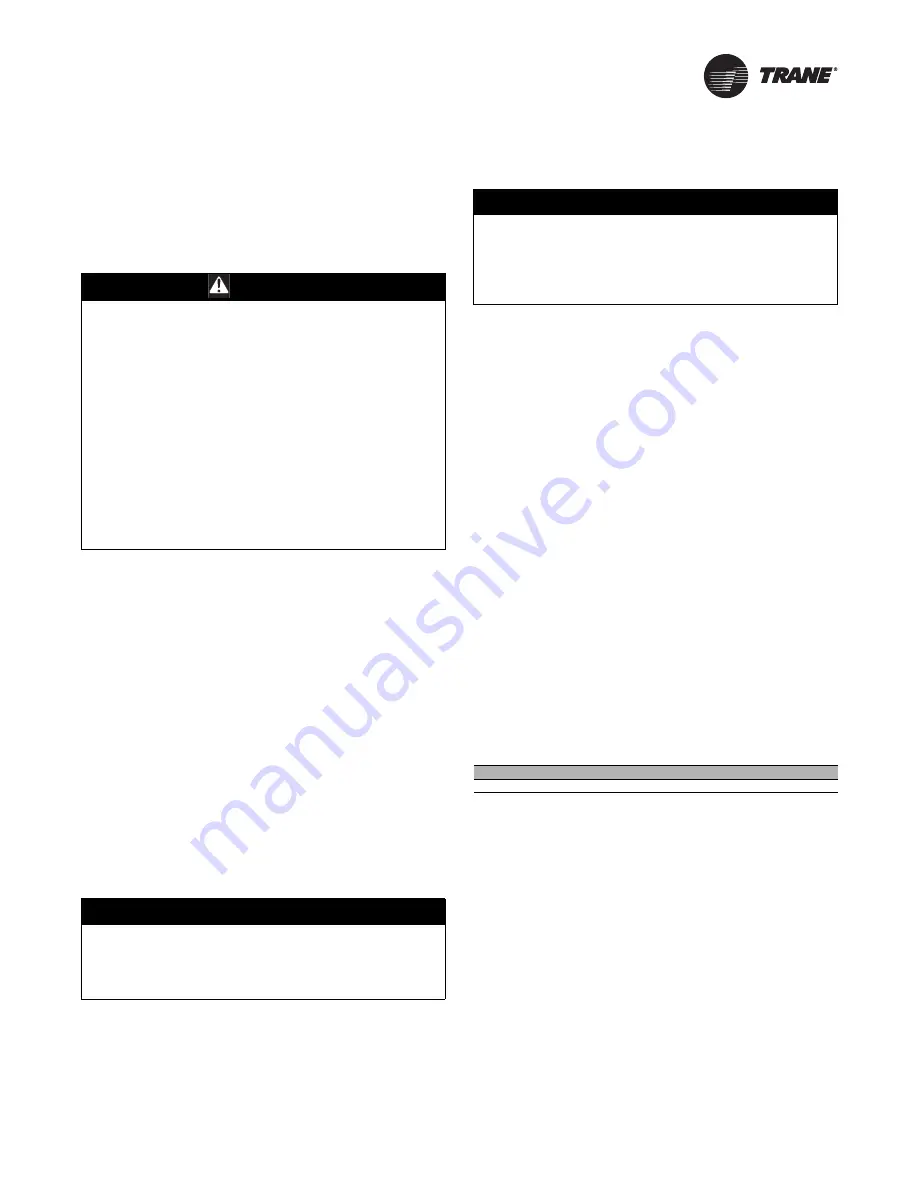
CLCH-SVX009A-EN
43
Electrical Requirements
Unit Wiring Diagrams
Specific unit wiring diagrams are provided on the inside of
the control panel door. Use these diagrams for
connections or trouble analysis.
Supply Power Wiring
It is the installer’s responsibility to provide power supply
wiring to the unit. Wiring should conform to NEC and all
applicable code requirements. When units are ordered
without controls, the contractor must also furnish an on/
off switch, thermostat, and a fused disconnect switch in
compliance with national and local electrical codes.
Bring supply wiring through the knockout in the unit
control box. Connect the three phase wires to the power
terminal block or the non-fused disconnect switch in the
control box terminals. Refer to specific wiring diagrams
and fuse information in the unit’s control panel.
Refer to unit specific wiring diagrams for specific wiring
connections. Locate unit wiring diagrams on the inside of
the control box cover. Refer to the unit nameplate for unit
specific electrical information, such as voltage, minimum
circuit ampacity (MCA), and maximum fuse size (MFS).
Electrical Grounding Restrictions
All sensor and input circuits are normally at or near ground
(common) potential. When wiring sensors and other input
devices to the control interface or controller, avoid
creating ground loops with grounded conductors external
to the unit control circuit. Ground loops can affect the
measurement accuracy of the controller.
All input/output circuits (except isolated relay contacts and
optically isolated inputs) assume a grounded source,
either a ground wire at the supply transformer to control
panel chassis, or an installer supplied ground.
Note:
Do not connect any sensor or input circuit to an
external ground connection.
The installer must provide interconnection wiring to
connect wall mounted devices such as a zone sensor
module. Refer to the unit wiring schematic for specific
wiring details and point-to-point wiring connections.
Dashed lines indicate field wiring on the unit wiring
schematics. All interconnection wiring must conform to
NEC Class 2 wiring requirements and any state and local
requirements. Refer to
Table 9
for the wire size range and
maximum wiring distance for each device.
Important recommendation
Do not bundle or run interconnection wiring in parallel
with or in the same conduit with any high-voltage wires
(110 V or greater). Exposure of interconnection wiring to
high-voltage wiring, inductive loads, or RF transmitters
may cause radio frequency interference (RFI). In addition,
improper separation may cause electrical noise problems.
Therefore, use shielded wire (Beldon 83559/83562 or
equivalent) in applications that require a high degree of
noise immunity. Connect the shield to the chassis ground
and tape at the other end.
WARNING
Hazardous Voltage w/Capacitors!
Disconnect all electric power, including remote
disconnects and discharge all motor start/run
capacitors before servicing. Follow proper lockout/
tagout procedures to ensure the power cannot be
inadvertently energized. For variable frequency drives
or other energy storing components provided by Trane
or others, refer to the appropriate manufacturer’s
literature for allowable waiting periods for discharge of
capacitors. Verify with an appropriate voltmeter that all
capacitors have discharged. Failure to disconnect power
and discharge capacitors before servicing could result
in death or serious injury.
For additional information regarding the safe discharge
of capacitors, see PROD-SVB06A-EN
NOTICE:
Use Copper Conductors Only!
Unit terminals are not designed to accept other types
of conductors. Failure to use copper conductors could
result in equipment damage.
NOTICE:
Motor Winding Damage!
Do not use a megohm meter or apply voltage greater
than 50 Vdc to a compressor motor winding while it is
under a deep vacuum. Voltage sparkover could cause
damage to the motor windings.
Table 9.
Zone sensor maximum wiring distance
Wire Size Range
Max. Wiring Distance
16-12 AWG
200 ft