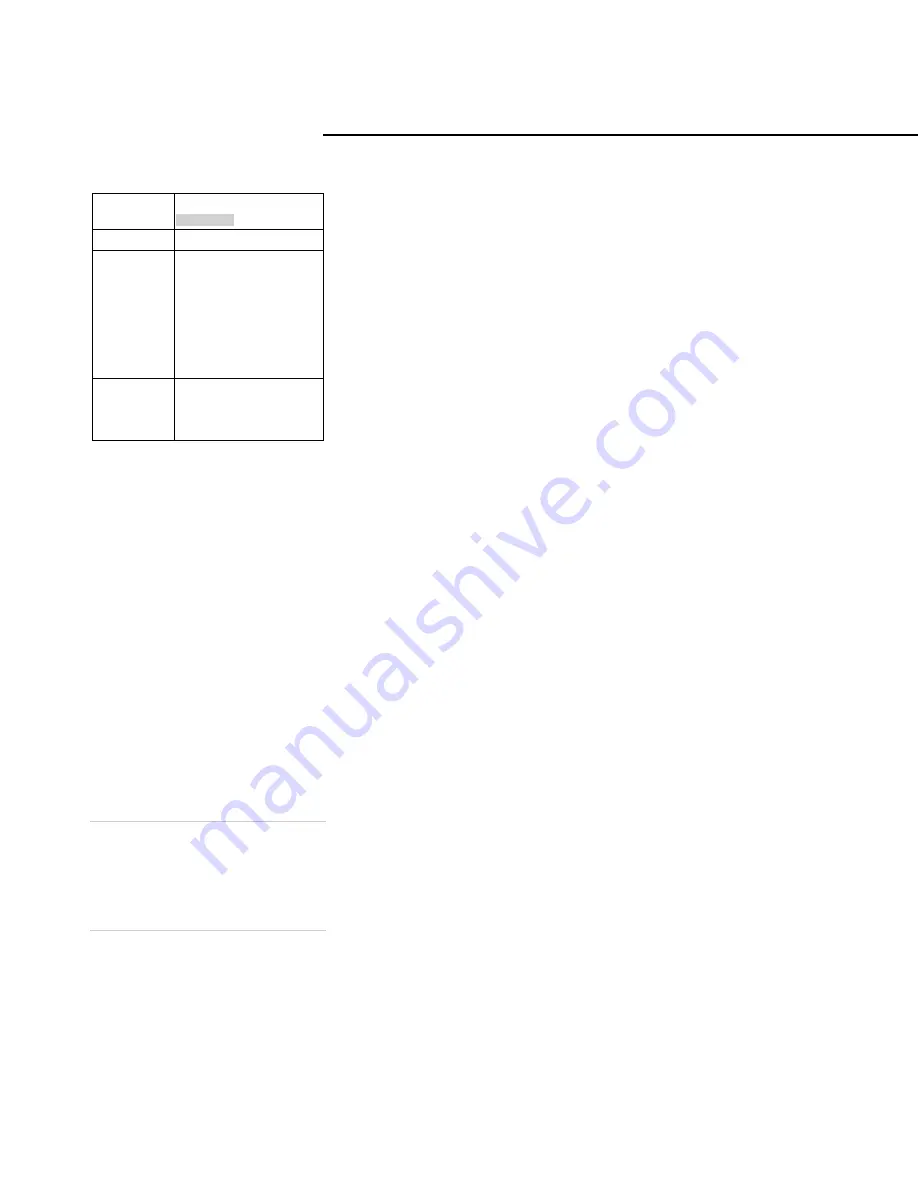
14
The ZN510 controller receives the
fan mode from either a wired zone
sensor or as a communicated valve.
When neither a zone sensor nor
communicated fan mode are
present, the ZN510 controller will
default unit operation to
AUTO
.
Note:
z
A building automation system
can also generate a fan mode
request and communicate this
request to the controller.
z
If the ZN510 controller does not
receive a hardwired or commu-
nicated request for the fan
mode, the unit recognizes the
fan input as
AUTO
and the fan
operates according to the
default configuration.
Fan Off Delay
When the heating output is
controlled off, the ZN510
automatically runs the fan
ON
for an
additional 30 seconds to give the fan
time to blow off any residual heat.
Possible
Fan Modes
Heat Pump
(1-speed)
OFF
Fan Off
AUTO
Continuous: (Field
Modified)
z
In occupied mode, the
fan runs continuously.
In unoccupied mode,
the fan cycles
OFF
when no heating or
cooling is required.
AUTO
Cycling: (Factory Default)
z
The fan cycles
ON
and
OFF
with compressor
operation.
Unit Operation
Leaving Water Temperature
ZN510 uses analog input 1 (AI 1) as
the leaving water temperature input
for use with a thermistor. This input
(AI 1) is automatically assigned as a
leaving water temperature input. As
explained in the binary input
section, the leaving water
temperature input protects the heat
exchanger (circuit 1) from low
temperatures. The second heat
exchanger, present in units with two
compressors is protected with a
binary low temperature detection
device. Based on the application of
the unit, circuit operation is
terminated when the leaving water
temperature falls below 35 F or
20 F. This is set when the unit is
ordered.
The ZN510 controller compares the
measured leaving water
temperature to the leaving water
temperature low limit value to
determine a fault condition. When
the measured leaving water
temperature is less than the leaving
water temperature low limit, the
controller generates a Low Temp
Detect diagnostic. If the Leaving
Water Temp Sensor fails to open or
close the controller generates a
Leaving Water Temp Failure
diagnostic. This disables unit
operation.
Note:
A low temperature detection failure
diagnostic for compressor 1 may
require you to manually reset the
unit to restore compressor opera-
tion.
Similarly, the ZN510 controller uses
a binary low temperature detection
device (fixed low limit trip point) to
lock-out circuit 2 when a fault condi-
tion is detected.
See the Diagnostics section on page
28 for information about the
automatic diagnostic reset function.
Filter Maintenance Timer
The controller’s filter maintenance
timer is based on the unit fan’s
cumulative run hours. The controller
compares the fan run time against
an adjustable fan run hours limit
(maintenance required setpoint
time, stored in the controller) and
recommends unit maintenance (i.e.
changing the filter).
Use Rover or BAS system to edit the
maintenance required setpoint time.
Once the setpoint limit is exceeded
the controller generates a filter
maintenance timer diagnostic.
When the maintenance required
setpoint time is zero, the controller
disables the diagnostic feature.
Discharge Air Temperature
Analog input 2 (AI 2) is used as the
discharge air temperature input for
use with a 10,000 ohm thermistor.
Typical factory placement of the
thermistor is at the discharge area of
the unit. The discharge air
temperature sensor does not affect
unit operation. The measured
temperature is for information only
to be read by the building
automation system or for
troubleshooting unit operation with
Rover.
Once a valid discharge air
temperature signal has been
established by the thermistor or
communicated and the value is no
longer present, the controller
generates a discharge air
temperature failure diagnostic. This
will not disable unit operation. If the
sensor returns with a valid
temperature, the diagnostic
automatically clears
Содержание Tracer ZN510
Страница 1: ...WSHP IOP 2 May 1998 Installation Operation and Programming Tracer ZN510 Controller...
Страница 29: ...29 Wiring Diagram...
Страница 30: ...30 Wiring Diagram...