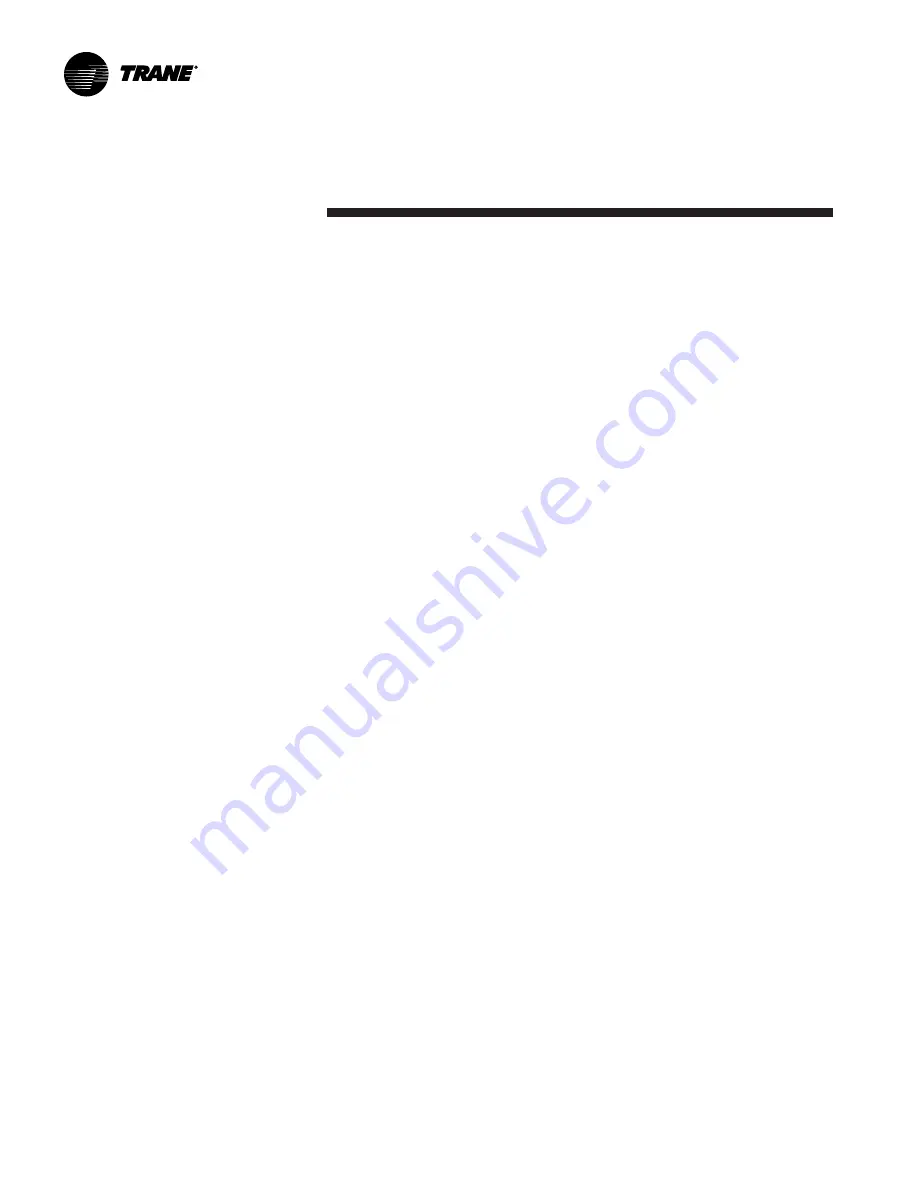
CDHF-SVN01B-EN
6
Figure 1 – Information from a Typical CDHF Unit Nameplate
General Information
MODEL: CDHF2000 DATE OF MFG (DD/MM/YY): @TODAY05
MODEL NO:
CDHF2000KR0TA2802745B0A106B0A1CFFRR10W4C0010330001S
SERIAL NO: S.O. NO: SAMPLE
RATED VOLTAGE: 4160 VOLTS 60 HZ 3 PH
VOLTAGE UTILIZATION RANGE: 3744-4576 VAC
LH CIRCUIT RH CIRCUIT
MINIMUM CIRCUIT AMPACITY: 96 AMPS 103 AMPS
MAXIMUM OVERCURRENT
PROTECTIVE DEVICE: 150 AMPS 175 AMPS
COMPRESSOR MOTOR MAX
VOLTS-AC HZ PH RLA KW LRAY
LH CIRCUIT 4160 60 3 75 480 400
RH CIRCUIT 4160 60 3 82 523 473
VOLT HZ PH
OIL TANK HEATER (LH&RH): 115 60 1 750 WATTS
CONTROL CIRCUIT (LH&RH): 115 60 1 4000 VA MAX
CARBON TANK HEATER (LH&RH):115 60 1 1.7 RLA
PUMPOUT COMPRESSOR(LH&RH): 115 60/50 1 1.55 RLA
PURGE COMP MTR(LH&RH): 115/110 60/50 1 8RLA 34.6LRA
WHEN MOTOR CONTROLLER PROVIDED BY OTHERS
TRANE ENGINEERING SPEC. S6516-0513 APPLIES
REFRIGERANT SYSTEM LH RH
FIELD CHARGED WITH: 1850 1850 LBS. OF R-123
ACTUALLY CHARGED WITH: LBS. OF R-123
MAXIMUM WORKING PRESSURE: 15 15 PSIG HIGH SIDE
MAXIMUM WORKING PRESSURE: 15 15 PSIG LOW SIDE
FACTORY TEST PRESSURE:
HIGH SIDE 45 PSIG LOW SIDE 45 PSIG
FIELD LEAK TEST PRESSURE 8 PSIG MAX.
TESTED AT PSIG
MANUFACTURED UNDER ONE OR MORE OF THE FOLLOWING
U.S. PATENTS: 4232533 4686834 4689967 4715190
4751653 4800732 5031410 5056032 5058031 5355691
5434738 5537830 5553997 5563489 5600960 5675978
5836382 5848538 6065297 6098422 6250101
SERVICE LITERATURE
INSTALLATION MANUAL: CDHF-SVN01A-EN
OPERATION/MAINTENANCE MANUAL: CDHF-SVU01A-EN
PRODUCT DESCRIPTION:
TVSQ
1
PTON 1975
VTR1
165
VTR2
165
CTM1 75
CTM2
100
MAC1
6
MAC2
6
MODL CDHF
DSEQ R0
NTON 2000
VOLT 4160
HRTZ 60
CPM1 512
CPD1 280
CPM2 588
CPD2 274
EVSZ 210D
EVBS 1850
EVTM TECU
EVTH 35
EFLD WATE
EVWT MAR
EVWP 1
EVWC STD
EVPR 150
EVCO VICT
EVWA RRLR
CDSZ 210D
CDBS 1900
CDTM TECU
CDTH 35
CFLD WATE
CDWT MAR
CDWP 1
CDWC STD
CDPR 150
CDCO VICT
CDWA LFRF
ORC1 1265
ORC2 1265
AGLT UL
TEST CWSP
TTOL SPCL
WCNM BNMP
CNIF CH53
OPST YES
WPSR WFC
TRMM TRM4
EPRO YES
CDRP YES
SPKG DOM
ASCL OUTS
APTY STD
SRT1 CXL
SRT2 CXL
SOPT 3RTD
GENR NO
Содержание Duplex Water-Cooled Hermetic CenTraVac
Страница 10: ...CDHF SVN01B EN 10 Figure 2 Typical CDHF Chiller General Information ...
Страница 38: ...CDHF SVN01B EN 38 Vent Line Piping Figure 20B Continued ...
Страница 39: ...39 CDHF SVN01B EN Vent Line Piping Figure 20C Continued ...
Страница 40: ...CDHF SVN01B EN 40 Vent Line Piping Figure 21 Rupture Disc Vent Pipe Sizing ...
Страница 42: ...CDHF SVN01B EN 42 Figure 22 Recommended Areas for Unit Insulation ...
Страница 59: ...59 CDHF SVN01B EN ...
Страница 60: ...CDHF SVN01B EN 60 ...
Страница 61: ...61 CDHF SVN01B EN ...
Страница 62: ...CDHF SVN01B EN 62 ...
Страница 63: ...63 CDHF SVN01B EN ...
Страница 64: ...CDHF SVN01B EN 64 ...
Страница 65: ...65 CDHF SVN01B EN ...
Страница 66: ...CDHF SVN01B EN 66 ...
Страница 67: ...67 CDHF SVN01B EN ...
Страница 68: ...CDHF SVN01B EN 68 ...
Страница 69: ...69 CDHF SVN01B EN ...
Страница 70: ...CDHF SVN01B EN 70 ...
Страница 71: ...71 CDHF SVN01B EN ...
Страница 72: ...CDHF SVN01B EN 72 ...
Страница 73: ...73 CDHF SVN01B EN ...
Страница 74: ...CDHF SVN01B EN 74 ...
Страница 75: ...75 CDHF SVN01B EN ...
Страница 76: ...CDHF SVN01B EN 76 ...
Страница 77: ...77 CDHF SVN01B EN ...
Страница 78: ...CDHF SVN01B EN 78 ...
Страница 79: ...79 CDHF SVN01B EN ...