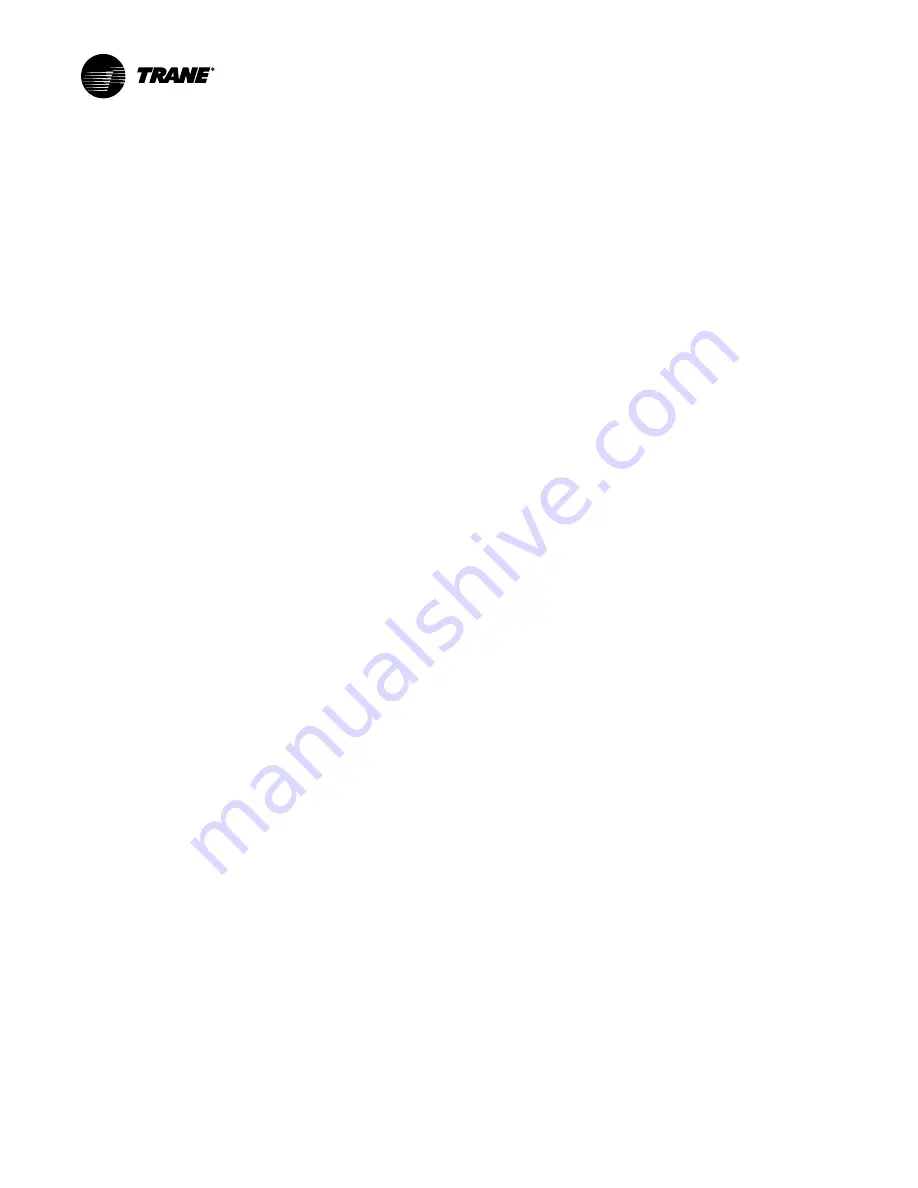
ARTC-SVX006A-EN
43
Sequence of Operations
This manual describes a typical air-to-water heat pump
system with few, if any, optional components or devices
attached.
Bank Controls Sequence
1. Air-to-Water Heat Pump machine can operate either in
Cooling or Heating Mode. Operational Thermal Mode is
defined by building needs for providing either chilled or
hot water and can be commanded from BMS or local
display user interface.
2. In Cooling Mode for both refrigeration circuits
Reversing Valves connect suction side to Water Load
Heat Exchanger, so it produces a cold water to satisfy
cooling load. Discharge side is connected to Air-Source
Coils, which are shared by both refrigeration circuits, so
Fan Bank, installed on the Air-Source Coils, rejects
generated heat when any refrigeration circuit is
running.
3. In Heating Mode both circuits Reversing Valves
connect discharge side to Water Load Heat Exchanger,
so it produces a hot water to satisfy heating load.
Suction side, in turn, is connected to Air-Source Coils,
so running Fan Bank facilitates a heat transfer to/from
environment.
4. Air-to-Water Heat Pump Bank can be turned on and off
from BMS system via communication channel or via
digital input signal DI 1 on the Primary Controller.
5. Besides, each Air-to-Water Heat Pump Module can be
turned on and off individually by the same means.
6. When Air-to-Water Heat Pump Bank turns on, Primary
Module tries to identify on the communication network
the required number of Secondary Modules according
to the Air-to-Water Heat Pump Bank number of
Modules setting. Secondary Modules that respond to
the Primary Controller, will become the part of the Air-
to-Water Heat Pump Bank, otherwise, non-responding
Modules, will run in Stand-alone mode if corresponding
conditions are met.
7. In addition to Secondary Modules communication
conditions, Primary Controller has to meet other
conditions to be able to act as a Primary Module, such
as, System Temperature Control Sensor has to be
intact and Primary Controller itself has to communicate
with other Secondary Controllers as well. When
mentioned conditions are not met, all Air-to-Water Heat
Pump Modules will switch automatically to Stand-alone
mode.
8. Once Primary and Secondary Modules have been
claimed, Primary Controller defines the Lead Module
which will keep its Load/Source (if option selected)
Isolation Valves opened at all times to allow for flow
circulation.
9. Lead Module is rotated through Air-to-Water Heat
Pump Bank based on time period or based on the
chiller demand. Both options can be enabled/disabled
individually. When Time Rotation is enabled, Rotation
Period has to expire before Lead is rotated. Demand
Rotation rotates Lead when the last compressor is
staged off.
10. Primary Controller constantly monitors the Controlled
Temperature and checks if it falls within Temperature
Control Band. Temperature Control Band is the zone
around Temperature Setpoint where Cooling / Heating
Demand is modulating. When Load Water Controlled
Temperature is below Control Band for Cooling Mode,
Cooling Demand is 0%; when Load Water Controlled
Temperature is above Control Band, Cooling Demand
is 100%. When Load Water Controlled Temperature is
changing within Temperature Control Band, Cooling
Demand is modulating accordingly. The same goes for
Heating Demand except for when Load Water
Temperature is below Control Band, Heating Demand
is 100% and when it is above Control Band, Heating
Demand is 0% as heating temperature control is
reversed versus cooling temperature control.
11. Compressors staging sequence always starts off from a
Lead Module. When Bank Demand is 100%,
compressors stage up; when Bank Demand is 0%,
compressors stage down. Once next compressor
comes on, Stage-up Delay has to expire before next
compressor is allowed to turn on. The same goes for
staging-down, Stage-Down Delay has to count down to
‘0’ before next compressor turns off.
12. When next Heat Pump Module comes into operation, it
first opens its Load Isolation Valve. While Isolation
Valve is opening, pumps ramp up to readdress
increased flow demand. When Load Flow is confirmed
by flow switch, compressors are allowed to start.
13. When Bank Demand reaches 0%, Air-to-Water Heat
Pump Bank goes into staging-down sequence.
Staging-down always starts from the compressor that
was engaged last implementing LIFO sequence (Last
In First Out).
14. When the last compressor on the Heat Pump Module
stops, Isolation Valve starts closing. Pumps in
corresponding circuits ramp down to adjust speed to a
decreased flow demand.
15. For Air-to-Water Heat Pump Bank, Running in Heating
Mode at low ambient temperature, Air-Source Coils of
the module tend to frost up. The lower the ambient
temperature, the faster frosting can develop.
16. To avoid Air-Source Coils frosting, module intermittently
goes in Defrost Mode when respective conditions are
met.
17. When running in Defrost Mode, module runs a reversed
refrigeration cycle thus diminishing Air-to-Water Heat
Pump Bank heating capacity.
Содержание Arctic Thermafit AXM
Страница 69: ...ARTC SVX006A EN 69 Notes...
Страница 70: ...70 ARTC SVX006A EN Notes...
Страница 71: ...ARTC SVX006A EN 71 Notes...