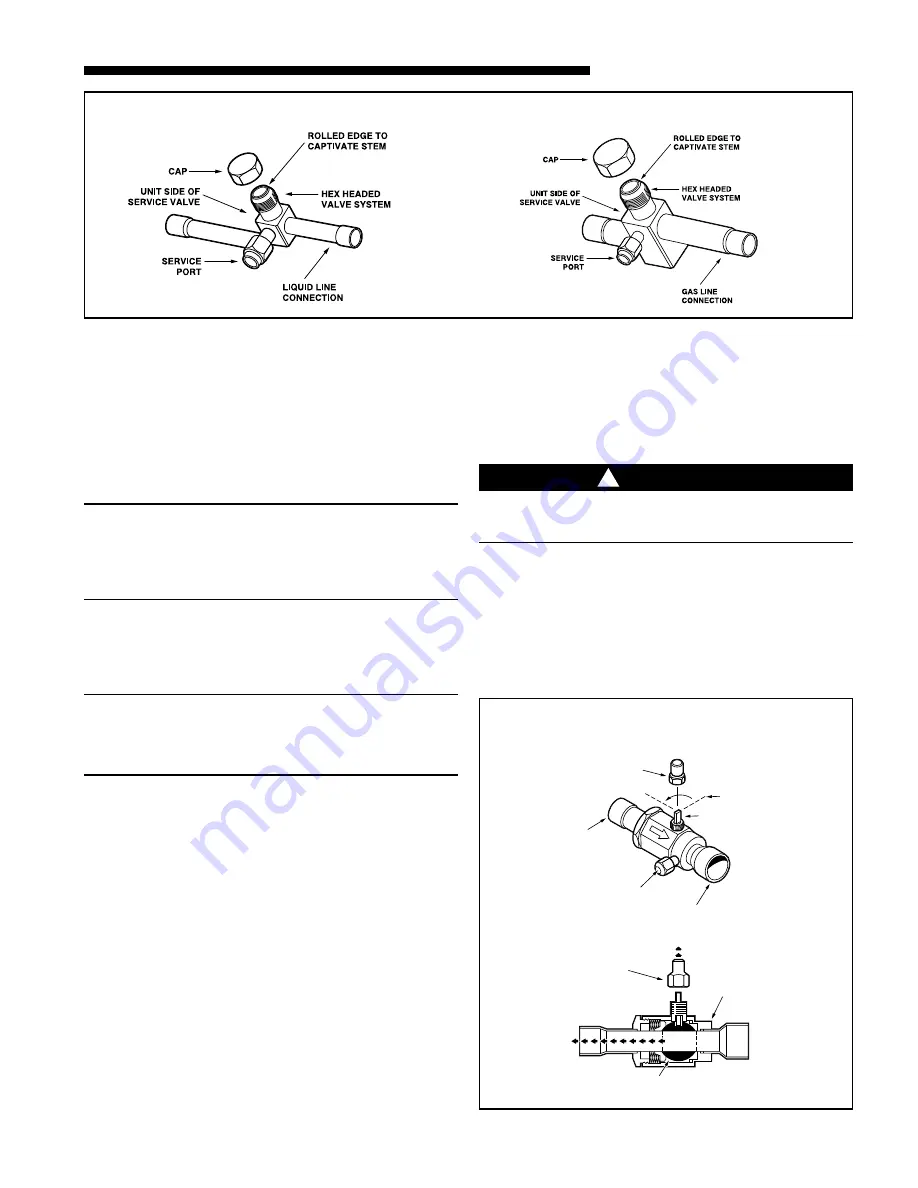
18-BC56D1-5
3
Installer’s Guide
lines with dry nitrogen to 150 psi. Use soap bubbles or other
leak-checking methods to see that all field joints are leak-
free! If not,
release pressure
; then repair!
SYSTEM EVACUATION
1. Upon completion of leak check, evacuate the refrigerant
lines and indoor coil before opening the gas and liquid
line valves.
2. Attach appropriate hoses from manifold gauge to gas
and liquid line pressure taps.
NOTE:
Unnecessary switching of hoses can be avoided and
complete evacuation of all lines leading to sealed system
can be accomplished with manifold center hose and
connecting branch hose to a cylinder of HCFC-22 and
vacuum pump.
3. The outdoor unit ships with a holding charge of dry
nitrogen. The nitrogen should be removed and the entire
system must be evacuated. Remove the refrigerant
connection seal caps and open the service gas and liquid
valves slowly to release the nitrogen from the unit.
NOTE:
A 3/16" Allen wrench is required to open liquid line service
valve. A 1/4" Open End or Adjustable wrench is required to
open gas line valve. A 3/4" Open End wrench is required to
take off the valve stem cap.
4. Attach center hose of manifold gauges to the vacuum
pump once the nitrogen pressure has been relieved.
5. Evacuate until the micron gauge reads no higher than
350 microns.
6. Close off valve to vacuum pump and observe the micron
gauge. If gauge pressure rises above 500 microns in one (1)
minute, then evacuation is incomplete or system has a leak.
7. If vacuum gauge does not rise above 500 microns in
one (1) minute, the evacuation should be complete.
8. With vacuum pump and micron gauge blanked off,
weigh in HCFC 22 refrigerant based on the outdoor
unit data plate and refrigerant line set length adjust-
ments noted on page 1 of the Service Facts.
9. Close valve on HCFC-22 supply cylinder when the
appropriate refrigerant charge has been achieved.
10. Replace gas and liquid service caps. These caps
MUST
BE REPLACED
to prevent leaks. Replace caps by
finger tightening, then tighten an additional 1/6 turn.
If refrigerant lines are longer than 15 feet and/or a
different size than recommended, it will be necessary to
adjust system refrigerant charge upon completion of
installation. See page 6 or in the unit Service Facts.
D. ELECTRICAL CONNECTIONS
WARNING
!
When installing or servicing this equipment, ALWAYS
exercise basic safety precautions to avoid the possibility of
electric shock.
1. Power wiring and grounding of equipment must comply
with local codes.
2. Power supply must agree with equipment nameplate.
3. Install a separate disconnect switch at the outdoor unit.
4. Ground the outdoor unit per local code requirements.
5. Provide flexible electrical conduit whenever vibration
transmission may create a noise problem within the
structure.
LIQUID LINE SERVICE VALVE
3
CAP
1/4 TURN ONLY
COUNTERCLOCKWISE
FOR FULL OPEN
POSITION
VALVE STEM
GAS LINE CONNECTION
UNIT SIDE
OF VALVE
CAP
BODY
COOLING
CORE
PRESSURE TAP PORT
GAS LINE BALL SERVICE VALVE
4
GAS LINE SERVICE VALVE