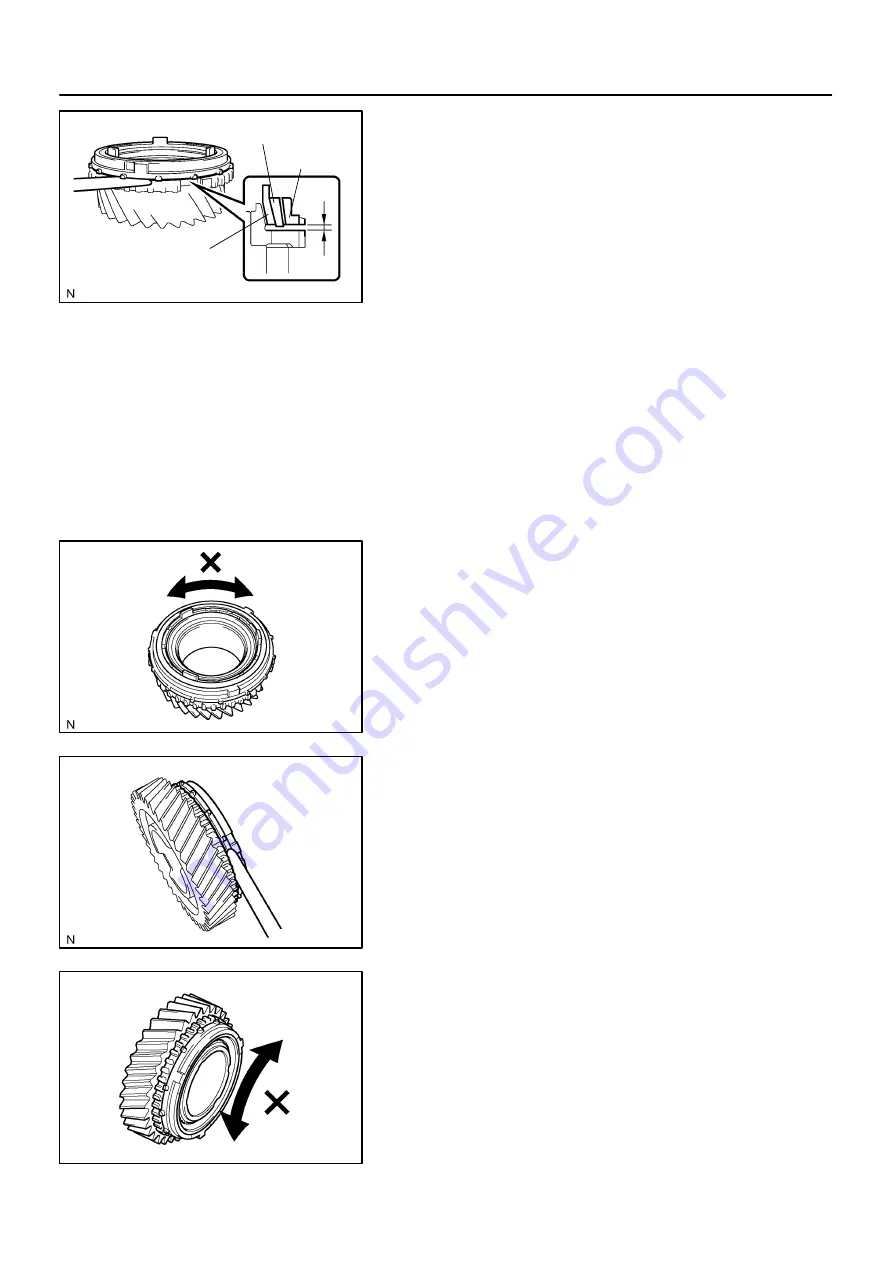
MT0HW−01
D13950
Inner
Middle
Outer
D13951
D13952
D13953
MT−34
−
MANUAL TRANSMISSION (RA60)
INPUT SHAFT
INSPECTION
1.
INSPECT SYNCHRONIZER RING SET NO.3
(a)
Using a feeler gauge, measure the clearance between
the synchronizer ring
set No.3 and the 3rd gear.
Standard clearance:
Inner: 1.20 to 2.20 mm (0.0472 to 0.0866 in.)
Middle: 0.60 to 1.80 mm (0.0236 to 0.0709 in.)
Outer: 0.80 to 1.80 mm (0.0315 to 0.0709 in.)
Minimum clearance:
Inner: 1.20 mm (0.0472 in.)
Middle: 0.60 mm (0.0236 in.)
Outer: 0.80 mm (0.0315 in.)
If the clearance is less than the minimum, replace the synchro-
nizer ring set No.3.
(b)
Coat the 3rd gear cone with gear oil. Check the braking
effect of the synchronizer ring. Turn the synchronizer ring
in one direction while pushing it against the 3rd gear cone.
Check that the ring locks.
2.
INSPECT SYNCHRONIZER RING NO.3
(a)
Using a feeler gauge, measure the clearance between
the synchronizer ring No.3 and the 4th gear.
Standard clearance:
0.70 to 1.50 mm (0.0276 to 0.0591 in.)
Minimum clearance:
0.70 mm (0.0276 in.)
If the clearance is less than the minimum, replace the synchro-
nizer ring No.3.
(b)
Coat the 4th gear cone with gear oil. Check the braking
effect of the synchronizer ring. Turn the synchronizer ring
in one direction while pushing it against the 4th gear cone.
Check that the ring locks.
Содержание 2006 Tundra
Страница 1: ......
Страница 2: ......
Страница 3: ......
Страница 56: ...PP0G5 02 PREPARATION MAINTENANCE PP 1 MAINTENANCE EQUIPMENT Mirror Brake hose Torque wrench ...
Страница 59: ...PP 4 PREPARATION ENGINE MECHANICAL 1GR FE 09951 07150 Handle 150 CYLINDER BLOCK CYLINDER HEAD ...
Страница 74: ...PP43J 01 PREPARATION SFI 1GR FE PP 19 RECOMMENDED TOOLS 09082 00050 TOYOTA Electrical Tester Set ...
Страница 75: ...PP43K 01 PP 20 PREPARATION SFI 1GR FE EQUIPMENT Graduated cylinder Transmission jack ...
Страница 86: ...PP43M 01 PREPARATION LUBRICATION 1GR FE PP 31 RECOMMENDED TOOLS 09200 00010 Engine Adjust Kit ...
Страница 87: ...PP43N 01 PP 32 PREPARATION LUBRICATION 1GR FE EQUIPMENT Oil pressure gauge Drain hose ...
Страница 96: ...PP43R 01 PREPARATION IGNITION 1GR FE PP 41 EQUIPMENT Spark plug cleaner Torque wrench ...
Страница 107: ...PP43E 01 PP 52 PREPARATION CHARGING 1GR FE EQUIPMENT Ammeter A Dial indicator with magnetic base Ohmmeter ...
Страница 112: ...PP0EO 04 PREPARATION CLUTCH PP 57 RECOMMENDED TOOLS 09031 00030 Pin Punch 09904 00010 Expander Set ...
Страница 113: ...PP0EP 02 PP 58 PREPARATION CLUTCH EQUIPMENT Vernier calipers Dial indicator ...
Страница 121: ...PP42P 01 PP 66 PREPARATION AUTOMATIC TRANSMISSION A750E A750F RECOMMENDED TOOLS 09082 00040 TOYOTA Electrical Tester ...
Страница 132: ...PP0EZ 03 PREPARATION PROPELLER SHAFT PP 77 EQUIPMENT Dial indicator Torque wrench ...
Страница 146: ...PP0FB 04 PREPARATION BRAKE PP 91 RECOMMENDED TOOLS 09082 00040 TOYOTA Electrical Tester 09905 00013 Snap Ring Pliers ...
Страница 148: ...PP0FD 02 PREPARATION BRAKE PP 93 LUBRICANT Item Capacity Classification Brake fluid SAE J1703 or FMVSS No 116 DOT 3 ...
Страница 160: ...PP06F 12 PREPARATION BODY ELECTRICAL PP 105 BODY ELECTRICAL SST Special Service Tools 09843 18020 Diagnosis Check Wire ...
Страница 166: ...PP0MW 03 PREPARATION BODY PP 111 LUBRICANT Item Capacity Classification MP grease ...
Страница 286: ...A21571 DIAGNOSTICS ENGINE 1GR FE DI 19 ...
Страница 287: ...A21572 DI 20 DIAGNOSTICS ENGINE 1GR FE ...
Страница 288: ...A21573 DIAGNOSTICS ENGINE 1GR FE DI 21 ...
Страница 289: ...A21575 DI 22 DIAGNOSTICS ENGINE 1GR FE ...
Страница 290: ...A21576 DIAGNOSTICS ENGINE 1GR FE DI 23 ...
Страница 566: ...cmc0490 BM E3 7 Battery J26 18 ETCS 2 1 Engine Room R B 1 2 2 4 B J27 DIAGNOSTICS ENGINE 1GR FE DI 293 WIRING DIAGRAM ...
Страница 613: ...DI 338 DIAGNOSTICS ENGINE 1GR FE NG Replace or replace harness or connector OK Replace ECM See page SF 66 ...
Страница 688: ... DIAGNOSTICS ENGINE 1GR FE DI 413 Check and repair harness or connector be tween EFI No 1 fuse and battery ...
Страница 711: ...A21571 DI 438 DIAGNOSTICS ENGINE 2UZ FE ...
Страница 712: ...A21572 DIAGNOSTICS ENGINE 2UZ FE DI 439 ...
Страница 713: ...A21573 DI 440 DIAGNOSTICS ENGINE 2UZ FE ...
Страница 714: ...A21575 DIAGNOSTICS ENGINE 2UZ FE DI 441 ...
Страница 715: ...A21576 DI 442 DIAGNOSTICS ENGINE 2UZ FE ...
Страница 830: ... DIAGNOSTICS ENGINE 2UZ FE DI 557 Replace ECM See page SF 82 ...
Страница 872: ... DIAGNOSTICS ENGINE 2UZ FE DI 599 END ...
Страница 1118: ... DIAGNOSTICS ENGINE 2UZ FE DI 833 NG Replace or replace harness or connector OK Replace ECM See page SF 82 ...
Страница 1248: ...A21571 DI 964 DIAGNOSTICS AUTOMATIC TRANSMISSION A750E for 1GR FE ...
Страница 1249: ...A21572 A22718 A22768 DIAGNOSTICS AUTOMATIC TRANSMISSION A750E for 1GR FE DI 965 ...
Страница 1250: ...A21573 DI 966 DIAGNOSTICS AUTOMATIC TRANSMISSION A750E for 1GR FE ...
Страница 1251: ...A21575 DIAGNOSTICS AUTOMATIC TRANSMISSION A750E for 1GR FE DI 967 ...
Страница 1252: ...A21576 DI 968 DIAGNOSTICS AUTOMATIC TRANSMISSION A750E for 1GR FE ...
Страница 1413: ...A21571 DIAGNOSTICS AUTOMATIC TRANSMISSION A750E A750F for 2UZ FE DI 1129 ...
Страница 1414: ...A21572 A22718 A22768 DI 1130 DIAGNOSTICS AUTOMATIC TRANSMISSION A750E A750F for 2UZ FE ...
Страница 1415: ...A21573 DIAGNOSTICS AUTOMATIC TRANSMISSION A750E A750F for 2UZ FE DI 1131 ...
Страница 1416: ...A21575 DI 1132 DIAGNOSTICS AUTOMATIC TRANSMISSION A750E A750F for 2UZ FE ...
Страница 1417: ...A21576 DIAGNOSTICS AUTOMATIC TRANSMISSION A750E A750F for 2UZ FE DI 1133 ...
Страница 1715: ...EM 12 ENGINE MECHANICAL 2UZ FE IDLE SPEED 4 Disconnect the tachometer from the DLC3 ...
Страница 1840: ...EC 10 EMISSION CONTROL 1GR FE EVAPORATIVE EMISSION EVAP CONTROL SYSTEM MEMO ...
Страница 1841: ... EMISSION CONTROL 1GR FE EVAPORATIVE EMISSION EVAP CONTROL SYSTEM EC 11 MEMO ...
Страница 1859: ... EMISSION CONTROL 2UZ FE EVAPORATIVE EMISSION EVAP CONTROL SYSTEM EC 13 MEMO ...
Страница 1860: ...EC 14 EMISSION CONTROL 2UZ FE EVAPORATIVE EMISSION EVAP CONTROL SYSTEM MEMO ...
Страница 1890: ...B17539 SF 16 SFI 1GR FE FUEL PUMP b Connect the sender gauge connector to the fuel suction plate No 1 ...
Страница 1941: ...SF1ZG 01 SFI 1GR FE ENGINE CONTROL MODULE ECM SF 67 INSPECTION INSPECT ECM See page DI 1 ...
Страница 1960: ...B17539 SF 18 SFI 2UZ FE FUEL PUMP b Connect the sender gage connector to the fuel suction plate No 1 ...
Страница 1981: ...SF0P1 12 B17463 MAF Meter Connector MAF Meter SFI 2UZ FE MASS AIR FLOW MAF METER SF 39 MASS AIR FLOW MAF METER COMPONENTS ...
Страница 2243: ... CLUTCH CLUTCH UNIT CL 19 6 INSTALL TRANSMISSION TO ENGINE See page MT 3 ...
Страница 2362: ...Q07290 TRANSFER TRANSFER ASSEMBLY TR 13 c Remove the planetary ring gear ...
Страница 2380: ...TR00L 07 F08802 Oil Seal Ring Input Shaft TRANSFER INPUT SHAFT TR 31 INPUT SHAFT COMPONENTS ...
Страница 2430: ...SA 16 SUSPENSION AND AXLE TIRE PRESSURE MONITOR VALVE 9 INSPECT TIRE PRESSURE WARNING SYSTEM See page DI 1287 SST 09843 18040 ...
Страница 2675: ...BR1X6 02 BRAKE STEERING ANGLE SENSOR BR 99 INSTALLATION Installation is in the reverse order of removal See page BR 97 ...
Страница 2726: ...F17910 SR 48 STEERING POWER STEERING VANE PUMP 1GR FE 4374 Author Date b Remove the 2 bolts and vane pump assembly ...
Страница 2835: ...RS12F 01 RS 68 SUPPLEMENTAL RESTRAINT SYSTEM SIDE AIRBAG ASSEMBLY Manual Adjuster Type 4483 Author Date DISPOSAL See page RS 53 ...
Страница 2975: ...I27167 M T Back up Light Switch A T Park neutral Position Switch BE 66 BODY ELECTRICAL BACK UP LIGHT SYSTEM 4623 Author Date ...
Страница 2991: ...BE2MD 01 I28305 A B BE 82 BODY ELECTRICAL COMBINATION METER 4639 Author Date CIRCUIT ...
Страница 3166: ...B17041 Double Cab Front Door Outside Moulding Rear Door Outside Moulding BO 52 BODY BODY OUTSIDE MOULDING 4823 Author Date ...
Страница 3218: ...BO4QC 02 BO 104 BODY SLIDING ROOF 4875 Author Date REASSEMBLY Reassembly is in the reverse order of disassembly see page BO 101 ...
Страница 3219: ...BO4QD 02 BODY SLIDING ROOF BO 105 4876 Author Date INSTALLATION Installation is in the reverse order of removal see page BO 100 ...
Страница 3333: ...BO4R6 02 BODY REAR SEAT LH BO 219 4990 Author Date REASSEMBLY Reassembly is in the reverse order of disassembly see page BO 214 ...
Страница 3334: ...BO4R7 02 BO 220 BODY REAR SEAT LH 4991 Author Date INSTALLATION Installation is in the reverse order of removal see page BO 213 ...
Страница 3341: ...BO4RB 03 BODY REAR SEAT RH BO 227 4998 Author Date REASSEMBLY Reassembly is in the reverse order of disassembly see page BO 223 ...
Страница 3342: ...BO4RC 03 BO 228 BODY REAR SEAT RH 4999 Author Date INSTALLATION Installation is in the reverse order of removal see page BO 222 ...
Страница 3429: ...AC0951 Stator AC 64 AIR CONDITIONING COMPRESSOR AND MAGNETIC CLUTCH 2UZ FE 5091 Author Date c Remove the stator ...
Страница 3475: ......
Страница 3477: ......
Страница 3486: ...INTRODUCTION F13890A IN 5 HOW TO USE THIS MANUAL 1 BODY PANEL REPLACEMENT THIS MANUAL ...
Страница 3487: ...INTRODUCTION IN 6 ...
Страница 3489: ...INTRODUCTION F13894A SYMBOLS MEANING ILLUSTRATION Assembly Mark BODY SEALER Flat Finishing BODY SEALER No flat Finishing IN 8 ...
Страница 3519: ...RADIATOR UPPER SUPPORT ASSY REMOVAL LH only RH only 2 2 10 BODY PANEL REPLACEMENT RE 2 ...
Страница 3521: ...RADIATOR SIDE SUPPORT ASSY REMOVAL With the radiator upper support removed 12 13 9 1 BODY PANEL REPLACEMENT RE 4 ...
Страница 3523: ...FRONT CROSSMEMBER ASSY REMOVAL 23 BODY PANEL REPLACEMENT RE 6 ...
Страница 3525: ...RADIATOR SUPPORT ASSY REMOVAL 12 1 1 1 BODY PANEL REPLACEMENT RE 8 ...
Страница 3527: ...COWL TOP SIDE PANEL ASSY REMOVAL 8 2 4 BODY PANEL REPLACEMENT RE 10 ...
Страница 3528: ... 8 2 4 BODY PANEL REPLACEMENT RE 11 INSTALLATION ...
Страница 3531: ...BODY PANEL REPLACEMENT RE 14 MEMO ...
Страница 3551: ...BACK PANEL ASSY Regular Cab REMOVAL 15 17 15 17 24 BODY PANEL REPLACEMENT RE 34 ...
Страница 3552: ...1 Temporarily install the new parts and check the fit of the back window glass BODY PANEL REPLACEMENT RE 35 INSTALLATION ...
Страница 3553: ...BACK PANEL ASSY Access Cab REMOVAL 67 25 BODY PANEL REPLACEMENT RE 36 ...
Страница 3555: ...BACK PANEL ASSY Access Cab REMOVAL 67 25 BODY PANEL REPLACEMENT RE 36 ...
Страница 3556: ...1 Temporarily install the new parts and check the fit of the back window glass BODY PANEL REPLACEMENT RE 37 INSTALLATION ...
Страница 3557: ...BACK PANEL ASSY Regular Cab REMOVAL 15 17 15 17 24 BODY PANEL REPLACEMENT RE 34 ...
Страница 3559: ...ROOF PANEL ASSY Regular Cab REMOVAL 9 9 16 2 2 20 BODY PANEL REPLACEMENT RE 38 ...
Страница 3561: ...ROOF PANEL ASSY Access Cab REMOVAL 16 16 16 2 2 20 BODY PANEL REPLACEMENT RE 40 ...
Страница 3566: ...Flat Surfacing Flat Surfacing Access Cab Regular Cab ANTI RUST TREATMENT Body Panel Sealing Areas AR 5 ...
Страница 3569: ...Flat Surfacing Flat Surfacing Flat Surfacing Flat Surfacing Flat Surfacing ANTI RUST TREATMENT Body Panel Sealing Areas AR 8 ...
Страница 3570: ...Flat Surfacing Flat Surfacing ANTI RUST TREATMENT Body Panel Sealing Areas AR 9 ...
Страница 3574: ...BODY PANEL REPLACEMENT F16919 F16919A REMOVAL BP 1 RADIATOR UPPER SUPPORT ASSY REPLACEMENT ...
Страница 3577: ...BODY PANEL REPLACEMENT F16921 F16921 REMOVAL BP 4 RADIATOR SIDE SUPPORT ASSY REPLACEMENT With the radiator upper support removed ...
Страница 3579: ...BODY PANEL REPLACEMENT F16923 F16923A REMOVAL BP 6 FRONT CROSSMEMBER ASSY REPLACEMENT ...
Страница 3581: ...BODY PANEL REPLACEMENT F16925 F16925A REMOVAL BP 8 RADIATOR SUPPORT ASSY REPLACEMENT ...
Страница 3585: ...BODY PANEL REPLACEMENT F16928 F16928A REMOVAL BP 12 COWL TOP SIDE PANEL ASSY REPLACEMENT ...
Страница 3588: ...BODY PANEL REPLACEMENT F16933 200 mm 7 87 in POINT 1 A is reuse PART NAME A Side Panel No 1 Retainer BP 15 ...
Страница 3591: ...BODY PANEL REPLACEMENT F16936 PART NAME J Antenna Pole Mounting Bracket RH Onry K Roof Drip Channel BP 18 ...
Страница 3592: ...BODY PANEL REPLACEMENT F16937 20 mm 0 79 in 30 mm 1 18 in 50 mm 1 97 in F16937A REMOVAL BP 19 CENTER BODY PILLAR CUT REPLACEMENT ...
Страница 3599: ...BODY PANEL REPLACEMENT F16940 20 mm 0 79 in F16940A REMOVAL BP 26 ROCKER PANEL CUT H REPLACEMENT ...
Страница 3601: ...BODY PANEL REPLACEMENT F16942 50 mm 1 97 in F16942A REMOVAL BP 28 ROCKER PANEL CUT REPLACEMENT ...
Страница 3603: ...BODY PANEL REPLACEMENT F16952 200 mm 7 87 in F16952A REMOVAL BP 30 QUARTER PANEL CUT REPLACEMENT ...
Страница 3607: ...BODY PANEL REPLACEMENT F16956 F16956A REMOVAL BP 34 BACK PANEL ASSY REPLACEMENT ...
Страница 3609: ...BODY PANEL REPLACEMENT F16958 F16958A REMOVAL BP 36 ROOF PANEL ASSY w o sun roof REPLACEMENT ...
Страница 3615: ...BODY PANEL REPLACEMENT F16902 23 0 N m 234 6 kgf cm 17 ft lbf BP 41 ...
Страница 3618: ...PAINT COATING F16905 2 INSIDE PC 2 ...
Страница 3619: ...F16906 3 OUTSIDE PAINT COATING PC 3 ...
Страница 3620: ...F15043 PAINT COATING PC 4 ...
Страница 3621: ...PAINT COATING F16908 4 DOOR PARTS PC 5 ...
Страница 3622: ...F16909 PAINT COATING PC 6 ...
Страница 3625: ...F16912 PAINT COATING PC 9 ...
Страница 3627: ...F16914 PAINT COATING PC 11 ...
Страница 3630: ...F16917 Anti Chip Film 1 W Over Fender 2 W O Over Fender PAINT COATING PC 14 ...
Страница 3678: ...2005 TOYOTA TUNDRA EWD611U 21 F Body Access Cab Standard Cab ...
Страница 3679: ...2005 TOYOTA TUNDRA EWD611U 22 F RELAY LOCATIONS Seat Access Cab Captain Seat ...
Страница 3680: ...2005 TOYOTA TUNDRA EWD611U 23 F 2 Engine Room R B Engine Compartment Left See Page 20 Access Cab Standard Cab ...
Страница 3682: ...2005 TOYOTA TUNDRA EWD611U 25 F ...
Страница 3684: ...2005 TOYOTA TUNDRA EWD611U 27 Memo ...
Страница 3686: ...2005 TOYOTA TUNDRA EWD611U 29 F ...
Страница 3688: ...2005 TOYOTA TUNDRA EWD611U 31 Memo ...
Страница 3689: ...2005 TOYOTA TUNDRA EWD611U 32 F RELAY LOCATIONS Engine Compartment Double Cab Instrument Panel Double Cab ...
Страница 3690: ...2005 TOYOTA TUNDRA EWD611U 33 F Body Double Cab Seat Double Cab Captain Seat ...
Страница 3692: ...2005 TOYOTA TUNDRA EWD611U 35 F ...
Страница 3694: ...2005 TOYOTA TUNDRA EWD611U 37 F ...
Страница 3695: ...2005 TOYOTA TUNDRA EWD611U 38 F RELAY LOCATIONS 2 Engine Room R B No 2 Engine Compartment Left See Page 32 Double Cab ...
Страница 3697: ...2005 TOYOTA TUNDRA EWD611U 40 F RELAY LOCATIONS Engine Room J B Engine Compartment Left See Page 32 Double Cab ...
Страница 3698: ...2005 TOYOTA TUNDRA EWD611U 41 F ...
Страница 3699: ...2005 TOYOTA TUNDRA EWD611U 42 F RELAY LOCATIONS Engine Room J B Inner Circuit Double Cab ...
Страница 3700: ...2005 TOYOTA TUNDRA EWD611U 43 Memo ...
Страница 3701: ...2005 TOYOTA TUNDRA EWD611U 44 F RELAY LOCATIONS Driver Side J B Lower Finish Panel See Page 32 Double Cab ...
Страница 3702: ...2005 TOYOTA TUNDRA EWD611U 45 F ...
Страница 3703: ...2005 TOYOTA TUNDRA EWD611U 46 F RELAY LOCATIONS Driver Side J B Inner Circuit Double Cab ...
Страница 3704: ...2005 TOYOTA TUNDRA EWD611U 47 F ...
Страница 3705: ...2005 TOYOTA TUNDRA EWD611U 48 F RELAY LOCATIONS Sub J B No 3 Upper the Accelerator Pedal See Page 32 Double Cab ...
Страница 3706: ...2005 TOYOTA TUNDRA EWD611U 49 F Sub J B No 3 Inner Circuit Double Cab ...
Страница 3707: ...2005 TOYOTA TUNDRA EWD611U 50 F RELAY LOCATIONS Sub J B No 4 Upper the Accelerator Pedal See Page 32 Double Cab ...
Страница 3708: ...2005 TOYOTA TUNDRA EWD611U 51 F Sub J B No 4 Inner Circuit Double Cab ...
Страница 3730: ...2005 TOYOTA TUNDRA EWD611U 73 Memo ...
Страница 3755: ...2005 TOYOTA TUNDRA EWD611U 98 G ELECTRICAL WIRING ROUTING Location of Connector Joining Wire Harness and Wire Harness Double Cab ...
Страница 3762: ...2005 TOYOTA TUNDRA EWD611U 105 Memo ...
Страница 3766: ...2005 TOYOTA TUNDRA EWD611U 109 Memo ...
Страница 3770: ...2005 TOYOTA TUNDRA EWD611U 113 Memo ...
Страница 3774: ...2005 TOYOTA TUNDRA EWD611U 117 Memo ...
Страница 3792: ...2005 TOYOTA TUNDRA EWD611U 135 Memo ...
Страница 3806: ...2005 TOYOTA TUNDRA EWD611U 149 Memo ...
Страница 3826: ...2005 TOYOTA TUNDRA EWD611U 169 Memo ...
Страница 3838: ...2005 TOYOTA TUNDRA EWD611U 181 Memo ...
Страница 3842: ...2005 TOYOTA TUNDRA EWD611U 185 Memo ...
Страница 3854: ...2005 TOYOTA TUNDRA EWD611U 197 Memo ...
Страница 3876: ...2005 TOYOTA TUNDRA EWD611U 219 Memo ...
Страница 3891: ...2005 TOYOTA TUNDRA EWD611U 234 Memo ...
Страница 3898: ...2005 TOYOTA TUNDRA EWD611U 241 Memo ...
Страница 3930: ...2005 TOYOTA TUNDRA EWD611U 273 Memo ...
Страница 3944: ...2005 TOYOTA TUNDRA EWD611U 287 Memo ...
Страница 3948: ...2005 TOYOTA TUNDRA EWD611U 291 Memo ...
Страница 3964: ...2005 TOYOTA TUNDRA EWD611U 307 Memo ...
Страница 3980: ...2005 TOYOTA TUNDRA EWD611U 323 Memo ...
Страница 3986: ...2005 TOYOTA TUNDRA EWD611U 329 Memo ...
Страница 4006: ...2005 TOYOTA TUNDRA EWD611U 349 Memo ...
Страница 4016: ...2005 TOYOTA TUNDRA EWD611U 359 Memo ...
Страница 4020: ...2005 TOYOTA TUNDRA EWD611U 363 Memo ...
Страница 4026: ...2005 TOYOTA TUNDRA EWD611U 369 Memo ...
Страница 4060: ...2005 TOYOTA TUNDRA EWD611U 403 Memo ...
Страница 4084: ...2005 TOYOTA TUNDRA EWD611U 427 Memo ...
Страница 4092: ...2005 TOYOTA TUNDRA EWD611U 435 Memo ...
Страница 4123: ...2005 TOYOTA TUNDRA EWD611U 466 Memo ...
Страница 4132: ...2005 TOYOTA TUNDRA EWD611U 475 Memo ...
Страница 4174: ...2005 TOYOTA TUNDRA EWD611U 517 Memo ...
Страница 4203: ...2005 TOYOTA TUNDRA EWD611U 546 J POWER SOURCE Current Flow Chart Access Cab Standard Cab ...
Страница 4204: ...2005 TOYOTA TUNDRA EWD611U 547 J ...
Страница 4210: ...2005 TOYOTA TUNDRA EWD611U 553 Memo ...
Страница 4211: ...2005 TOYOTA TUNDRA EWD611U 554 J POWER SOURCE Current Flow Chart Double Cab ...
Страница 4212: ...2005 TOYOTA TUNDRA EWD611U 555 J ...
Страница 4240: ...L Code Part Name Part Number Code Part Name Part Number 2005 TOYOTA TUNDRA EW611U 583 ...
Страница 4241: ...M OVERALL ELECTRICAL WIRING DIAGRAM 2005 TOYOTA TUNDRA EWD611U 584 ...
Страница 4389: ... 05 TUNDRA_U L O 0409 144 2005 TUNDRA from Sep 04 Prod OM34432U ...
Страница 4397: ... 05 TUNDRA_U L O 0409 152 2005 TUNDRA from Sep 04 Prod OM34432U ...
Страница 4409: ... 05 TUNDRA_U L O 0409 164 2005 TUNDRA from Sep 04 Prod OM34432U ...
Страница 4541: ... 05 TUNDRA_U L O 0409 296 2005 TUNDRA from Sep 04 Prod OM34432U ...
Страница 4583: ... 05 TUNDRA_U L O 0409 338 2005 TUNDRA from Sep 04 Prod OM34432U ...
Страница 4615: ... 05 TUNDRA_U L O 0409 370 2005 TUNDRA from Sep 04 Prod OM34432U ...
Страница 4729: ... 05 TUNDRA_U L O 0409 484 2005 TUNDRA from Sep 04 Prod OM34432U ...
Страница 4735: ... 05 TUNDRA_U L O 0409 490 2005 TUNDRA from Sep 04 Prod OM34432U ...
Страница 4809: ...DESTINATION INPUT AND ROUTE GUIDANCE 60 ...
Страница 4843: ...ADVANCED FUNCTIONS 94 ...
Страница 4893: ...AUDIO SYSTEM 144 ...
Страница 4898: ...v ...
Страница 4945: ...Notes 40 ...
Страница 4946: ...Notes 41 ...
Страница 4947: ...Notes 42 ...