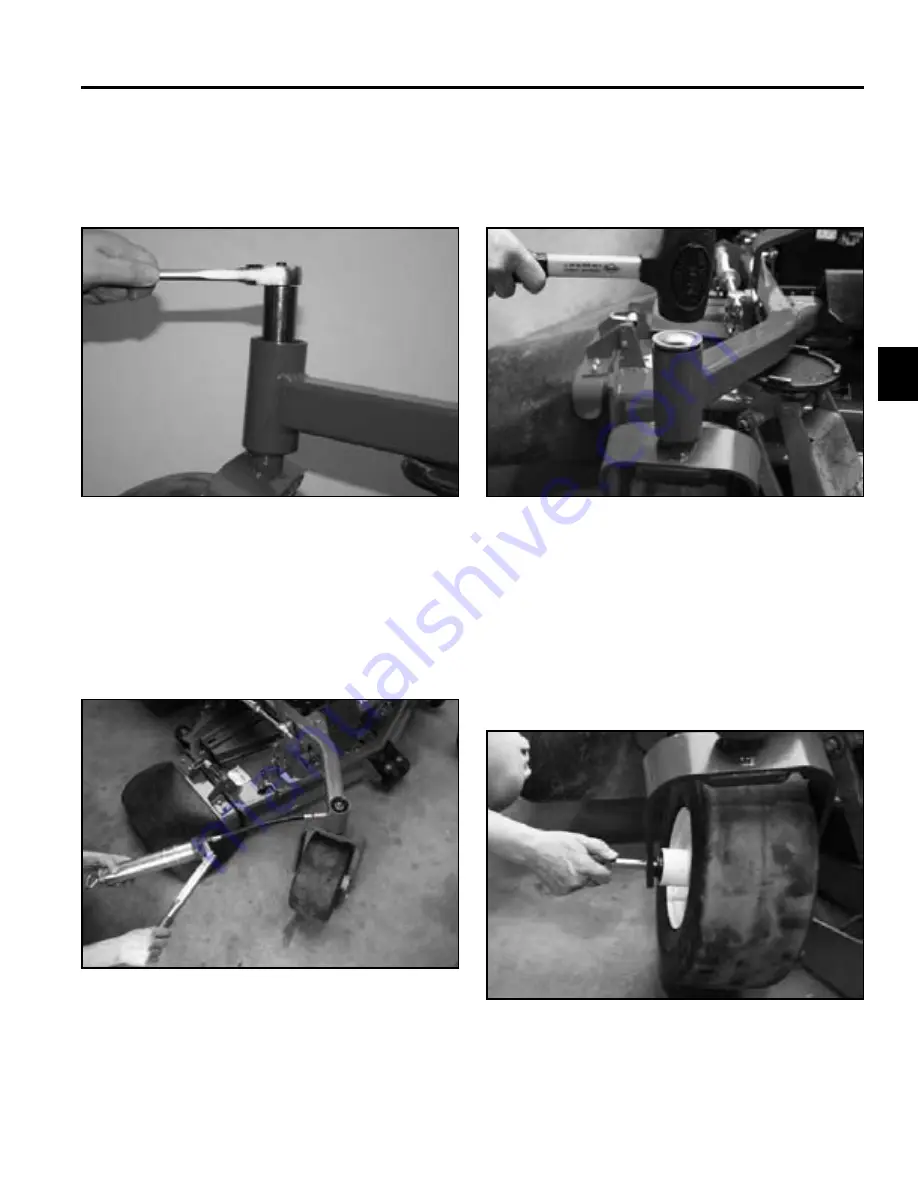
CHASSIS
3-5
Z580/Z593/Z595 Diesel Service Manual
3
3. Install the locknut. Tighten the locknut until the
Belleville washers are fl at, then back the nut off 1/4
turn to properly set the preload on the bearings (Fig.
016).
5. Remove the grease fi tting and install the grease
plug.
6. Install the dust cap onto the frame (Fig. 018).
Fig 016
IMG_7874a
Fig 018
IMG_7734
1. Raise the front of the machine off the ground.
2. Remove the wheel axle bolt and nut (Fig. 019).
4. Remove the plug located on the side of the castor
hub. Install a grease fi tting. Apply grease (No.
2 general purpose lithium base or molybdenum
grease) into the hub until it passes through the upper
bearing. Fill the top cavity with grease (Fig. 017).
Fig 019
IMG_7736
Fig 017
PICT-2897
Front Wheel Removal & Bearing
Replacement
Содержание Z580-D
Страница 1: ...LCE Products Z580 D Z593 D Z595 D Diesel Z Master Service Manual ...
Страница 3: ...THIS PAGE INTENTIONALLY LEFT BLANK ...
Страница 9: ...vi Z580 Z593 Z595 Diesel Service Manual TABLE OF CONTENTS THIS PAGE INTENTIONALLY LEFT BLANK ...
Страница 11: ...SAFETY INFORMATION 1 2 Z580 Z593 Z595 Diesel Service Manual 1 THIS PAGE INTENTIONALLY LEFT BLANK ...
Страница 87: ...CHASSIS 3 64 Z580 Z593 Z595 Diesel Service Manual 3 THIS PAGE INTENTIONALLY LEFT BLANK ...
Страница 309: ...MOWER DECKS 7 86 Z580 Z593 Z595 Diesel Service Manual 7 THIS PAGE INTENTIONALLY LEFT BLANK ...
Страница 310: ...Z580 D Z593 D Z595 D Diesel Z Master Service Manual Form No 492 9188 ...