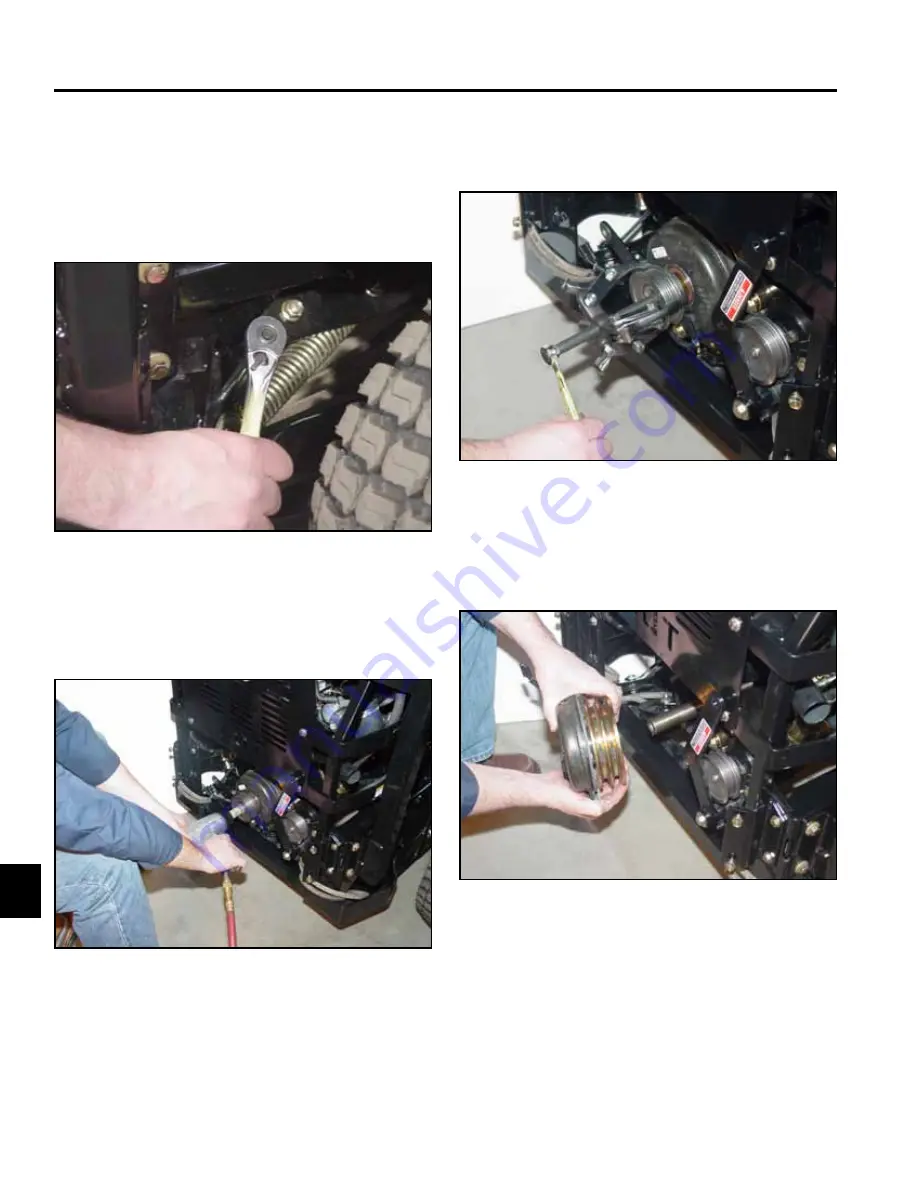
7-4
Z Master 597 Diesel Series Service Manual
7
9. On the right side of the unit is the spring loaded idler
pulley for the second mower drive belt. Insert a 3/8”
drive ratchet with a 6” extension into the square cut
hole in the idler bracket. Pull back on the ratchet to
relieve tension on the belt. Slip the belt off the idler
pulley and the PTO clutch (Fig. 395).
Fig 395
DSC-2607
10. Using an air impact wrench, loosen the center bolt
retaining the pulley and the PTO clutch (Fig. 396).
Fig 396
DSC-2613
Fig 398
DSC-2615
12. Remove the electric PTO clutch from the crankshaft
(Fig. 398).
Fig 397
DSC-2614
11. Use a wheel puller to remove the fan pump drive
pulley from the PTO clutch (Fig. 397).
MOWER DECKS
Содержание Z Master Z597
Страница 1: ...Z Master Z597 Diesel Series Service Manual LCE Products...
Страница 3: ...THIS PAGE INTENTIONALLY LEFT BLANK...
Страница 7: ...iv Z Master Z597 Diesel Service Manual THIS PAGE INTENTIONALLY LEFT BLANK TABLE OF CONTENTS...
Страница 87: ...4 34 Z Master Z597 Diesel Service Manual 4 HYDRAULIC SYSTEM HYDRAULIC DIAGRAM...
Страница 145: ...6 24 Z Master 597 Diesel Series Service Manual 6 ELECTRICAL...
Страница 146: ...6 25 Z Master 597 Diesel Series Service Manual 6 ELECTRICAL _ _...
Страница 147: ...6 26 Z Master 597 Diesel Series Service Manual 6 THIS PAGE INTENTIONALLY LEFT BLANK ELECTRICAL...
Страница 198: ...Z Master Z597 Diesel Series Service Manual Form No 492 9150...