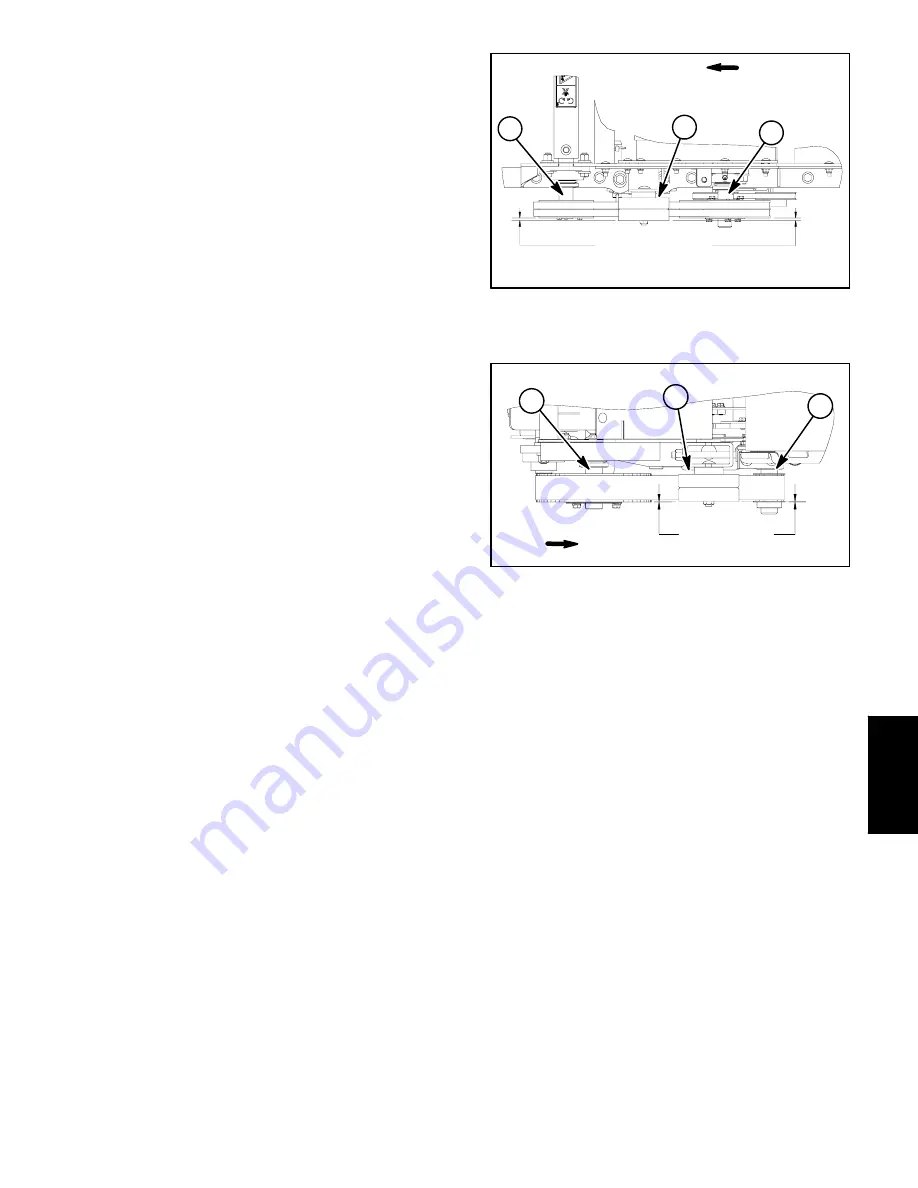
ProCore Processor
Page 6 -- 23
Chassis
7. Adjust drive belt idler pulleys to achieve proper ten-
sion on drive belts (see Operator’s Manual). After ad-
justment, make sure that chopper axle and brush shaft
are still properly aligned (Fig. 23).
IMPORTANT: After adjusting belt tension, check
that distance from idler pulley face to the faces of
the drive and driven pulleys is correct (Figs. 24 and
25). This distance is necessary to ensure that idler
pulley is correctly aligned to drive belts. If neces-
sary, re--adjust positions of drive and driven pulleys
to allow correct distance.
8. Install belt covers (see Drive Belt Covers in this sec-
tion).
9. Install rear cover to machine (see Rear Cover Instal-
lation in this section).
1. Jack shaft
2. Chopper axle
3. Idler pulley
Figure 24
0.250” (6.3 mm)
Idler Face to Sheave Face
1
2
3
FRONT
1. Brush shaft
2. Chopper axle
3. Idler pulley
Figure 25
0.050” (1.3 mm)
Idler Face to Sheave Face
UP
1
2
3
Chassis
Содержание ProCore
Страница 2: ...ProCore Processor This page is intentionally blank...
Страница 4: ...ProCore Processor This page is intentionally blank...
Страница 10: ...0 09375 ProCore Processor Page 2 2 Product Records and Maintenance Equivalents and Conversions...
Страница 44: ...ProCore Processor Hydraulic System Page 4 16 This page is intentionally blank...
Страница 93: ...ProCore Processor Page 6 17 Chassis This page is intentionally blank Chassis...
Страница 103: ...ProCore Processor Page 6 27 Chassis This page is intentionally blank Chassis...
Страница 107: ...ProCore Processor Page 6 31 Chassis This page is intentionally blank Chassis...
Страница 114: ...ProCore Processor Page 6 38 Chassis This page is intentionally blank...
Страница 116: ...ProCore Processor Electrical Diagrams Page 7 2 This page is intentionally blank...
Страница 120: ...Page 7 6 ProCore Processor Wire Harness Drawing...
Страница 122: ...Page 7 8 ProCore Processor Tow Hitch Kit Wire Harness BLACK BLUE BLACK BLUE BLACK BLUE BLACK BLUE BLACK BLUE...