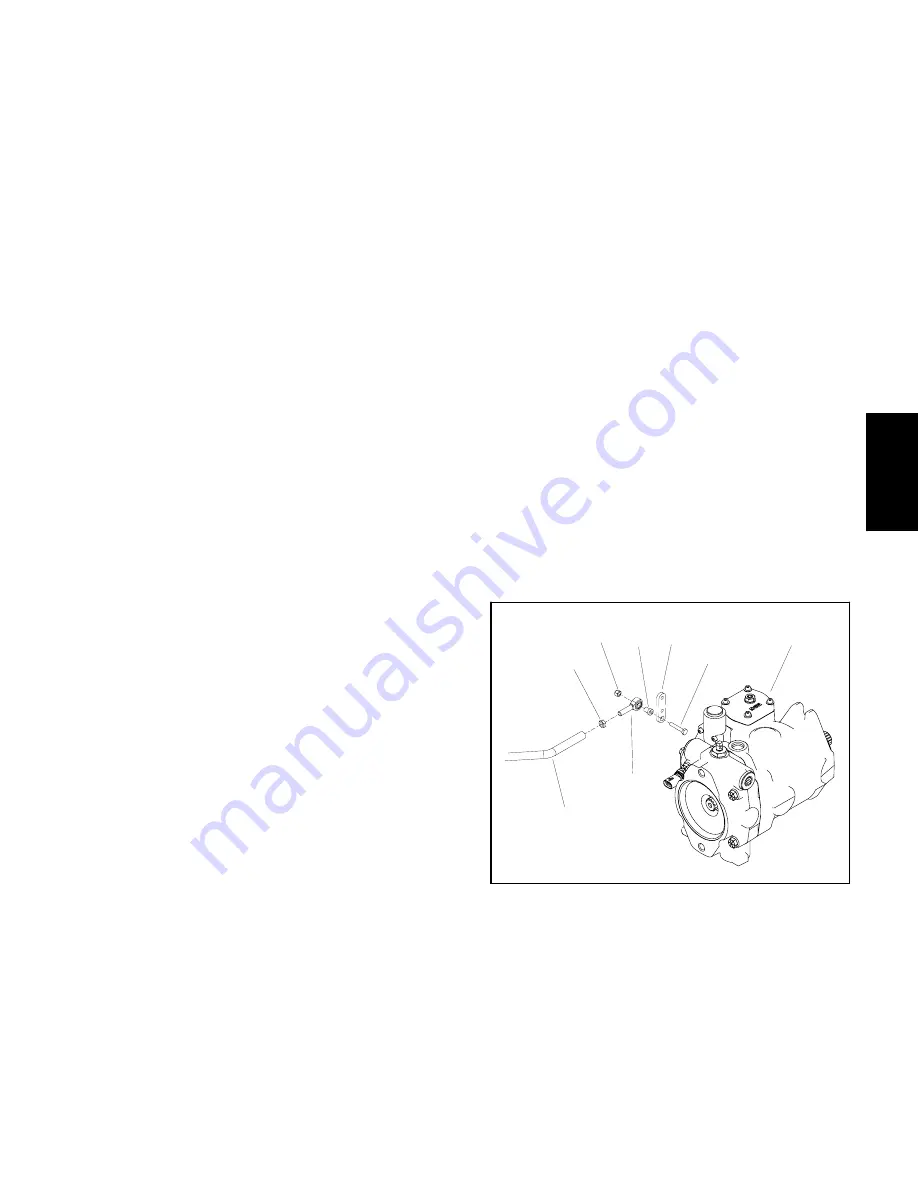
Groundsmaster 4000--D
Hydraulic System
Page 4 -- 75
Removal (Fig. 53)
1. Park machine on a level surface, lower cutting
decks, stop engine, apply parking brake and remove
key from the ignition switch.
2. To prevent contamination of hydraulic system during
removal, thoroughly clean exterior of pump assembly.
3. Remove traction rod from control arm on piston
pump by removing lock nut, spacer and cap screw (Fig.
54).
4. Disconnect wire harness connector from neutral
switch on piston pump.
5. Read the General Precautions for Removing and
Installing Hydraulic System Components at the begin-
ning of the Service and Repairs section of this chapter.
6. For installation purposes, label all hydraulic lines that
connect to gear pump and piston pump.
7. Put a drain pan below the pump assembly. Remove
hydraulic hoses and fittings connected to piston and
gear pumps. Put plugs or caps on disconnected hydrau-
lic hoses to prevent contamination of the system. Put
plugs in open ports of pumps.
NOTE:
If fuel tank is loosened and raised from the ma-
chine, the gear pump and piston pump can be removed
as a complete assembly.
8. Remove gear pump from machine (see Gear Pump
Removal in this section).
9. Support the piston pump to prevent it from falling
while removing two (2) cap screws and washers retain-
ing pump assembly to engine flywheel plate. Carefully
pull pump assembly from flywheel plate and raise it out
of the machine.
Installation (Fig. 53)
1. Carefully lower piston pump into the machine, align
pump input shaft to spring coupler on engine and posi-
tion it to the engine flywheel plate. Support pump to pre-
vent it from producing any side load into coupler and
also to align pilot diameter of pump to flywheel plate
bore.
2. While maintaining pump alignment with spring cou-
pler and flywheel plate, install two (2) cap screws and
washers to secure piston pump to engine flywheel plate.
Torque screws from
79 to 84 ft--lb (108 to 113 N--m)
.
3. Install gear pump to piston pump (see Gear Pump
Installation).
4. Position traction rod to control arm on piston pump
by installing cap screw, spacer and lock nut (Fig. 54).
5. Connect wire harness connector to neutral switch on
traction pump.
6. Remove plugs or caps from disconnected hydraulic
hoses and open ports of the pump assembly. Install fit-
tings and hoses to correct location on gear and piston
pumps (see Hydraulic Hose and Tube Installation in the
General Information section of this chapter).
7. Install new filter and fill hydraulic reservoir with cor-
rect oil.
8. Disconnect engine run solenoid electrical connector
to prevent engine from starting. Prime pumps by turning
ignition key switch to crank engine for 10 seconds. Re-
peat cranking procedure again.
9. Connect engine run solenoid electrical connector,
start the engine and check for proper operation.
10.Properly fill hydraulic system (see Charge Hydraulic
System in this section).
11.Stop engine and check for hydraulic oil leaks. Check
hydraulic reservoir oil level.
1. Piston pump
2. Cap screw
3. Pump control arm
4. Spacer
5. Lock nut
6. Jam nut
7. Traction rod
8. Rod end
Figure 54
1
2
4
5
6
3
7
8
Hydraulic System
Содержание Groundsmaster 4000-D
Страница 2: ...Groundsmaster 4000 D This page is intentionally blank ...
Страница 4: ...Groundsmaster 4000 D This page is intentionally blank ...
Страница 10: ...Groundsmaster 4000 D Page 1 6 Safety This page is intentionally blank ...
Страница 12: ...0 09375 Groundsmaster 4000 D Page 2 2 Product Records and Maintenance Equivalents and Conversions ...
Страница 34: ...Groundsmaster 4000 D Page 3 18 Kubota Diesel Engine This page is intentionally blank ...
Страница 43: ...Groundsmaster 4000 D Hydraulic System Page 4 9 This page is intentionally blank Hydraulic System ...
Страница 55: ...Groundsmaster 4000 D Hydraulic System Page 4 21 This page is intentionally blank Hydraulic System ...
Страница 107: ...Groundsmaster 4000 D Hydraulic System Page 4 73 This page is intentionally blank Hydraulic System ...
Страница 111: ...Groundsmaster 4000 D Hydraulic System Page 4 77 This page is intentionally blank Hydraulic System ...
Страница 117: ...Groundsmaster 4000 D Hydraulic System Page 4 83 This page is intentionally blank Hydraulic System ...
Страница 131: ...Groundsmaster 4000 D Hydraulic System Page 4 97 This page is intentionally blank Hydraulic System ...
Страница 145: ...Groundsmaster 4000 D Hydraulic System Page 4 111 This page is intentionally blank Hydraulic System ...
Страница 155: ...Groundsmaster 4000 D Hydraulic System Page 4 121 This page is intentionally blank Hydraulic System ...
Страница 161: ...Groundsmaster 4000 D Hydraulic System Page 4 127 This page is intentionally blank Hydraulic System ...
Страница 212: ...Groundsmaster 4000 D Page 5 38 Electrical System This page is intentionally blank ...
Страница 253: ...Groundsmaster 4000 D Page 7 11 Chassis This page is intentionally blank Chassis ...
Страница 264: ...Groundsmaster 4000 D Page 7 22 Chassis This page is intentionally blank ...
Страница 269: ...Groundsmaster 4000 D Cutting Decks Page 8 5 This page is intentionally blank Cutting Decks ...
Страница 282: ...Groundsmaster 4000 D Foldout Drawings Page 9 2 This page is intentionally blank ...
Страница 292: ...Page 9 12 Groundsmaster 4000 D Engine Wire Harness STARTER STARTER STARTER ...
Страница 294: ...Page 9 14 Groundsmaster 4000 D Front Wire Harness FLOW DIVIDER SOLENOID ...