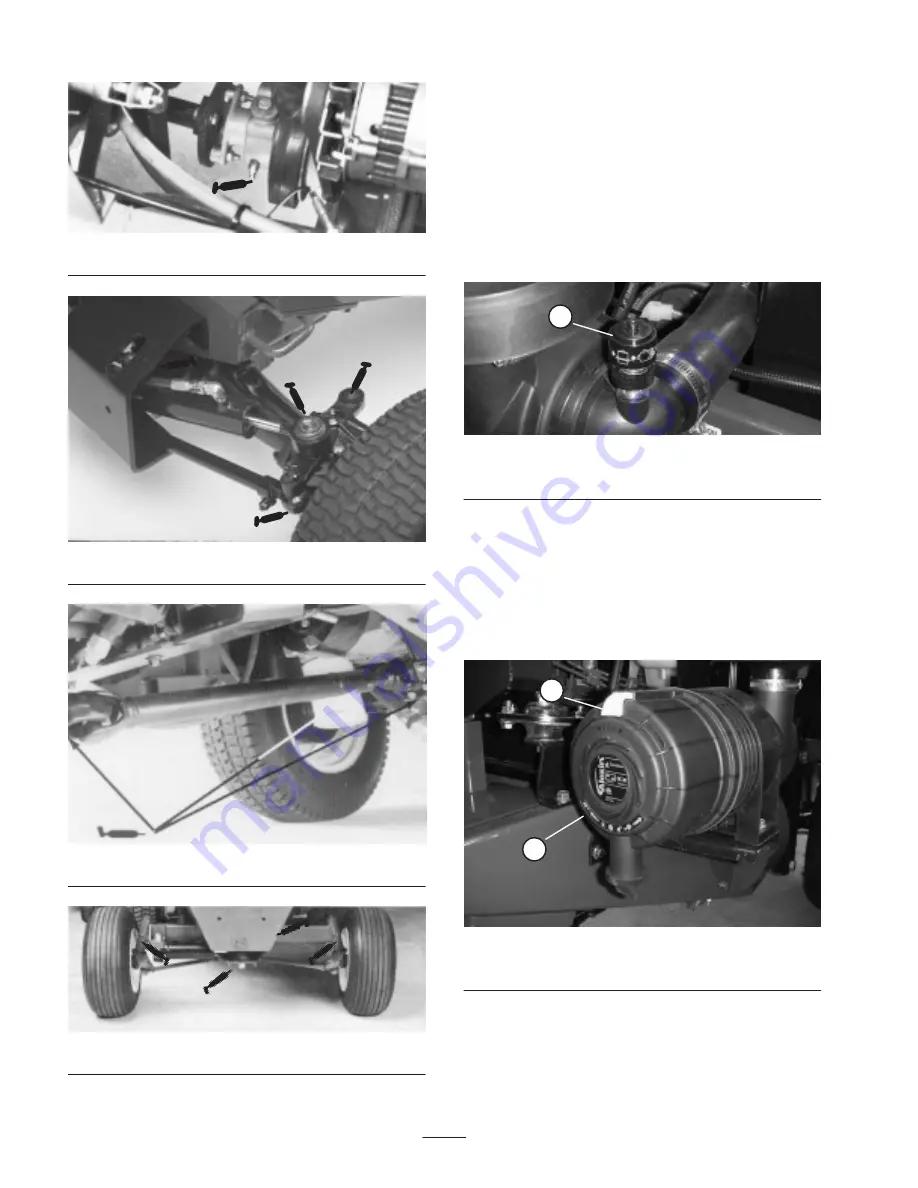
36
Figure 37
(2)
(2)
(4)
Figure 38
Figure 39
Figure 40
General Air Cleaner
Maintenance
•
Check air cleaner body for damage which could
possibly cause an air leak. Replace a damaged air
cleaner body.
•
Service the air cleaner filters when air cleaner indicator
(Fig. 41) shows red or every 400 hours (more frequently
in extreme dusty or dirty conditions). Do not over
service air filter.
1
Figure 41
1.
Air cleaner indicator
•
Be sure cover is sealing around air cleaner body.
Servicing Air Cleaner
1. Pull latch outward and rotate air cleaner cover
counter–clockwise. Remove cover from body (Fig. 42).
Clean inside of air cleaner cover.
2
1
Figure 42
2.
Air cleaner latch
3.
Air cleaner cover
2. Gently slide primary filter (Fig. 43) out of air cleaner
body to reduce the amount of dust dislodged. Avoid
knocking filter against air cleaner body.
Содержание Groundsmaster 328-D
Страница 55: ...55 ...