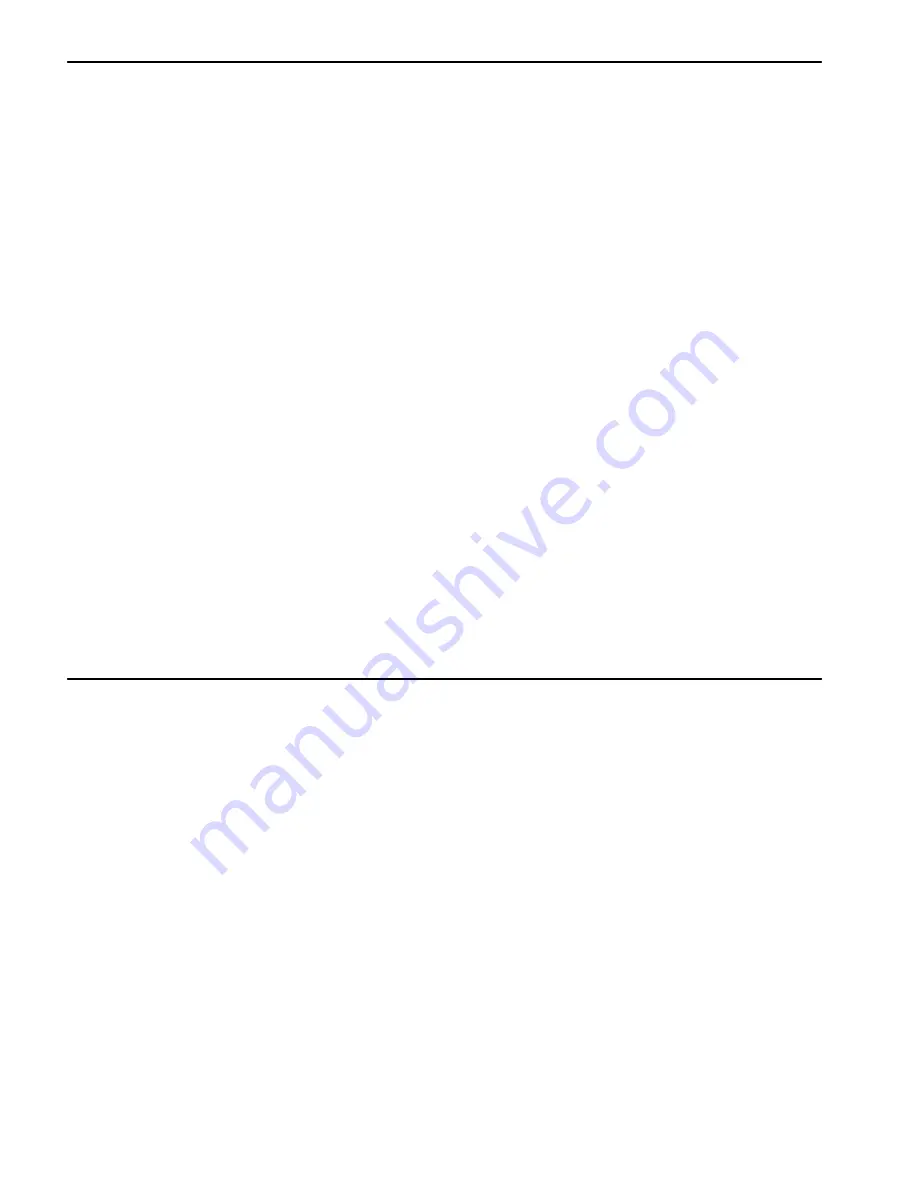
Greensmaster Flex 21
Page 1 – 2
Safety
While Operating
1. Do not run the engine in a confined area without ade-
quate ventilation. Exhaust fumes are hazardous and
could be deadly.
2. Always stand behind the handle when starting and
operating the machine.
3. To start and stop the engine:
A. Open fuel shut-off valve.
B. Verify that the control lever on handle is in NEU-
TRAL position for both traction and reel drives.
C. Move on/off switch to ON position, set choke to
full choke position (cold start) and throttle to half
throttle.
D. Pull starter cord to start engine.
E. Move throttle to SLOW and on/off switch to OFF
position to stop engine.
4. To transport mower from one area to another:
A. Install transport wheels.
B. Disengage reel drive.
C. Start engine.
D. Press down on handle to raise front of mower and
engage traction drive.
5. Before beginning mowing operation:
A. Disengage traction drive.
B. Stop engine.
C. Remove transport wheels.
D. Start engine.
E. Engage reel drive.
6. Before emptying basket of clippings, disengage trac-
tion drive, reduce engine speed and move on/off switch
to OFF position to stop engine.
7. Do not touch engine, muffler or exhaust pipe while
engine is running or soon after it has stopped because
these areas are hot enough to cause burns.
8. If the cutting unit strikes a solid object or vibrates ab-
normally, stop immediately, turn engine off,wait for all
motion to stop and inspect for damage. A damaged reel
or bedknife must be repaired or replaced before opera-
tion is commenced.
9. Whenever machine is left unattended, be sure en-
gine is stopped and cutting unit reel is not spinning.
Close fuel shut-off valve if machine is not to be used for
an extended period of time.
Maintenance and Service
1. Before servicing or making adjustments to the ma-
chine, stop the engine and pull the high tension lead off
spark plug to prevent accidental starting of the engine.
2. To make sure entire machine is in good condition,
keep all nuts, bolts, screws and belts properly tightened.
3. If major repairs are ever needed or assistance is re-
quired, contact an Authorized TORO Distributor.
4. To reduce potential fire hazard, keep the engine area
free of excessive grease, grass, leaves and accumula-
tion of dirt.
5. If the engine must be running to perform a mainte-
nance adjustment, keep hands, feet, clothing, and any
parts of the body away from the cutting unit and any
moving parts. Keep everyone away.
6. Do not overspeed the engine by changing governor
settings. Maximum engine speed is 3600 rpm. To en-
sure safety and accuracy, have an Authorized TORO
Distributor check maximum engine speed with a
tachometer.
7. Engine must be shut off before checking oil or adding
oil to the crankcase.
8. Engine must be shut off before checking or adding
fluid to the transmission.
9. To be sure of optimum performance and safety, al-
ways purchase genuine TORO replacement parts and
accessories. Replacement parts and accessories made
by other manufacturers could be dangerous. Such use
could void the product warranty of The Toro Company.
Содержание Greensmaster Flex 21
Страница 2: ...Greensmaster Flex 21 This page is intentionally blank...
Страница 4: ...Greensmaster Flex 21 This page is intentionally blank...
Страница 8: ...Greensmaster Flex 21 Page 1 4 Safety This page is intentionally blank...
Страница 10: ...Greensmaster Flex 21 Page 2 2 Product Records and Manuals Equivalents and Conversions...
Страница 72: ...Greensmaster Flex 21 Page 5 10 Electrical System This page is intentionally blank...
Страница 101: ...Greensmaster Flex 21 Page 7 17 Cutting Unit Rev C This page is intentionally blank Cutting Unit...
Страница 111: ...Greensmaster Flex 21 Page 7 27 Cutting Unit Rev C This page is intentionally blank Cutting Unit...
Страница 132: ...Greensmaster Flex 21 Groomer Model 04201 Rev B Page 8 16 This page is intentionally blank...