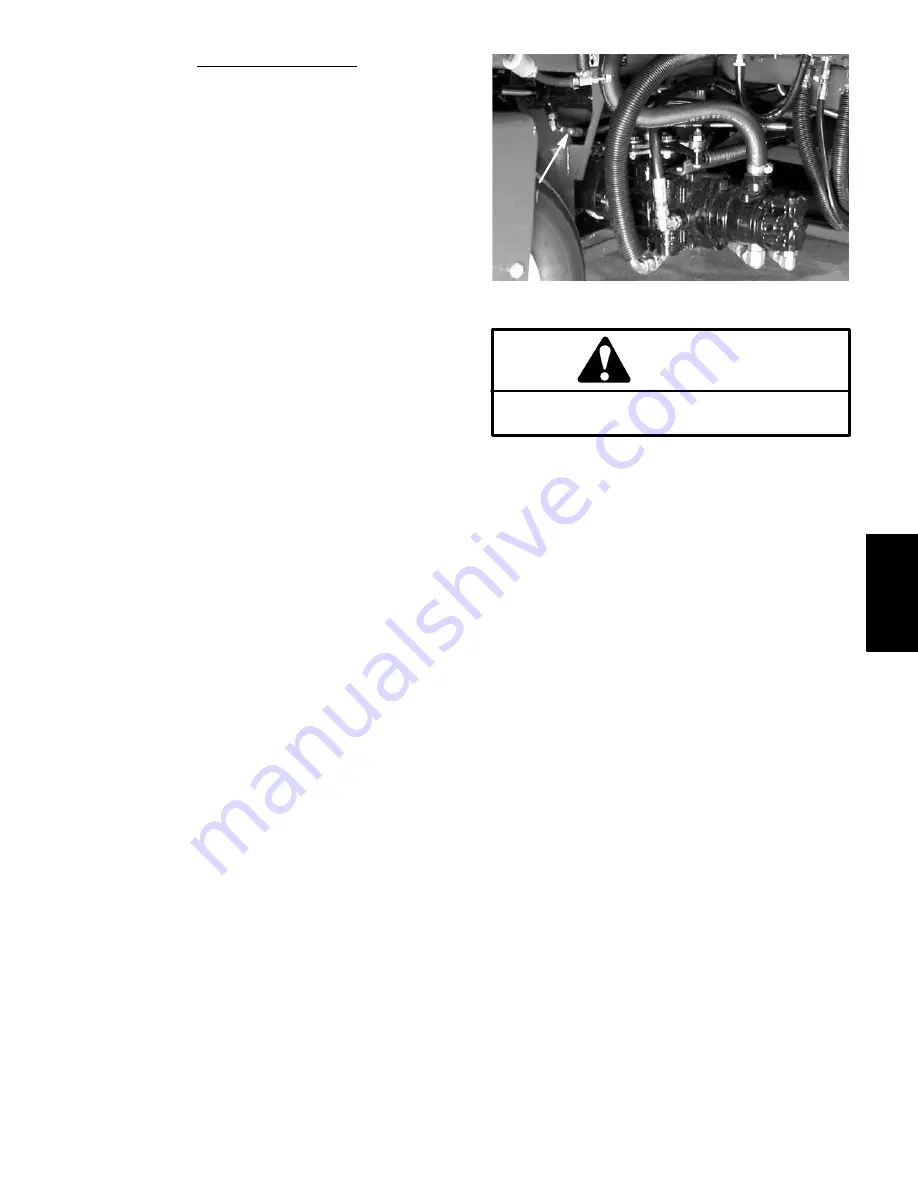
Procedure for Steering Control Valve Check:
1. Make sure the hydraulic tank is full.
2. Make sure hydraulic oil is at normal operating tem-
perature by operating the machine for approximately 10
minutes.
3. Drive machine slowly in a figure eight on a flat level
surface.
A. There should be no shaking or vibration in the
steering wheel or rear wheel.
B. Steering wheel movements should be followed
immediately
by a corresponding rear wheel move-
ment
without
the steering wheel continuing to turn.
4. Stop the unit with the engine running. Turn steering
wheel with small quick movements in both directions.
Let go of the steering wheel after each movement.
A. The steering wheel must go back immediately to
the neutral position.
B. The steering wheel should
not
continue to turn.
Note:
The steering wheel must be able to turn with no
more than
45 in–lb (5.1 Nm)
of torque.
5. Perform the Implement Relief Valve (R5) Pressure
and Gear Pump (P2) Flow tests to make sure that relief
valve and gear pump are functioning correctly.
Note:
This steering test procedure will be affected by
incorrect rear tire pressure, binding in the hydraulic
steering cylinder, extra weight on the vehicle, and/or
binding of the steering fork assembly. Make sure that
these items are checked before proceeding with any hy-
draulic testing procedure.
6. If either of these performance tests indicate a steer-
ing problem, determine if the steering cylinder is faulty
using the following procedure.
A. Park machine on a level surface with the cutting
units lowered and off. Make sure engine is off and the
parking brake is engaged.
B. Turn the steering wheel all the way to the left
(counterclockwise) so the steering cylinder rod is ful-
ly extended.
C. Turn engine off.
REMOVE
THIS HOSE
Figure 13
CAUTION
Before continuing further, read and become fa-
miliar with Precautions for Hydraulic Testing.
D. Read Precautions for Hydraulic Testing.
E. Remove hydraulic hose from the 90
o
fitting on the
rod end of the steering cylinder. Plug the end of the
hose.
F. With the engine off, continue turning the steering
wheel to the left (counterclockwise) with the steering
cylinder fully extended. Observe the open fitting on
the steering cylinder as the steering wheel is turned.
If oil comes out of the fitting while turning the steering
wheel to the left, the steering cylinder has internal
leakage and must be repaired or replaced.
G. Remove plug from the hydraulic hose. Recon-
nect hose to the steering cylinder fitting.
7. If steering problem exists and steering cylinder
tested acceptably, steering control valve requires ser-
vice (see Steering Control Valve and Steering Control
Valve Service).
Hydraulic System
Greensmaster 3150
Page 4 – 39
Hydraulic System
Содержание Greensmaster 3150
Страница 2: ...This page is intentionally blank Greensmaster 3150 ...
Страница 4: ...This page is intentionally blank Greensmaster 3150 ...
Страница 10: ...Equivalents and Conversions Product Records and Maintenance Page 2 2 Greensmaster 3150 ...
Страница 24: ...This page is intentionally blank Engine Page 3 8 Greensmaster 3150 ...
Страница 26: ...This page is intentionally blank Hydraulic System Page 4 2 Greensmaster 3150 ...
Страница 112: ...Rev C Greensmaster 3150 Hydraulic System Page 4 88 This page is intentionally blank ...
Страница 134: ...This page is intentionally blank Electrical System Page 5 22 Greensmaster 3150 ...
Страница 147: ...Greensmaster 3150 Page 7 3 ...
Страница 148: ......
Страница 149: ...Greensmaster 3150 Page 7 5 ...
Страница 150: ...Page 7 6 Greensmaster 3150 ...
Страница 151: ...Greensmaster 3150 Page 7 7 ...
Страница 152: ...Page 7 8 Greensmaster 3150 ...
Страница 153: ...Greensmaster 3150 Page 7 9 ...
Страница 154: ...Page 7 10 Greensmaster 3150 ...
Страница 155: ...Greensmaster 3150 Page 7 11 ...
Страница 156: ...Page 7 12 Greensmaster 3150 ...
Страница 157: ...Greensmaster 3150 Page 7 13 ...
Страница 158: ...Page 7 14 Greensmaster 3150 ...
Страница 159: ...Greensmaster 3150 Page 7 15 ...
Страница 160: ...Page 7 16 Greensmaster 3150 ...
Страница 161: ...Greensmaster 3150 Page 7 17 ...
Страница 163: ...Greensmaster 3150 Page 7 19 ...
Страница 164: ...Page 7 20 Greensmaster 3150 ...
Страница 166: ...Page 8 2 Greensmaster 3150 ...
Страница 168: ...Page 8 4 Greensmaster 3150 ...
Страница 169: ...Greensmaster 3150 Page 8 5 ...
Страница 170: ...Page 8 6 Greensmaster 3150 ...
Страница 171: ...Greensmaster 3150 Page 8 7 ...
Страница 172: ...Page 8 8 Greensmaster 3150 ...
Страница 173: ...Greensmaster 3150 Page 8 9 ...
Страница 174: ...Page 8 10 Greensmaster 3150 ...
Страница 175: ...Greensmaster 3150 Page 8 11 ...
Страница 176: ...Page 8 12 Greensmaster 3150 ...
Страница 177: ...Greensmaster 3150 Page 8 13 ...
Страница 178: ...Page 8 14 Greensmaster 3150 ...
Страница 179: ...Greensmaster 3150 Page 8 15 ...
Страница 180: ...Page 8 16 Greensmaster 3150 ...
Страница 181: ...Greensmaster 3150 Page 8 17 ...
Страница 182: ...Page 8 18 Greensmaster 3150 ...
Страница 183: ...Greensmaster 3150 Page 8 19 ...
Страница 184: ...Page 8 20 Greensmaster 3150 ...
Страница 185: ...Greensmaster 3150 Page 8 21 ...
Страница 186: ...Page 8 22 Greensmaster 3150 ...
Страница 188: ...Page 8 24 Greensmaster 3150 ...
Страница 189: ...Greensmaster 3150 Page 8 25 ...
Страница 190: ...Page 8 26 Greensmaster 3150 ...
Страница 192: ...Page 9 2 Greensmaster 3150 ...
Страница 194: ...Page 9 4 Greensmaster 3150 ...
Страница 195: ...Greensmaster 3150 Page 9 5 ...
Страница 196: ...Page 9 6 Greensmaster 3150 ...
Страница 197: ...Greensmaster 3150 Page 9 7 ...
Страница 198: ...Page 9 8 Greensmaster 3150 ...
Страница 199: ...Greensmaster 3150 Page 9 9 ...
Страница 200: ...Page 9 10 Greensmaster 3150 ...
Страница 201: ...Greensmaster 3150 Page 9 11 ...
Страница 202: ...Page 9 12 Greensmaster 3150 ...
Страница 203: ...Greensmaster 3150 Page 9 13 ...
Страница 204: ...Page 9 14 Greensmaster 3150 ...
Страница 205: ...Greensmaster 3150 Page 9 15 ...
Страница 206: ...Page 9 16 Greensmaster 3150 ...
Страница 207: ...Greensmaster 3150 Page 9 17 ...
Страница 208: ...Page 9 18 Greensmaster 3150 ...
Страница 209: ...Greensmaster 3150 Page 9 19 ...
Страница 210: ...Page 9 20 Greensmaster 3150 ...
Страница 211: ...Greensmaster 3150 Page 9 21 ...
Страница 212: ...Page 9 22 Greensmaster 3150 ...
Страница 213: ...Greensmaster 3150 Page 9 23 ...
Страница 214: ...Page 9 24 Greensmaster 3150 ...
Страница 216: ...Page 9 26 Greensmaster 3150 ...
Страница 217: ...Greensmaster 3150 Page 9 27 ...
Страница 218: ...Page 9 28 Greensmaster 3150 ...
Страница 219: ...Greensmaster 3150 Page 9 29 ...
Страница 220: ...Page 9 30 Greensmaster 3150 ...
Страница 221: ...Greensmaster 3150 Page 9 31 ...
Страница 222: ...Page 9 32 Greensmaster 3150 ...
Страница 223: ...Greensmaster 3150 Page 9 33 ...
Страница 224: ...This page is intentionally blank Repairs Page 9 34 Greensmaster 3150 ...
Страница 245: ...This page is intentionally blank Greensmaster 3150 Page 10 21 Rev A Dual Point Adjust Cutting Units Cutting Units ...
Страница 250: ...This page is intentionally blank Dual Point Adjust Cutting Units Page 10 26 Rev A Greensmaster 3150 ...
Страница 268: ...This page is intentionally blank Electrical Diagrams Page 11 2 Greensmaster 3150 ...
Страница 278: ...Page 11 12 Wiring Diagram Greensmaster 3150 ORIFICE S6 P19 Serial Number 230000801 Up Serial Number Under 230000801 ...