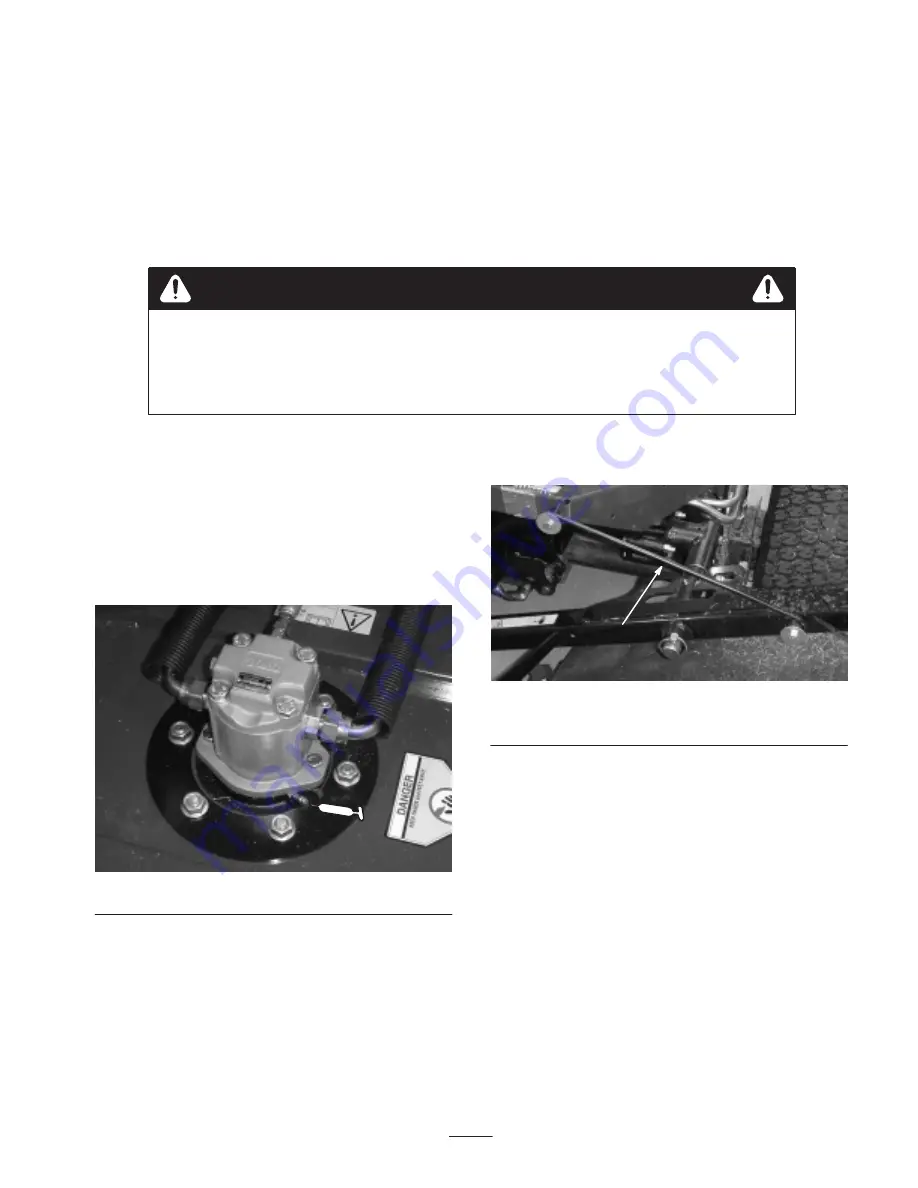
7
Check Condition of Deck
Make sure cutting chambers are in good condition.
Straighten any bends in chamber components to assure
correct blade tip/chamber clearance.
After Operating
To ensure optimum performance, clean underside of mower
housing. If residue is allowed to build up in mower
housing, cutting performance will decrease.
Maintenance
Note: Determine the left and right sides of the machine from the normal operating position.
Caution
If you leave the key in the ignition switch, someone could accidently start the engine and
seriously injure you or other bystanders.
Remove the key from the ignition and disconnect the wire from the spark plug before you do any
maintenance. Set the wire aside so that it does not accidentally contact the spark plug.
Greasing the Bearings
Each cutting deck has two grease fittings per spindle. Either
fitting can be used, which ever is more accessible. If
machine is operated under normal conditions, lubricate
blade spindle bearings (Fig. 6) with No. 2 general purpose
lithium base grease or molybdenum base grease, after every
50 hours of operation. Pump grease into fitting until a small
amount appears at bottom of spindle housing (under deck).
Figure 6
Cutting Deck Service Latch
When servicing cutting decks, use the service latch to
prevent injury.
1. Center cutting deck sidewinder with the traction unit.
2. Raise cutting decks to transport position.
3. Set parking brake and turn off machine.
4. Release latch rod (Fig. 7) from front carrier frame
retainer.
1
Figure 7
1.
Service latch hook
5. Lift outside of front cutting decks and place latch over
frame pin mounted on front of operators platform
(Fig. 7).
6. Sit on operator seat and start traction unit.
7. Lower cutting decks to mow position.
8. Turn off machine and remove key.
9. Reverse procedure to unlatch cutting decks.