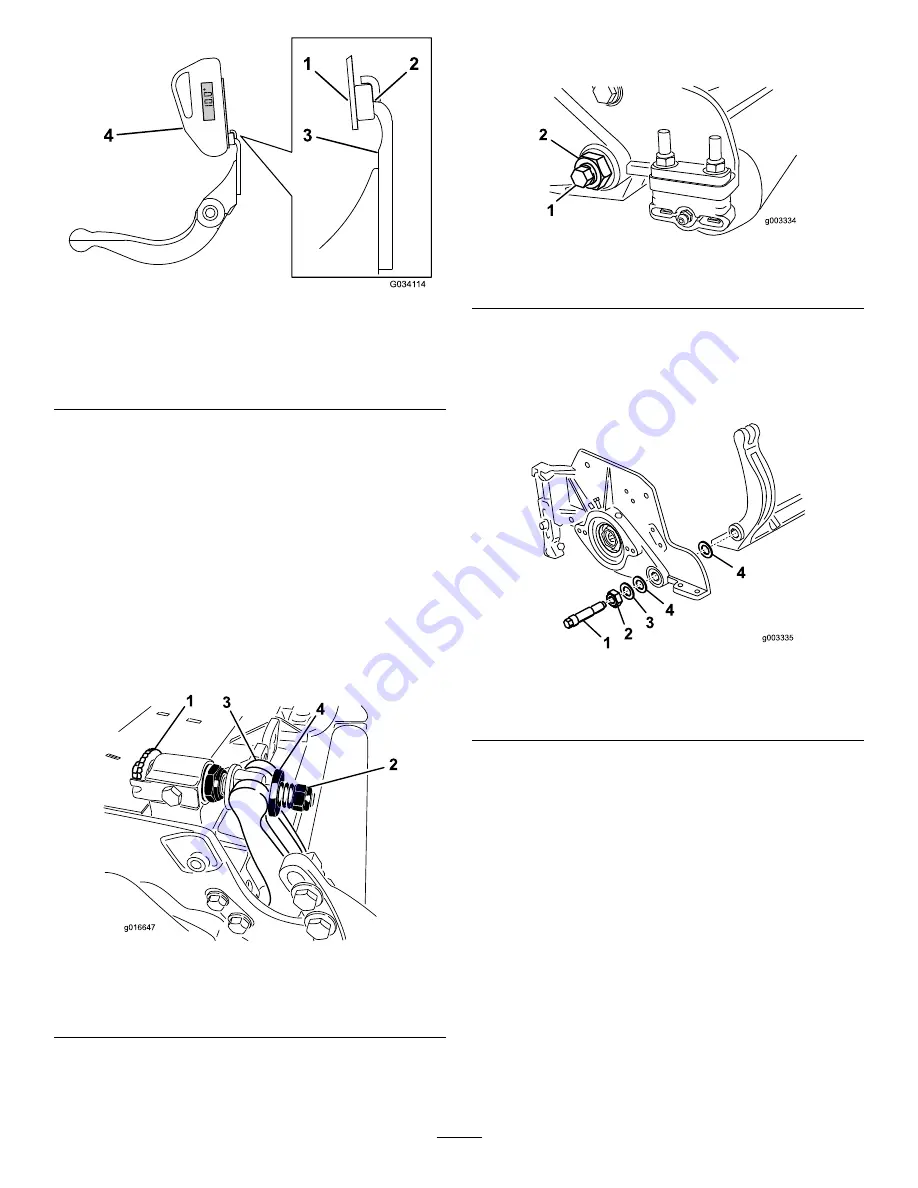
g034114
Figure 31
1.
Angle-indicator mount
3.
Bedknife
2.
Edge of the magnet mated
with the edge of the
bedknife
4.
Angle indicator
4.
Place the angle indicator on the mount as shown
in
Note:
This is the angle that your grinder
produces, and should be within 2° of the
recommended top grind angle.
Servicing the Bedbar
Removing the Bedbar
1.
Turn the bedbar-adjuster screws
counterclockwise to back the bedknife
away from the reel (
g016647
Figure 32
1.
Bedbar-adjusting screw
3.
Bedbar
2.
Spring-tension nut
4.
Washer
2.
Back out the spring-tension nut until the washer
is no longer tensioned against the bedbar
(
).
3.
On each side of the machine, loosen the locknut
securing the bedbar bolt (
g003334
Figure 33
1.
Bedbar bolt
2.
Locknut
4.
Remove each bedbar bolt, allowing the bedbar
to be pulled downward and removed from
machine bolt (
). Account for 2 nylon
washers and 1 stamped steel washer on each
end of the bedbar (
g003335
Figure 34
1.
Bedbar bolt
3.
Steel washer
2.
Nut
4.
Nylon washer
Assembling the Bedbar
1.
Install the bedbar, positioning the mounting ears
between the washer and the bedbar adjuster.
2.
Secure the bedbar to each side plate with the
bedbar bolts (nuts on bolts) and 6 washers.
3.
Position a nylon washer on each side of the
side-plate boss.
4.
Place a steel washer outside each of the nylon
washers (
).
Note:
Torque the bedbar bolts to 37 to 45 N∙m
(27 to 33 ft-lb). Tighten the locknuts until the
outside steel washer stops rotating and end play
is removed, but do not overtighten or deflect
the side plates. The washers on the inside may
have a gap.
21