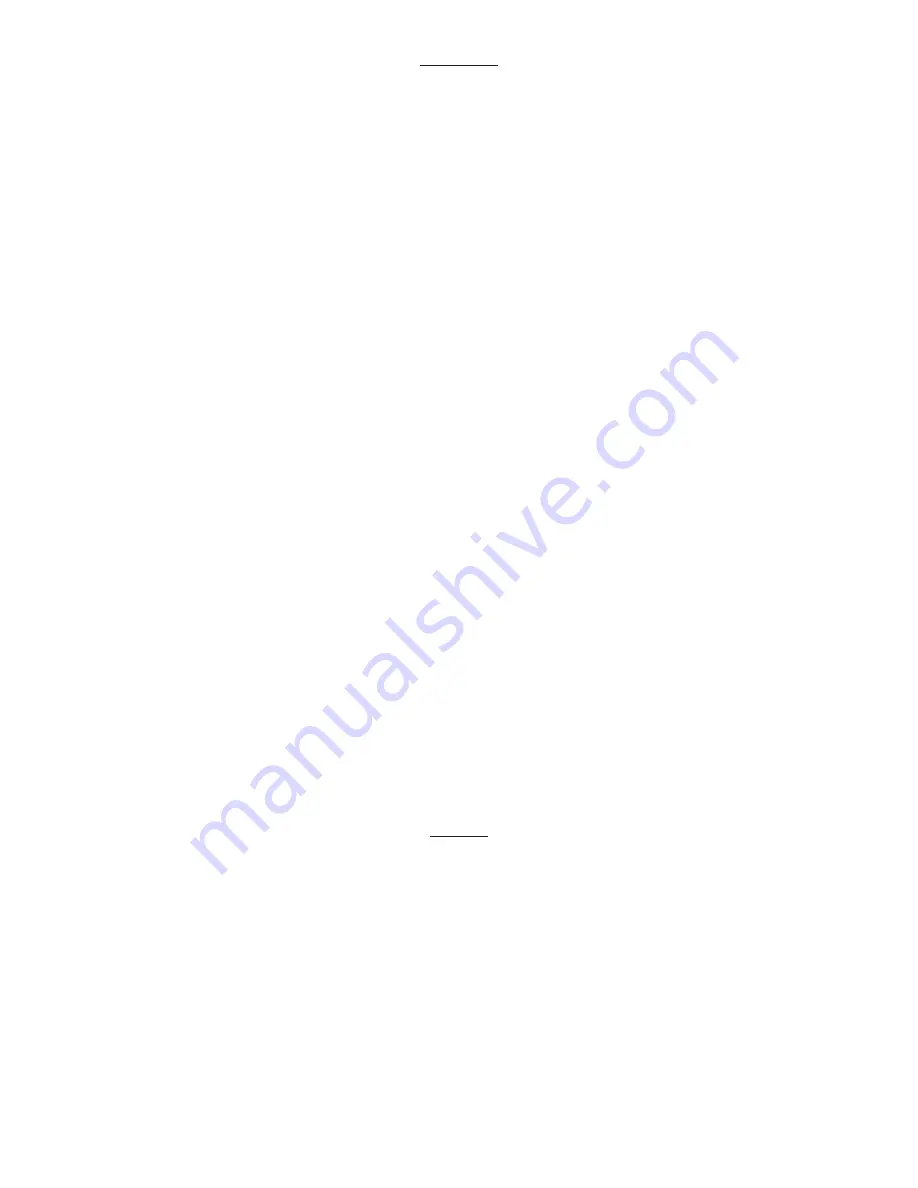
Disassemble
1. Disconnect tool from air supply and remove all wheels and accessories.
2. Secure the tool in vise vertically with angle head toward the upward direction. Clamp onto flats of the motor housing
(402-132[A][S][AS]).
3. Unscrew lock nut (406-38) with the use of a wrench. The angle head assembly will disconnect from motor housing. Set angle head
assembly aside for now. (Should the motor retainer (406-39) come off with the angle head assembly, then clamp the lock nut (406-38)
into a vise and remove motor retainer with motor retainer wrench (1100-350.)
4. Remove coupling (406-41), exhaust sleeve (410-G-17S), o-ring (400-51) and exhaust screen (402-134).
5. Unscrew and remove motor retainer (406-39). (Flats are provided for a wrench, or a special tool (1100-350) is available for easier
removal.)
6. Grasp motor assembly out of motor housing. Remove from vise.
The Motor Assembly
7. Remove snap ring (404-39) from rear of motor assembly with use of snap ring pliers.
8. Lift out bearing cover (404-38) and o-ring (594016).
9. Push snap ring (592016) out of spindle groove with use of snap ring pliers.
10. Install brass jaws onto vise. Secure the motor assembly vertically in the vise with the geared end toward the downward direction.
Clamp onto the outside diameter of cylinder (400-2G) and rear endplate (404-19).
11. Tap the spindle (406-14) out of rear bearing (404-9) with use of a 3/16” punch. Be sure not to drop the front motor assembly
when it becomes free. Remove from vise.
12. Push the rear bearing out of the read endplate with use of a small screwdriver.
13. Lift the rotor (400-5), blades (400-6), key (400-10) and front endplate (400-7) from the front motor assembly.
14. Remove retaining ring (400-46) from the motor spindle with use of snap ring pliers.
15. Support the front spindle assembly vertically on a suitable drill block. Press spindle through front bearing (400-G-11) with an
arbor press.
Angle Head Assembly
16. Secure right angle head assembly in vise so that the angle head neck is vertical. A head holder (1100-818) that fits against the
front face of the angle head is available.
17. Remove head retainer (406-40) using a wrench on the wrench flats.
18. Lift off lock nut. Remove angle head from vise.
19. Grasp end of pinion gear stem (406-112) and pull pinion gear assembly from angle head.
20. Secure the pinion gear assembly in vise vertically with gear head (406-110) in downward direction. Clamp onto the side of gear
spacer (406-42) and rear most bearing (300-G-29).
21. Tap the pinion gear stem through the rear bearing with use of a 3/16 inch punch. Remove from vise.
22. Secure the pinion gear stem with a wrench on the wrench flats.
23. Unscrew and remove the pinion gear head with use of a wrench on the wrench flats.
24. Support the pinion gear stem assembly vertically on a suitable drill block. Press the pinion gear stem off of bearing (300-G-29)
with use of arbor press.
25. Remove retaining ring (406-45) with use of snap ring pliers.
26. Grasp the output spindle (406-13) and pull assembly free from right angle head (406-1B).
27. Secure the output spindle assembly in a vise vertically with output toward downward direction. Clamp onto the flats of the spindle.
28. Remove screw (591046) from end of spindle assembly. Remove from vise.
29. Support the spindle assembly vertically on a suitable drill block. Press spindle through bearings (400-9) & (590031), spacer
(406-15), ring gear (406-110), and key (406-4).
To check the throttle valve, secure the motor housing horizontally in a vise. Clamp lightly onto the flats of the housing. Unscrew
and remove the throttle valve cap (869311). Lift out throttle valve spring (400-G-34) and throttle valve (400-G-29). Replace o-ring
(844302) if worn or torn.
Assembly
1. Be sure all parts are clean and free from abrasives before assembly.
The Motor Assembly
2. Support bearing (400-G-11) on a suitable drill block.
3.Press spindle (406-14A) through bearing until it bottoms on shoulder.
4. Place retaining ring (400-46) into groove in spindle.
5. Slide front endplate (400-7) over spindle and onto front bearing.
6. Place key (400-10) into keyway in spindle.
7. Slide rotor (400-5) over spindle.
8. Place 5 blades (400-6) into slots.
9. Slip cylinder (400-2G) over rotor. (be sure the alignment pin is oriented away from the front for the motor assembly.
10. Install rear endplate (404-19) locating cylinder pin in smaller hole of the rear endplate.
11. Place bearing (404-9) in rear endplate. Tap in place with bearing driver (1100-806).
12. Place snap ring (592016) in spindle groove.
13. Place o-ring (594016), bearing cover (404-38) and snap ring (404-39) into rear of end plate.
14. Secure case (402-132[A][S][AS]) in vise vertically. Slip motor assembly into case.
15. Install o-ring (400-51), exhaust screen (402-134), and exhaust deflector (410-G-17S).
16. Screw motor retainer (406-39) into case and tighten. (Flats are provided for a wrench, or a special tool (1100-350) is available
for easier tightening.)
Содержание 46BRA1
Страница 4: ...Maintenance...