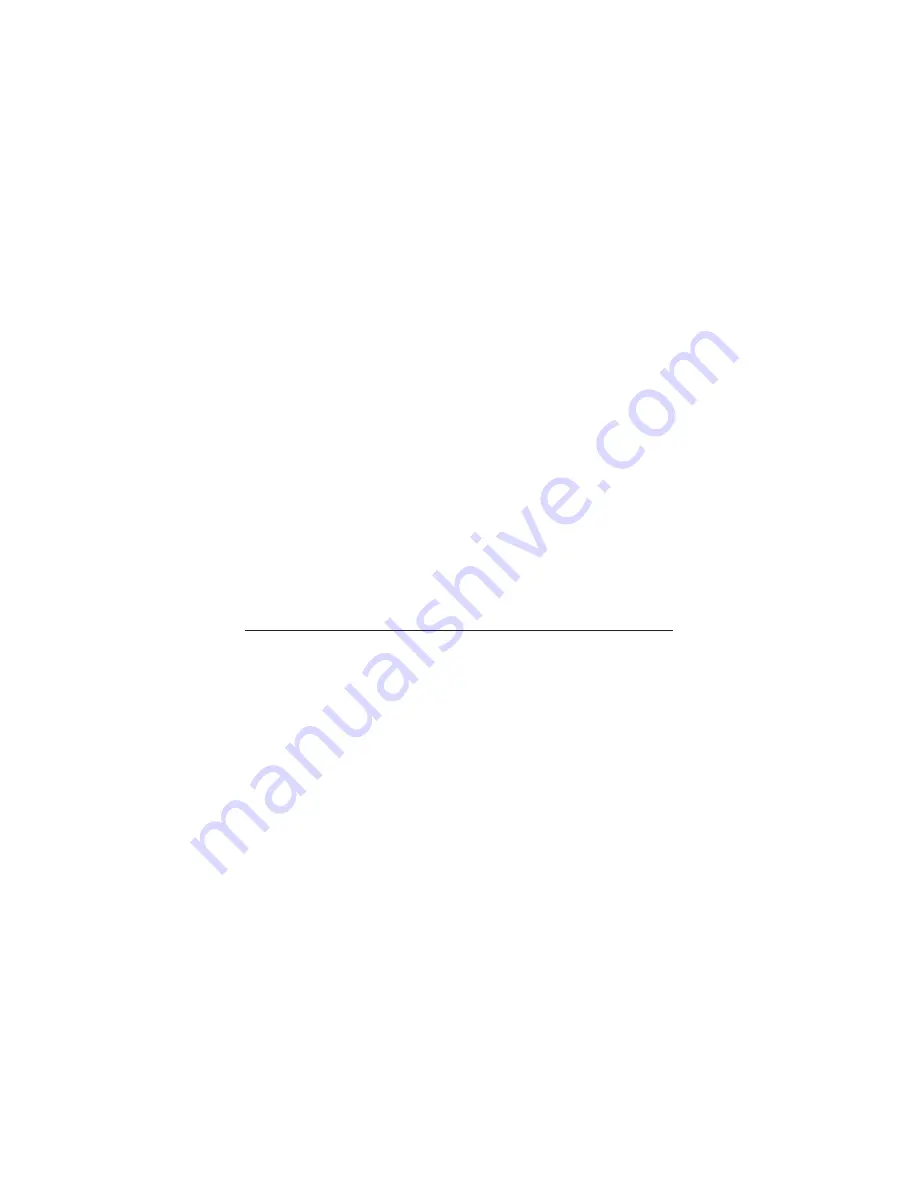
Lubricators
Lubricators are devices that induce a controlled amount of oil into the air supply for pneumatically
driven tools. They generally contain a reservoir that one must keep filled with oil. A light grade oil
such as Mobil DTE light or equivalent is recommended. There is a variable setting on the lubricator
that will determine the amount of oil induced into the air supply. It is important to inspect both the
setting and amount of oil in the lubricator regularly to determine proper functioning of the device. The
lack of oil in the air system will greatly reduce the performance and longevity of the pneumatically
driven tool.
2) Direct injection of oil into the tool
A simple and easy way to ensure proper lubrication is to inject the oil directly into the tool air inlet.
This should be performed prior to storage of the tool. To perform this task one must have a small
container of the proper lubricating oil.
● Disconnect the tool from the air supply at the air coupling.
● Place a few drops of oil from the container into the air inlet of the tool directly.
● Reconnect the tool to the air supply.
● Direct the exhaust of the tool away from any bystanders or cover the exhaust with a shop rag.
● Run the tool until the oil has completely passed through the unit.
The best lubrication techniques include both methods.
Geared Tools
Tools equipped with gear systems require occasional greasing in order to maintain efficiency and
promote longevity of the geared components. Zirc grease fittings are installed on geared tools to
make for ease of this process. We recommend a NLGI-2 type of grease for use with all of our
geared tools.
What Conditions Indicate the Need for Maintenance?.
Pneumatic tools will exhibit several distinct signs that maintenance is required. Higher costs can
be avoided if maintenance is performed when the first signs are evident. The following list details
conditions that may indicate the necessity for service.
1) With the tool disconnected from the air supply, grasp the spindle and spin in the direction of
operation. The spindle should spin freely with no resistance.
2) With the tool disconnected from the air supply, grasp the spindle by hand. Attempt to move the
spindle from side to side and back and forth. Excess play can be a sign that service is required.
3) A reduction in power may indicate the necessity for maintenance.
4) Should the tool not maintain a uniform operating speed, servicing may be required.
For More Information
1) General Industry Safety & Health Regulations 29 CFR, Part 1910 and where applicable Construc-
tion Industry Safety & Health Regulations 29 CFR, Part 1926 available from Superintendent of
Documents, Gov’t. Printing Office, Washington, D.C. 20402.
2) Safety Code For Portable Air Tools, ANSI B186.1, B7.1 and Z87.1, available from American
National Standards Institute, Inc. 1430 Broadway, New York, NY 10018
© Copyright 2007
All Rights Reserved
Содержание 46BRA1
Страница 4: ...Maintenance...