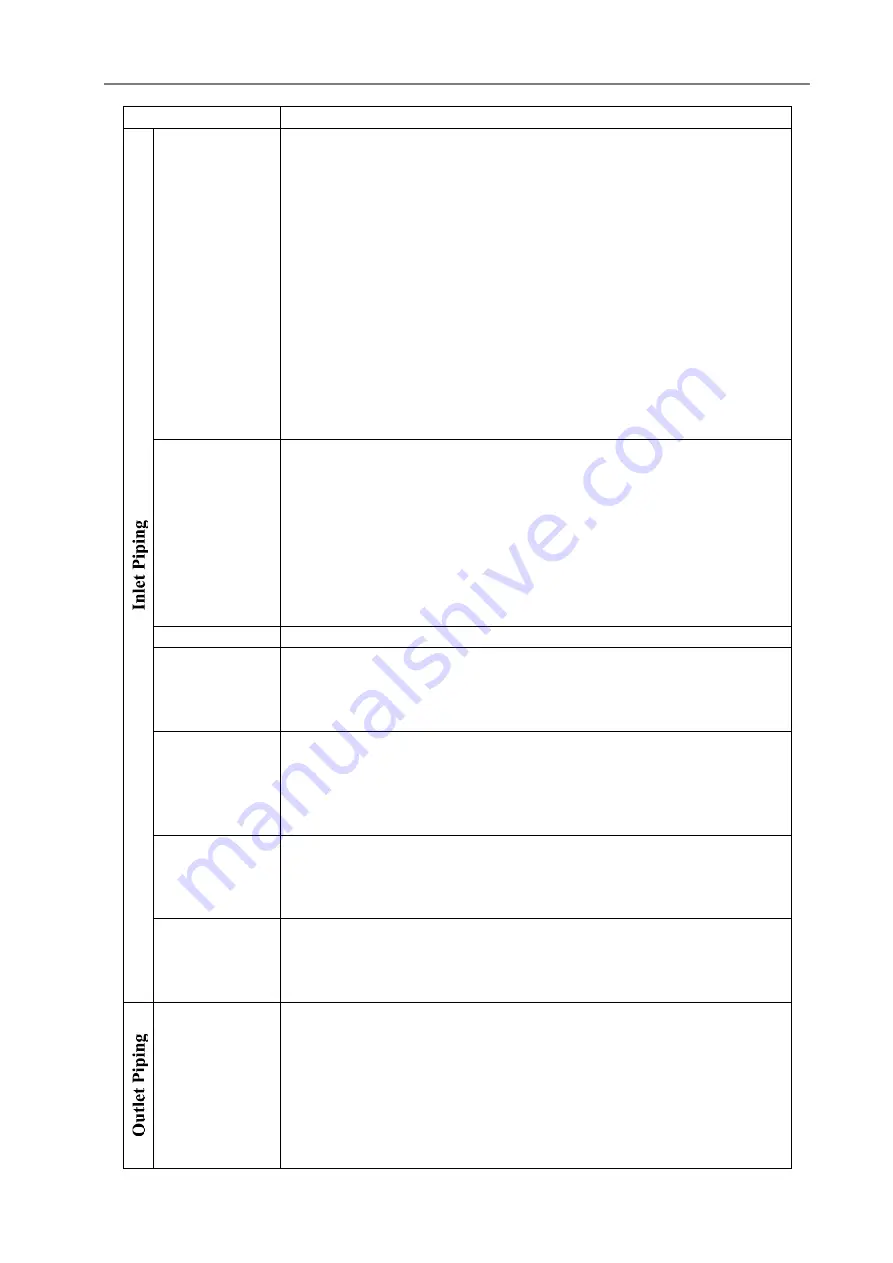
6
Procedure
Items to Note
General
Requirements
1. Suction condition must satisfy NPSHa>NPSHr+0.5m
2. Reduce inlet Head as much as possible. Use straight and short
piping.
3. The pipes should have adequate structural support and shouldn’t
use the pump as its primary support. (see Fig. 4.1)
4. When designing supports, consider the effects of temperature
changes on the supports to avoid thermal stress.
5. Inlet piping and connectors should be installed properly to prevent
sucking in air.
6. The piping system should not have upward bumps that may collect
air. The inlet piping should also have a 0.01~0.02 slope increase
towards the pump. (see Fig. 4.2)
7. There should not be any elbows for at least 5 times the pipe
diameter from the opening of the pump. The elbow closest to the
pump opening should be a long radial elbow.
Inlet Piping
1. There should be at least a 1.5 diameter distance between the pipe
inlet and the closest tank wall to prevent circulation. (see Fig. 4.4)
2. The submerge depth of the inlet should be at least 0.5m or at least
twice the pipe diameter below the liquid surface. (see Fig. 4.4)
3. There should be a distance of at least 1.5D between the bottom of
the tank and the beginning of the inlet pipe opening. (see Fig. 4.4)
4. If there are two or more inlet piping in the same tank, they should
be placed at least 3D apart to prevent mutually disrupting each
other’s flow.
Foot Valve
Please install a foot valve if upward suction is used. (see Fig. 4.1)
Self-Priming
Cylinder
1. If suction method is upward suction, please install a self-priming
cylinder to prevent dry-running due to a leaking foot-valve.
2. The size of the self-priming cylinder should have a minimum liquid
level of at least 0.5m above the opening of the pump.
Control Valve
1. A control valve should be installed to make disassembling of the
pump easier. The valve should only be shut off when the pump is to
be detached for maintenance or repairs.
2. We recommend the use of valves that have the least loss when fully
opened, like a gate valve.
Filter
1. It is generally not recommended to install a filter in front of a
pump, which can unpredictably increase suction system resistance.
2. If a filter has to be used, it should be cleaned regularly to ensure a
smooth flow.
Vacuum Gauge
1. The material used should be corrosion resistant, otherwise, a
pressure gauge diaphragm should be used.
2. During operation, if the vacuum gauge reading fluctuates, either
there are air bubbles in the system or cavitation has occurred.
General
Requirements
1. The weight of the outlet piping should be properly supported to
prevent putting excessive stress on the pump. (see Fig. 4.1)
2. A priming piping must be installed if the suction system does not
employ positive pressure, i.e. upward suction. (see Fig. 4.1)
3. The flow rate in the outlet piping should not exceed 3m/sec.
4. The ability for each component in the piping system to withstand
pressure should be calculated, to determine the maximum
allowable operating pressure.
Содержание TEM Series
Страница 1: ......