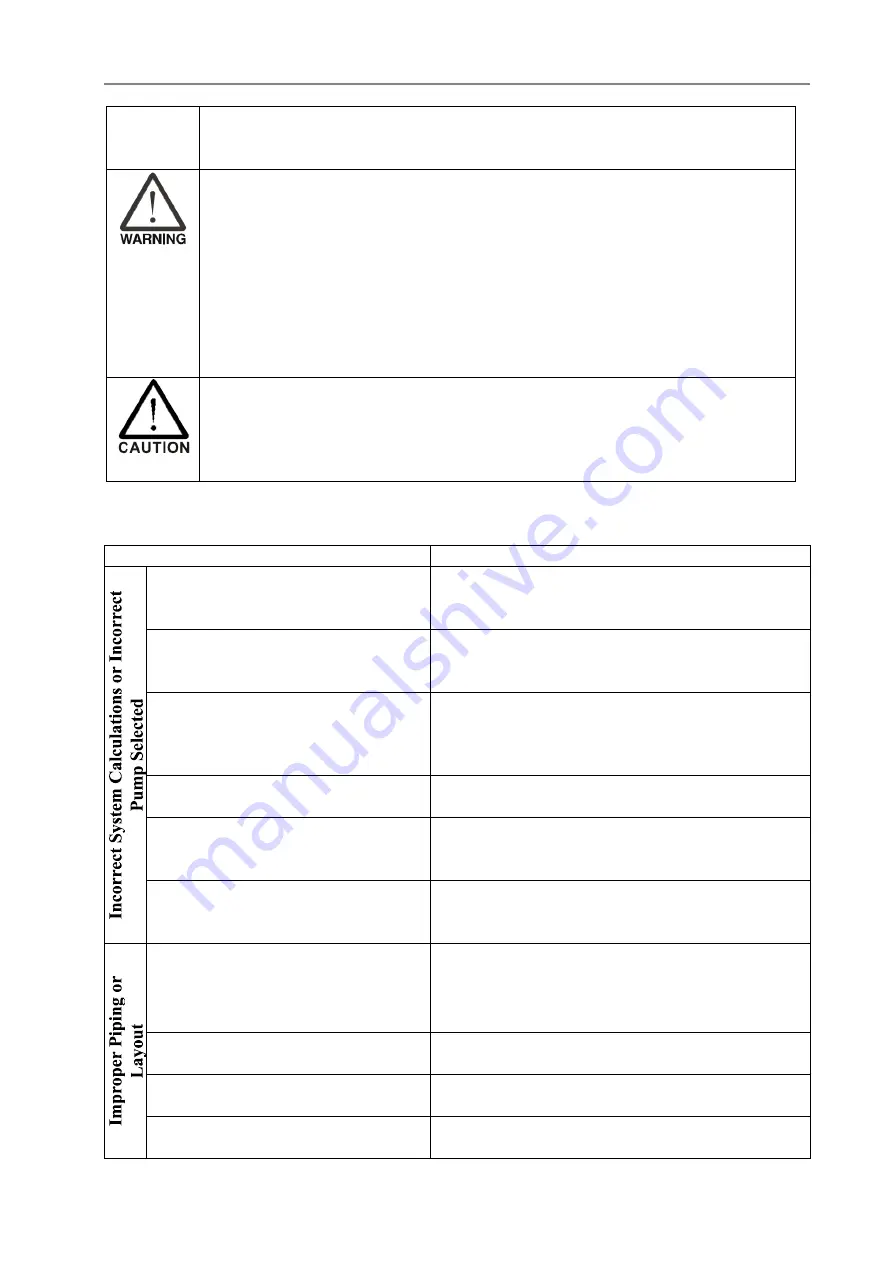
14
power supply switch to notify others that someone is “WORKING” on the
pump. Power supply mistakenly turned on during maintenance may lead to
personal injury.
1. When handling a toxic or odorant liquid, ventilate the working area well. In
addition, the operator must wear protector gear (such as a safety mask,
safety goggles, and protective gloves).
2. No remodeling: Remodeling of the pump by the user may result in serious
injury, electric shock, or damage to the pump. Do not attempt to remodel as
it is very dangerous.
3. Magnetic field hazard: Be careful not to get your hands or fingers pinched
by parts. Impeller is encapsulated strong magnet inside. While, do not let the
magnet close to the magnetic sensitive objects such as magnetic cards,
computer equipment, etc.
1. Use the right tools for any maintenance or disassembly and assembly.
2. Be careful with hazardous liquids:
If pumping dangerous chemicals, be sure to drain and wash well before
disassembling. A small amount of fluid may however remain in the internal
parts or pipe fittings.
8. Incorrect Usage and Selection
Abnormal Condition
Possible Effect/Damage
System resistance too high
or
Pump head too low
1. Insufficient or no flow.
2. Pump unable to effectively dissipate heat.
3. Excessive wear on bearing and thrust rings.
Resistance lower than expected
or
Pump head too high
1. Excessive flow.
2. Overloading of the motor.
3. NPSHa too low, resulting in cavitation.
NPSHa too low,
resulting in cavitation
1. High frequency vibration and noise.
2. Fracturing of the bearing and thrust rings.
3. Decreased pump performance and low flow rate.
4. Serious cases may result in dry-running.
Specific Gravity higher than
anticipated
1. Motor overloading.
2. Decoupling of the magnetic drive.
Viscosity higher than anticipated
1. Motor overloading.
2. Decoupling of the magnetic drive.
3. Decreased pump performance and reduced flow.
Wrong pump material selected
1. Corrosion and cracking.
2. Rapid corrosion and wearing of bearing.
3. Corrosion of the O-ring resulting in leakage.
Inlet pipe not submerged sufficiently
into the fluid or air sucked into piping
system
1. Produce high frequency vibrations and noise.
2. Fracturing of the bearing and thrust rings.
3. Reduced pump performance.
4.
Serious cases can lead to dry-running.
Air pockets in inlet piping
1. Reduced pump performance.
2. Serious cases can lead to dry-running.
Parallel pumps improperly installed
Improper suction, resulting in low efficiency,
insufficient flow, cavitation or dry-running.
Leaking foot valve or inlet piping
Fluids within pump leaks during shut-down period,
resulting in dry-running when pump is restarted.
Содержание TEM Series
Страница 1: ......