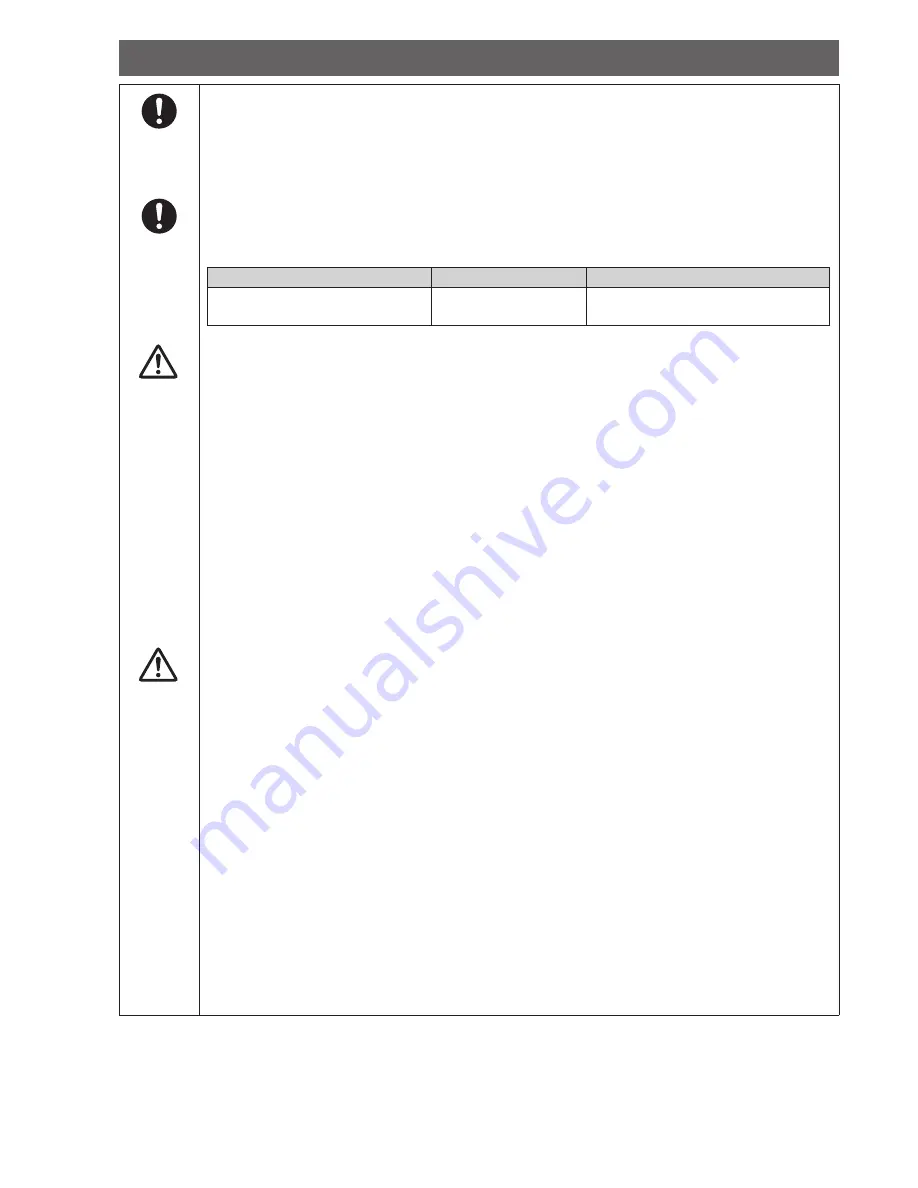
14
3. 6 Maintenance
(Continued)
3. 6. 4 Replacement of spare parts
This product should be disassembled and assembled in a clean location which is free from dirt,
waste material and dust.
Refer to section
2. 1 “Expanded View and Part List” and “MAINTENANCE” in Chapter 5 for type
and replacement procedures of spare parts.
3. 6. 5 Rust prevention procedure
Be sure to use the rust preventive agent specified blow.
<Table-7> Rust Prevention Procedure
To be applied to:
Rust preventive agent
Product Name (Manufacturer)
Plated parts
Indicator, bolts, nuts and handle shaft
Rust preventive agent
Ferro-Guard #1009
(US Ronco Laboratories, INC.)
WARNING
3. 6. 6 Countermeasures to address abnormalities
1) The work should be performed while wearing protective gear, such as a helmet, safety belt,
protective glasses, working gloves and safety shoes, in accordance with laws and regulations,
and safety provisions of business establishments.
2) When the fluid which flows through the piping is toxic, flammable or corrosive, adequate safety
measures should be taken.
3) Before retightening the pipe flanges, be sure to reduce the pressure in the piping to the atmo-
spheric pressure.
4) In case of abnormal operation, possible causes are clogging of foreign material, damage of
the Seatring, etc. If you continue to use the valve, serious accidents may occur due to dam-
age. Perform checks in accordance with the following procedures.
①
To remove foreign material, keep the disc in the full-open positon and flush fluid to remove
foreign material.
②
If normal operation is still not restored through the above procedure, damage of the seat
ring is possible.
Remove the Seatring from the piping and check the Seatring.
WARNING
3. 6. 7 Removal/Installation from/to the piping
1) Before removing this product from the piping, release the residual pressure and remove fluid
from the equipment and the piping completely. Otherwise, jetting of fluid to the outside and
unexpected movements may occur.
2) Take necessary measures so that fluid does not flow into applicable pipes accidentally during
the work.
3) When this product is removed, fluid may leak from the inside. Provide protection as required.
4) Remove/install this product from/to the piping with the product in the full-close position so that
the disc does not protrude from the face. (Refer to section
4. 1. 1 for detailed procedures.)
5) Remove all the bolts and nuts except those on the lower side. Remove the valve. At this time,
use of jack bolts in between the flanges will assist in removing the valve more easily.
3. 6. 8 Disposal
1) Do not dispose of this product by incineration. There is a possibility of generation of toxic gas
from synthetic rubber or nylon resin parts and bursting. Therefore please dispose of this prod-
uct as general industrial waste. The product does not contain materials which cannot be dis-
posed of as general industrial waste.
2) For segregated disposal, classify the parts in accordance with materials specified on drawings.
3) This product should be disposed of in accordance with laws and regulations, local government
ordinances, standards of business establishments, etc.
Содержание 304YA
Страница 28: ...27 MEMO...