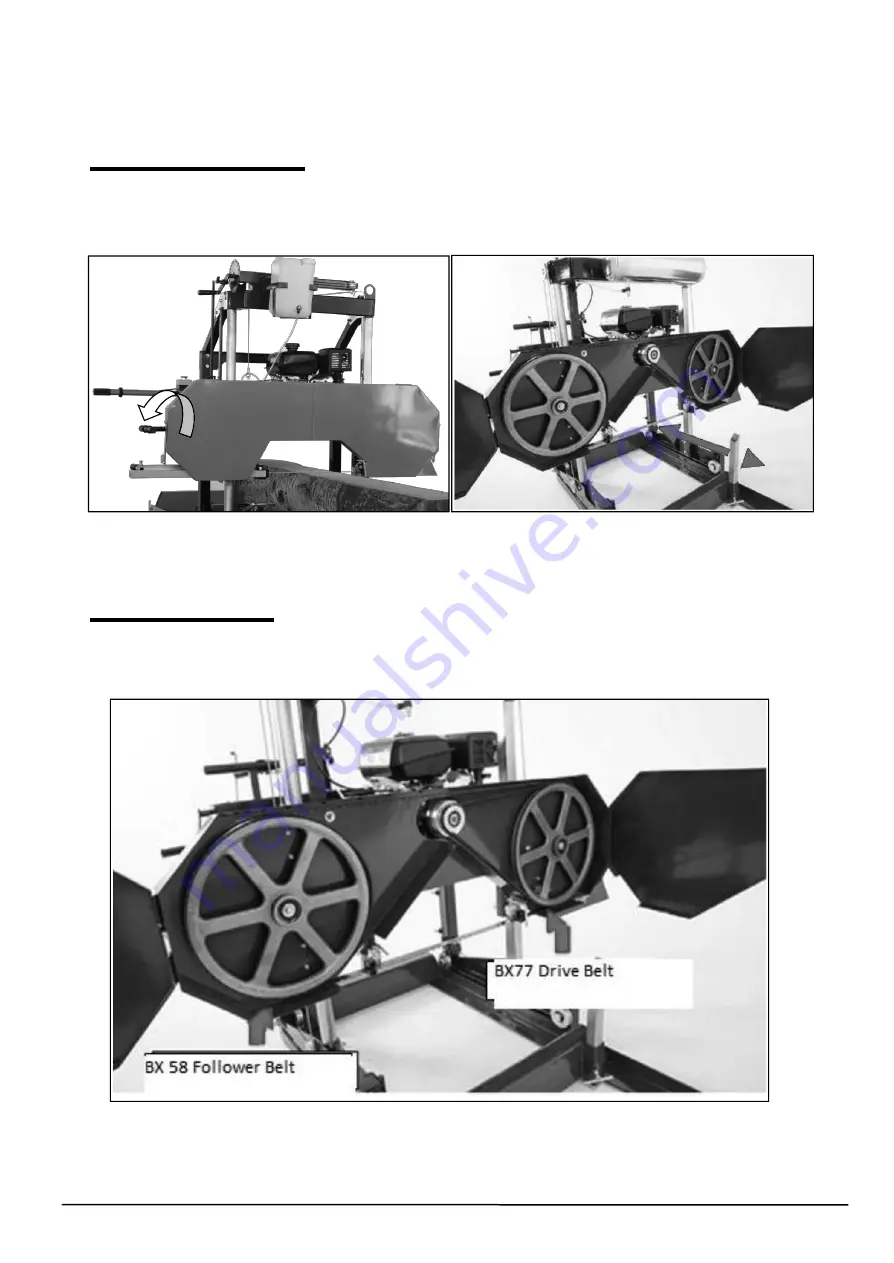
#1 – CHANGING THE BLADE
SAWMILL MAINTENANCE
Never attempt the below with the engine running. As a safety precaution, remove the spark plug cap.
Gloves and safety glasses must be worn when changing the blade.
Remove the tension in the blade by turning the “T” handle in the counter-clockwise direction and then
open the blade guard cover. The blade should now be loose and free to pull straight out the front. The
new blade can now be installed, guards closed and proper blade tension set.
#2 – REPLACING BELTS
Never attempt the below with the engine running. As a safety precaution, remove the spark plug cap.
Gloves and safety glasses must be worn when replacing the belts.
There are two rubber “V” belts on the sawmill and they should be replaced as a set. It is not advised
to replace individual belts separately. It is recommended to use a BX77 cogged belt for the drive side
and a BX58 follower belt.
WWW.TMGINDUSTRIAL.COM
P32/43
Toll Free:1-877-761-2819
Содержание Kohler TMG-PSM26
Страница 35: ...DIAGRAM ENSEMBLE A B C WWW TMGINDUSTRIAL COM P35 43 Toll Free 1 877 761 2819...
Страница 36: ...DIAGRAM A BANDWHEEL HOUSEING WWW TMGINDUSTRIAL COM P36 43 Toll Free 1 877 761 2819...
Страница 39: ...PARTS LIST B CARRIAGE WWW TMGINDUSTRIAL COM P39 43 Toll Free 1 877 761 2819...
Страница 42: ...DIAGRAM C GUIDE RAIL WWW TMGINDUSTRIAL COM P42 43 Toll Free 1 877 761 2819...