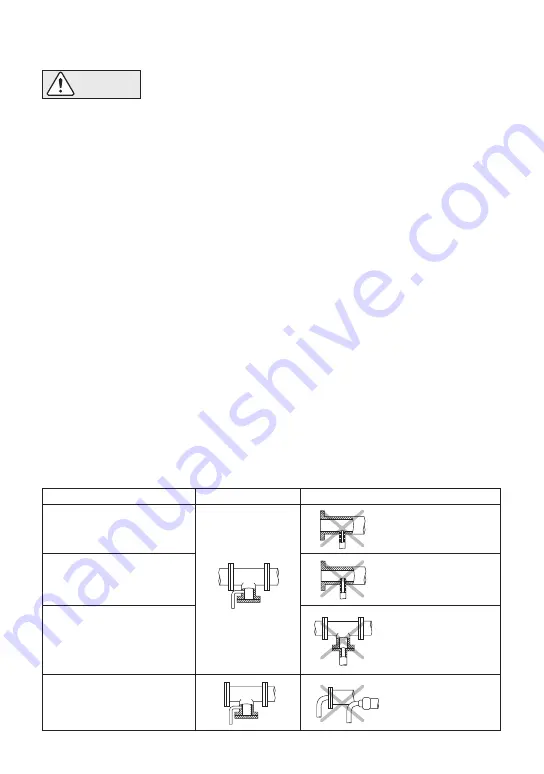
1. Before installation, be sure to remove all protective seals.
2. The trap can be installed either horizontally or vertically, but make sure the arrow on the trap
points in the direction of flow.
3. Before installing the trap, blow out the inlet piping to remove all dirt and oil.
4. Install the trap in the lowest part of the pipeline or equipment so the condensate flows naturally
into the trap by gravity. The inlet pipe should be as short and have as few bends as possible.
5. Support the pipes properly within 800 mm (2.5 ft) on either side of the trap.
6. Install a bypass valve to discharge condensate, and inlet and outlet valves to isolate the trap in
the event of trap failure or when performing maintenance.
7. Install a check valve at the trap outlet whenever the condensate discharge pipe leads to a tank
or recovery line, or whenever the condensate collection pipeline is connected with more than
one trap.
8. In order to avoid excessive back pressure, make sure the discharge pipes are large enough (the
outlet back pressure should be no more than 80% of the inlet steam pressure).
9. The use of unions is recommended to facilitate connection and disconnection of the screwed
version.
5. Proper Installation
6. Piping Arrangement
Requirement
Diameter is too small.
Diameter is too small
and inlet protrudes
into pipe.
Rust and scale flow
into the trap with the
condensate.
Condensate collects
in the pipe.
Correct
Incorrect
Install a catchpot of the
proper diameter.
Make sure the flow of
condensate is not
obstructed.
To prevent rust and scale
from flowing into the trap,
connect the inlet pipe 25 -
50 mm (1 - 2 in) above the
base of the T - pipe.
When installing on the blind
end, make sure nothing
obstructs the flow of
condensate.
• Installation, inspection, maintenance, repairs, disassembly, adjustment
and valve opening/closing should be carried out only by trained
maintenance personnel.
• Take measures to prevent people from coming into direct contact with
product outlets.
• Install for use under conditions in which no freeze-up will occur.
• Install for use under conditions in which no water hammer will occur.
CAUTION
Check to make sure that the pipes connected to the trap have been installed properly.
1. Is the pipe diameter suitable, and has sufficient space been secured for maintenance?
2. Has the trap been installed with the arrow on the body pointing in the direction of flow?
3. Have maintenance valves been installed at the inlet and outlet? If the outlet is subject to
back pressure, has a check valve been installed?
4. Is the inlet pipe as short as possible, with as few bends as possible, and installed so that the
condensate will flow naturally down into the trap?
5. Has the piping work been done correctly, as shown in the table below?
̶ 5 ̶