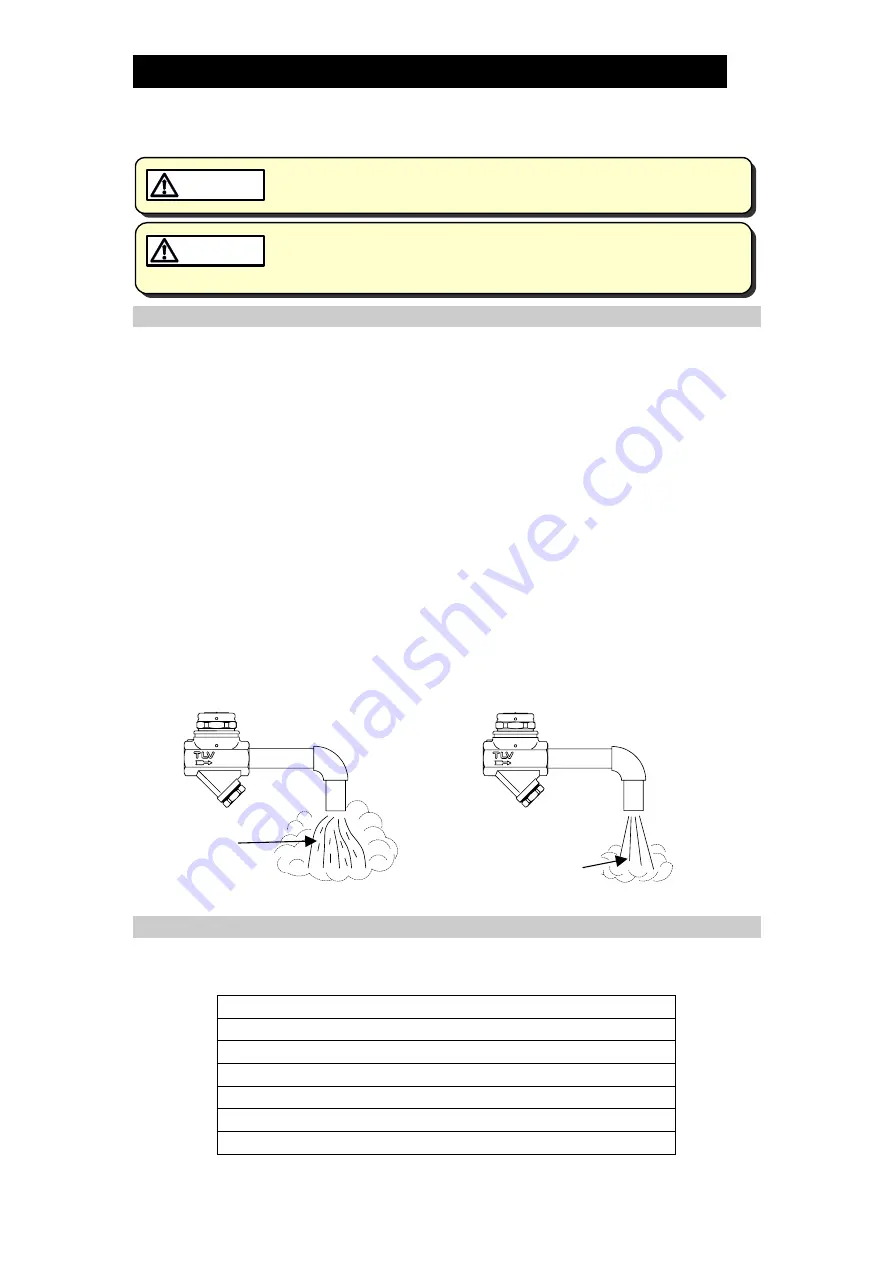
172-65400MA-01 (BD2) 21 Apr 2010
8
Maintenance
Take measures to prevent people from coming into direct contact with
product outlets. Failure to do so may result in burns or other injury from
the discharge of fluids.
CAUTION
Be sure to use only the recommended components when repairing the
product, and NEVER attempt to modify the product in any way. Failure to
observe these precautions may result in damage to the product or burns
or other injury due to malfunction or the discharge of fluids.
CAUTION
Operational Check
A visual inspection of the following items should be done on a daily basis to
determine whether the trap is operating properly or has failed. Periodically (at least
biannually) the operation should also be checked by using diagnostic equipment,
such as a stethoscope, thermometer, TLV TrapMan or TLV Pocket TrapMan.
If the trap should fail, it may cause damage to piping and equipment, resulting in
faulty or low quality products or losses due to steam leakage.
Normal : Condensate is discharged intermittently together with flash steam,
and the sound of flow can be heard.
Blocked
(Discharge Impossible)
: No condensate is discharged. The trap is quiet and makes no
noise, and the surface temperature of the trap is low.
Blowing : Live steam continually flows from the outlet and there is a
continuous metallic sound.
Steam Leakage : Live steam is discharged through the trap outlet together with
condensate, accompanied by a high-pitched sound.
(When conducting a visual inspection, flash steam is sometimes mistaken for steam
leakage. For this reason, the use of a steam trap diagnostic instrument [TLV: TrapMan] in
conjunction with the visual inspection is highly recommended.)
Parts Inspection
When parts have been removed, or during periodic inspections, use the following
table to inspect the parts and replace any that are found to be defective.
Procedure
Gaskets:
Check for warping or scratches
Screen:
Check for clogging or corrosion
Disc:
Check for scratches or wear
Air Vent Ring:
Check for scratches or wear
Disc Holder Ring:
Check for scratches or wear
Modular Valve Seat Surface: Check for scratches or wear
Flash Steam
Live Steam
White jet
containing
water droplets
Clear, slightly
bluish jet