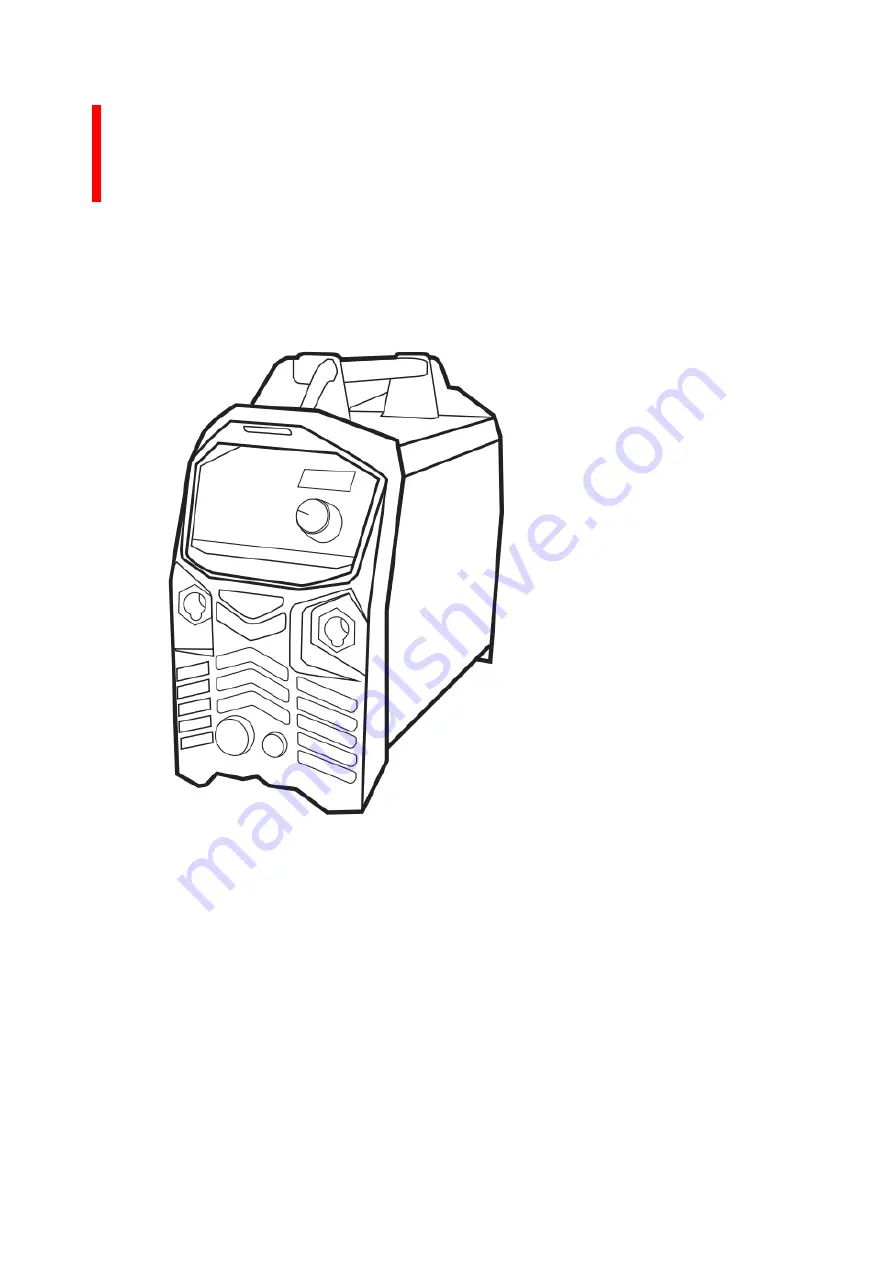
TitanTig 200 DC Pulse Operators Manual
Issue. A 0516
TitanTig
200 DC Pulse
Pro
Operating Manual
Operating manual
EN
Brugsanvisning
DA
Gebrauchsanweisung
DE
Manual de instrucciones
ES
Käyttöohje
FI
Manuel d’utilisation
FR
Manuale d’uso
IT
Gebruiksaanwijzing
NL
Bruksanvisning
NO
Instrukcja obsługi
PL
Manual de utilização
PT
Инструкции по эксплуатации
RU
Bruksanvisning
SV
操作手册
CN
English
TitanTig 200 DC Pulse
Pro
TIG/Stick Welder
Model No.
TTIG200DCP
Issue.
A 05/16
Содержание 200 DC PULSE PRO
Страница 2: ...TitanTig 200 DC Pulse Operators Manual Issue A 0516 ...
Страница 41: ...TitanTIG 200 DC Pulse Pro Operators Manual Issue A 0516 7 0 Electrical principle diagram ...
Страница 46: ...TitanTIG 200 DC Pulse Pro Operators Manual Issue A 0516 ...
Страница 47: ...TitanTIG 200 DC Pulse Pro Operators Manual Issue A 0516 ...