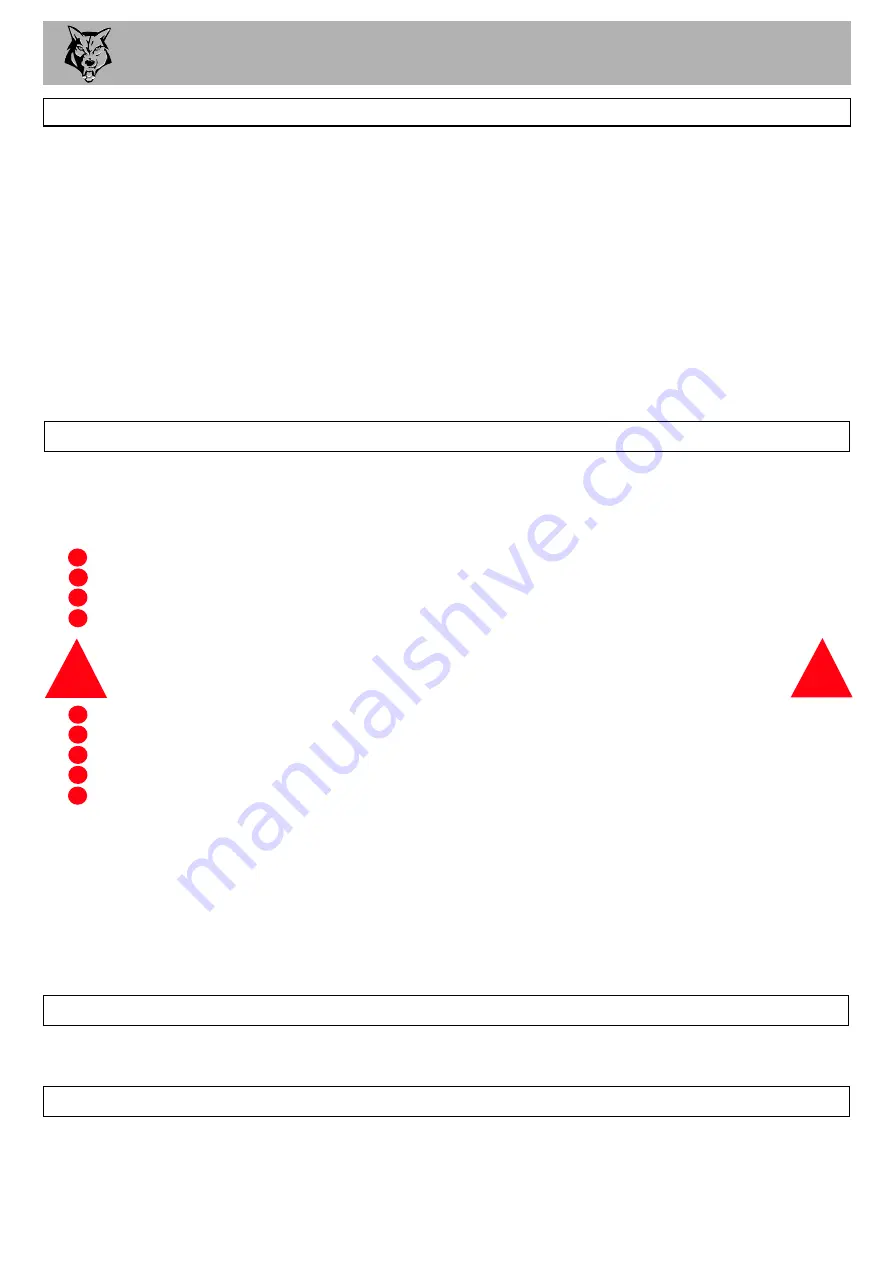
OPERATING INSTRUCTIONS
12
BLOCKAGES
Always be aware that what you are putting into the chipper must come out. If the chips stop coming
out of the discharge tube but the chipper is taking material in - STOP IMMEDIATELY. Continuing to
feed material into a blocked machine may cause damage and will make it difficult to clear.
If the chipper becomes blocked proceed as follows:
STOP
the engine and remove the keys.
REMOVE
the two rotor housing bolts.
OPEN
the rotor housing fully.
THE
material causing the blockage should fall clear.
WARNING
Do not reach into the rotor housing with unprotected hands. There are
sharp blades and any small movement of the rotor may cause serious injury.
EMPTY
loose debris from inside the rotor housing.
CHECK
that the discharge tube is clear before continuing.
THE
rotor housing does not have to be completely clear to continue.
SHUT
the rotor housing and replace both bolts securely.
RESTART
the engine.
ALLOW
machine time to clear excess chips still remaining in rotor housing before you continue
feeding brushwood. Feed in a small piece of wood whilst watching to make sure that it comes out of
the discharge. If this does not clear it, repeat the process and carefully inspect the discharge tube to
find any obstruction.
NOTE
Continuing to feed the chipper with brushwood once it has become blocked will cause the chipper to
compact the chips in the rotor housing and it will be difficult and time consuming to clear.
AVOID THIS SITUATION - WATCH THE DISCHARGE TUBE AT ALL TIMES.
!
!
CHIPPING
Wood up to 190mm diameter can be fed into the feed funnel. Put the butt end in first and engage it
with the feed roller. The hydraulic feed rollers will pull the branch into the machine quite quickly. Large
diameter material will have its feed rate automatically controlled by the no stress unit.
Sometimes a piece of wood that is a particularly awkward shape is too strong for the feed rollers to
break. This will cause the top roller to either bounce up and down on the wood or both rollers to stall.
If this occurs press the
BLUE REVERSE
button until the material has been released. Pull the material
out of the feed funnel and trim it so the chipper can handle it.
Both feed rollers should always turn at the same speed. If one or both rollers stop or suddenly slow
down it may be that a piece of wood has become stuck behind one of the rollers. If this occurs press
the
BLUE REVERSE
button and hold for 2 seconds - then repress
GREEN FEED
button. This should
enable the rollers to free the offending piece of material and continue rotation at the correct speed. If
the rollers continue to stall in the 'forward feed' or 'reverse feed' position push the
RED STOP
BUTTON
, turn engine off, remove ignition key and investigate.
HYDRAULIC OIL LEVEL INDICATOR
This can be viewed through the wall of the tank. Maximum and minimum marks are provided.
FUEL LEVEL INDICATOR
The fuel level can be seen through the wall of the fuel tank.