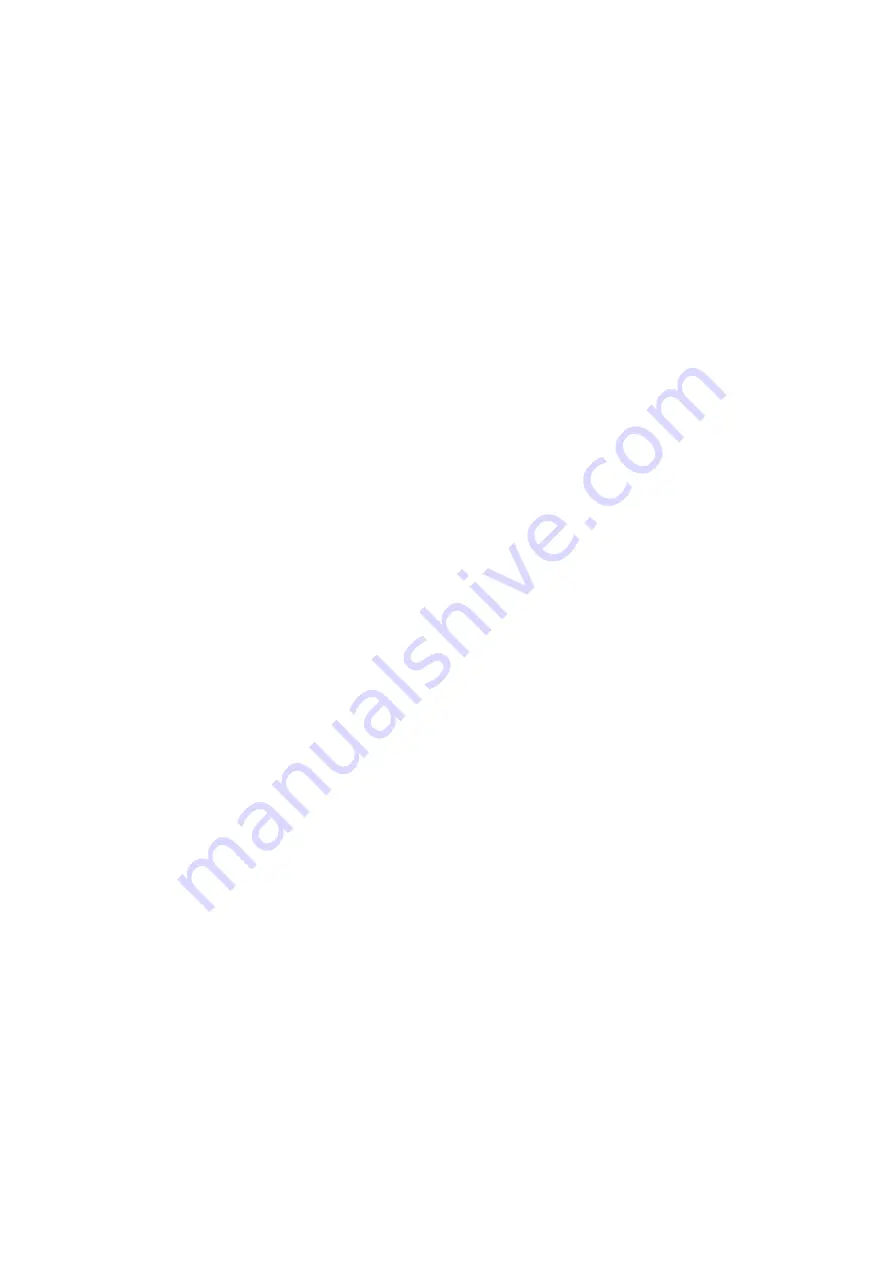
3
axis of output shaft is vertical with the floor.
2.1.2 Side: the central axis of output shaft is parallel to the floor. It is much better if axis of
motor is parallel to the floor at that time.
2.2 The connection between electric actuator with the valve
2.2.1 Take the spline joint out of the driving shaft and get it properly connected with valve (if
no requirement of the dimension of the inner hole and key is made while placing order, processing
shall be made by user).
2.2.2 Check up the valve’s position (end position is the best), and if the valve’s position is
different from the driving shaft’s position, to manually operate the electric actuator to get the
valve’s position same as that of driving shaft. (The position of the driving shaft can be seen from
the dial)
2.2.3 To install the electric actuator with valve, making the flange hole of the two to be aligned
with each other. To make electric actuator to be fastened with valve through bolts. The depth of
the threaded section on the bolts shall comply with standard requirement (after the electric
actuator is well adjusted, the dwell pin can be placed between the valve and the electric actuator).
3.Electric wiring
Electric schematic diagram and electric wiring
The Operation Manual is attached with an Electric schematic diagram which is applied for the
electric actuator. Wire numbers and terminal numbers are marked on the diagram which could be
used by user to connect wire.
3.1 Electric wiring for Standard type (see Fig.1)
Remove the “the control box cover 1” and “sealing plug2”; put the power cable and control
cable through the two G1’’ sealing wire inlet plugs(provided by user) which are matched with
thread holes of “Case4”
;put the cable into the control cavity of the electric actuator. Connect the
core of cables with “connection wiring terminal board 3”, and wiring should be reliable and shall
not be exposed. Pull the cable outwards in a proper amount to ensure it will not interfere with
other operating components in the cavity. Rotate the input sealing wire plug into the thread hole
of the case body; firmly screw the gland nut on the sealing wire plug so as to ensure the sealing
performance of controller.
3.2 Electric wiring for Integral type of electric actuator (see Fig.2)
Remove the “Control case 2” and “Wiring case 3”; unscrew the thread plug and the inner
sealing plug of “Sealing inlet wiring plug 4”. Put power cable and control cable through the
sealing inlet wire plug and pull them into “Integral controller’s case 1”. Connect cable’s core wire
with “Wire connecting terminal 5” according to Electric Schematic Diagram and Terminal
Number Table. The wires shall be reliable and cannot be exposed to the outside. Rotate and
tighten the thread plug on the “Sealing inlet wire plug 4” against cables, ensuring the sealing of
the controller.
3.3 Electric wiring for Explosion-proof type and Integral explosion-proof type (see
Fig.3, 4)
2-G1’’ sealing plug is applied at the inlet wire port for the Explosion-proof type and Integral
explosion-proof type. Remove “Wiring box case 1” and “Sealing plug 2” before wiring; put the
power cable and control cable through explosion-proof sealing inlet wire plug (provided by user)
which is matched with thread holes of “Wiring box3”. Connect cable’s core wire with
“Explosion-proof terminal board 4” according to Electric Schematic Diagram and Terminal
Number Table. The wires shall be reliable and cannot be exposed to the outside. Rotate and
tighten the thread plug on the “Sealing inlet wire plug” against cables, ensuring the sealing of the
controller.
Note: 1. The sealing plug shall be sealed properly in any working environment, even the product
is not working. This product has been strictly examined before factory delivery. The product shall
Содержание NQB1
Страница 10: ...8 Fig 1 Fig 3 Fig 2 ...
Страница 11: ...9 Fig 4 ...